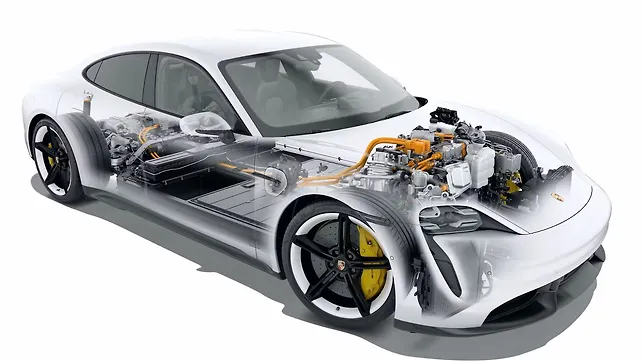
Last year, German super luxury and sports car manufacturer Porsche unveiled its first electric sports car Taycan S. The electric sports car gained popularity because of its sleek design and new technology involved, but enthusiasts termed it as one of the most important powerful cars of all time. Not just this, the Center of Automotive Management (CAM) declared the Taycan, the world’s most innovative model of 2020.
The Porsche Taycan S, which comes with a 390-416 km range, is energised with a collective torque of 12,000 Nm on all four wheels at once. The concentrated power is discharged in full without delay, and the thrust from the two electric motors on the front and rear axles remain virtually unchanged up to top speed.
Porsche did not come up with this concept just yesterday – or even the day before. In fact, it was more than 120 years ago.
At that time, a young Ferdinand Porsche achieved a world first when he developed electric vehicles with steered wheel-hub motors. The possibilities offered by electromobility spurred on his sporting ambition, and his racing car became the world’s first all-wheel-drive passenger vehicle.
What makes the Porsche Taycan S the most innovative model of 2020?
The electric motor and two-speed gearbox (front) are arranged parallel to the rear axle. The power electronics are located on top.
More sophisticated machines have long since replaced the simple DC motors of yesteryear. However, the basic physical principle has remained the same: magnetism. A magnet always consists of a north and a south pole. Unequal poles attract; equal poles repel.
On the one hand, there are permanent magnets based on the interplay of elementary particles. On the other, magnetic fields also arise every time an electric charge is moved. The current-carrying conductor in an electric motor is arranged to form a coil to amplify the electromagnetism in play. Electromagnets and – depending on the design of the motor – permanent magnets are arranged on two components. The stationary part is called the stator, while the rotating part is the rotor, which turns when attractive and repulsive forces are generated by periodically switching the electrical voltage on and off.
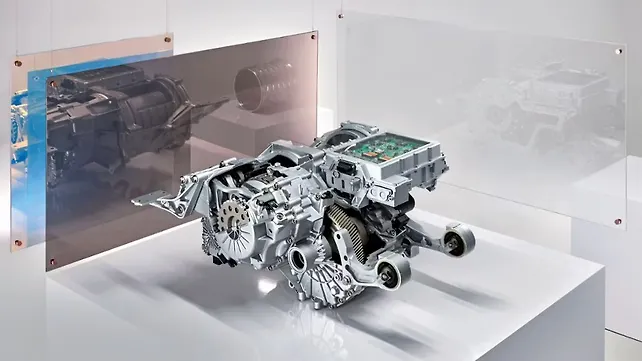
Not every type of electric motor is suitable for propelling a vehicle. For example, Porsche makes use of the permanently excited synchronous machine (PSM). Compared to the predominantly used design – the cheaper asynchronous machine (ASM) – the PSM offers higher continuous output because it overheats less easily and therefore does not have to be turned down.
Porsche’s PSM is supplied and controlled via power electronics with three-phase AC voltage: the speed of the motor is determined by the frequency at which the alternating voltage oscillates around the zero point from plus to minus.
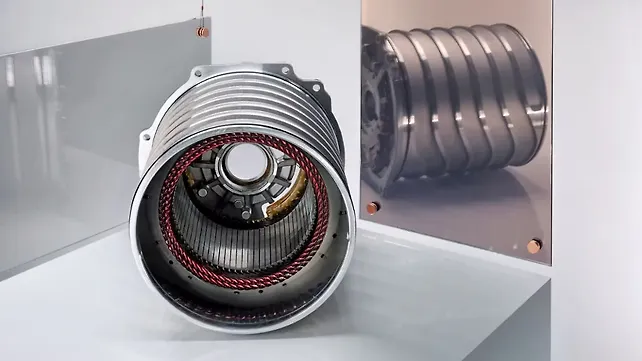
In Taycan motors, the pulse inverter sets the frequency of the rotating field in the stator, thereby regulating the speed of the rotor.
