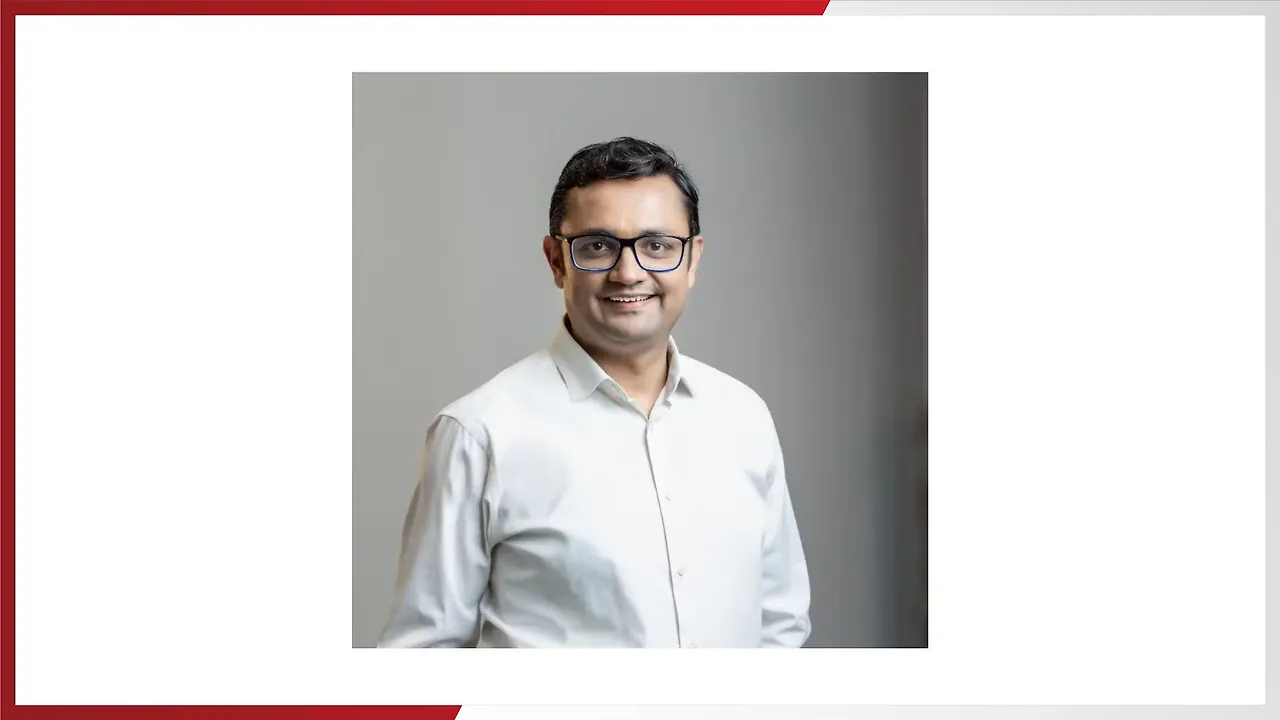
Vector Consulting Group has released a comprehensive report that critically assesses the implementation of Just-In-Time (JIT) inventory practices across the Indian automotive manufacturing sector. Despite decades of global validation and successes attributed to JIT, the study reveals that no Indian Original Equipment Manufacturer (OEM) has fully integrated this system throughout their end-to-end supply chain.
JIT Adoption: A Closer Look At Indian Auto Manufacturers
Originally developed by Toyota in the 1970s, JIT is a strategy designed to increase efficiency, decrease waste, and reduce inventory costs by receiving goods only as they are needed in the production process. While JIT has been globally adopted with significant success, the adaptation within the Indian context appears fragmented.
The report highlights that most Indian auto manufacturers rely on a hybrid model that combines JIT with traditional inventory management practices, such as forecasting and scheduled production, rather than a true pull-based system responsive to real-time market demand.
Challenges & Barriers In Full JIT Implementation
The study identifies several obstacles preventing the full adoption of JIT in India. These include the prevalence of the bullwhip effect among smaller players in the supply chain, leading to operational disruptions and financial strain due to sudden shifts in orders and inflated inventories. Additionally, while some multinational OEMs have managed to implement a zero-inventory model at the dealership level, this remains an exception rather than the norm.
Achal Saran Pande, a spokesperson for Vector Consulting, elaborated on the findings, stating, 'To position itself as a global auto manufacturing hub, India must refine its supply chain practices. The current model, which lacks a comprehensive pull-based system, leads to increased costs, stockpile ups, and reduced capital turnover.'
Proposed Solutions For Enhancing JIT Effectiveness
Vector Consulting suggests a reimagined approach to JIT that includes completely abandoning forecasts for daily inventory decisions, dampening demand variability with strategic buffer placements, and implementing a system where 'buffers replenish buffers' based on actual consumption. This model aims to protect the supply chain from the variabilities of an increasingly complex market environment, characterised by a surge in model variations and extended global supply chain lead times.
The report underscores the need for Indian auto manufacturers to adopt more sophisticated, end-to-end pull systems that not only align with JIT principles but also adapt to the unique challenges of the Indian market. By adopting these strategies, OEMs can enhance their operational agility, reduce wastage, and ultimately, improve profitability.
As the Indian auto industry continues to evolve, embracing these recommendations could be crucial in ensuring its competitive edge on the global stage, fostering innovation, and contributing to sustainable economic growth. Vector Consulting Group's insights are poised to catalyse a significant shift in how JIT is perceived and implemented across the sector, potentially leading to more robust, responsive, and efficient supply chain systems in the future.