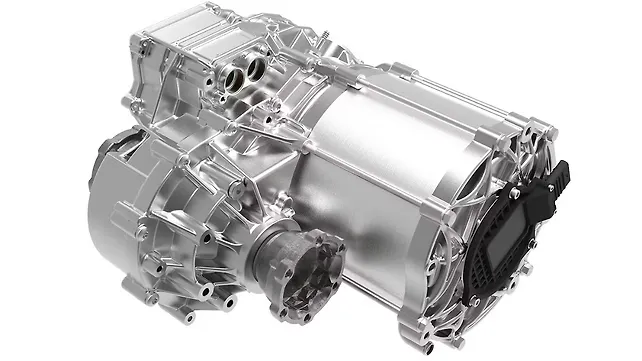
Vitesco Technology, a leading international provider of modern drive technologies and electrification solutions, has showcased its new generation highly-integrated electric axle drive at the 13th Transmission Symposium China organised by SAE.
According to the company, the EMR4 (Electronics Motor Reducer) offers high power density, compact dimensions, and low weight. The comprehensive platform covers power requirements from 80 kW to 230 kW. Utilising the development and industrialisation expertise from the successful EMR3 and previous models, the new platform shows a high level of integration, modularisation, scalability, and standardisation. It allows vehicle manufacturers worldwide to offer different power levels of the drive in one model without having to touch interfaces or mounting points. Compared to the award-winning EMR3, the EMR4 is even more energy efficient as it weighs 25% less at the same power level and is further cost optimised.
Thomas Stierle, Executive Vice President Electrification Technology business unit, Vitesco Technologies, said that with electromobility gaining momentum, the key to support this megatrend lies in high efficiency and relands well as affordability for high-performing electric drive systems. The company has anticipated this with the EMR4 design, which offers a combination of benefits that will meet and exceed the requirements of vehicle manufacturers around the world.
Supporting electrification
The big task for the automotive industry is to bring electrification to many new vehicle brands, segments, and models.
Gunter Mühlberg, head of Product Management Axle Drives, Vitesco Technologies, said the greatest possible scalability of electric drives plus the highest efficiency is the market demand. The EMR4 platform perfectly fits this bill, which is already the fourth generation of the highly integrated ‘Electronics Motor Reducer’ offered by the company, he added.
Although EMR3 already set ambitious benchmarks in weight, compactness, and power density, EMR4 surpasses the current third generation. In addition, it delivers up to 5% increased efficiency of the whole axle drive compared with the predecessor generation. “This is the result of consistent system optimisation on detail level within numerous effect chains in the axle drive,” Mühlberg added.