Centrepiece
The stator of the e-motor essentially consists of circular sheet-metal discs layered into a tube and the copper coils. U-shaped bent wires are inserted into gaps in the tube and connected to each other.
The rotor contains high-quality permanent magnets with neodymium-iron-boron alloys that are permanently magnetised during the manufacturing process via a strong directional magnetic field. The permanent magnets also enable a very high degree of energy recovery through recuperation during braking.
The electric motor goes into the regenerative way in overrun mode while the magnets induce voltage and current into the stator winding. As a result, the recuperation performance of the Porsche e-motor is the best among the competition.
Technology-driven to its very limits: this Porsche gene is reflected in a special feature of the Taycan motors, known as the hairpin winding. Here, the coils of the stator consist of wires that are not round but rectangular. And unlike classic winding processes where the copper wire is obtained from an endless reel, hairpin technology is known as a forming-based assembly process.
This means that the rectangular copper wire is divided into individual sections and bent into a U-shape, similar to a hairpin. These individual ‘hairpins’ are inserted into the stator laminations in which the winding is mounted so that the surfaces of the rectangular cross-section lie on top of each other. It made the front-axle drive of the Taycan to be even more space-saving than the drive unit in the rear. The motor and gearbox are arranged coaxially; the rotor, gearbox, and axle shafts are in line.
This is the decisive advantage of hairpin technology as it allows the wires to be packed more densely, thereby adding more copper to the stator. While conventional winding methods have a copper fill factor – as it is known – of around 50%, the technology used by Porsche has a fill factor of almost 70%. As a result, it increases power and torque with the same installation space.
The ends of the wire hairpins are welded together by laser, creating the coil. Another important advantage is that the homogeneous contact between adjacent copper wires improves heat transfer and can cool the hairpin stator much more efficiently.
Electric motors convert more than 90% of the energy into propulsion. But just as in an internal combustion engine, the losses are converted into heat that must dissipate. That is why the motors have a cooling water jacket.
To precisely control a permanently excited synchronous motor, the power electronics must know the exact angular position of the rotor. This is what the resolver is for. It consists of a rotor disc made of field-conducting metal, an exciter coil, and two receiver coils.
The exciter coil generates a magnetic field that is transmitted via the encoder to the receiving windings. In addition, it induces a voltage in the receiving coils, the phase position of which is shifted proportionally to the rotor position.
The control system can use this information to calculate the exact angular position of the rotor. This control system, known as the pulse inverter, is the culmination of Porsche expertise. It is responsible for converting the battery's direct current at 800 volts into alternating current and supplying it to the two e-motors.
The rotor is filled with permanent magnets arranged in a V-shape. Porsche was the first manufacturer to implement a voltage level of 800 volts. Originally developed for the Porsche 919 Hybrid race car, this voltage now reduces weight and installation space in series production thanks to leaner cables, enabling shorter charging times. The electric motors reach up to 16,000 revolutions per minute.
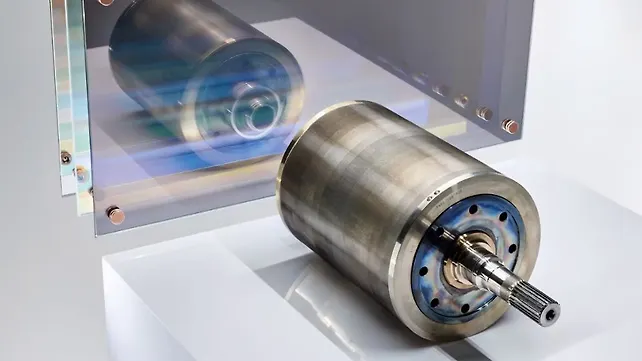
The front and rear drive units have their transmission to make optimum use of this speed range for Porsche’s signature spread between dynamics, efficiency, and top speed. The Taycan is the first electric sports car ever to have a transmission with two shiftable gears on the rear axle, the first of which has a very short reduction ratio. On the front axle, an input planetary gearbox transmits power to the wheels.
These combine to give the Taycan Turbo S its mighty powers. At the front axle, the gear ratio translates the 440 Nm generated by the electric motor to around 3,000 Nm at the wheels. Some 610 Nm from the rear-axle motor are multiplied in first gear to about 9,000 Nm of axle torque. The task of the longer-ratio second gear is to ensure efficiency and power reserves at high speed.
This is pioneering technology, applied to the smallest detail – and a continuation of Porsche’s innovation tradition in the electric drive age.