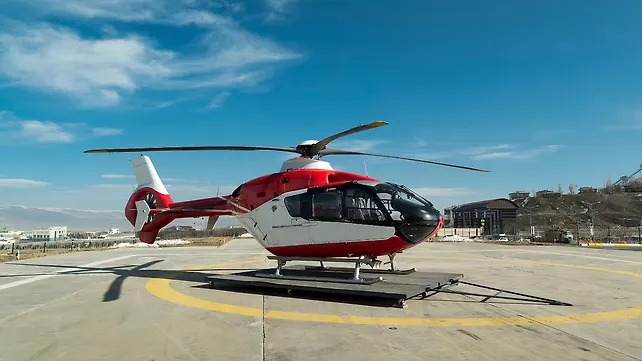
As part of its indigenous helicopter development programme for helicopter engine application, the Defence Research and Development Organisation (DRDO) has developed single crystal blades technology.
This is part of a programme taken up by the Defence Metallurgical Research Laboratory (DMRL), a premium laboratory of DRDO, to develop five sets of single crystal high pressure turbine (HPT) blades using a nickel-based super alloy. Each set comprises of 60 blades, amounting to 300 blades in total.
DRDO has already supplied 60 of these blades to Hindustan Aeronautics Limited (HAL), while the supply of remaining four sets will be completed in due course.
Helicopters used in strategic and defence applications need compact and powerful aero-engines for their reliable operation at extreme conditions. To achieve this, the state-of-the-art single crystal blades have been developed using complex shape and geometry. These are being manufactured out of Nickel-based superalloys capable of withstanding high temperatures of operation.
Very few countries in the world, including the USA, the UK, France and Russia, have the capability to design and manufacture such Single Crystal (SX) components, claimed a Ministry of Defence, Government of India release.
Complex Technology
The DMRL undertook this task based on its expertise gained during the development of such a technology for an aero-engine project earlier. Complete vacuum investment casting process to realise the blades, including die design, wax pattering, ceramic moulding, actual casting of components non-destructive evaluation (NDE), heat treatment and dimensional measurement, has been established at DMRL, said the statement.
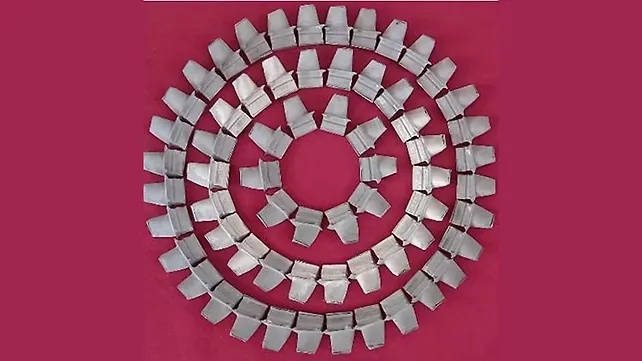
The DMRL had to formulate special ceramic composition for making strong ceramic moulds, which can withstand metallostatic pressure of liquid CMSX-4 alloy at 1,500° C and above during casting operation. The challenge of maintaining the required temperature gradient has also been overcome by optimising the casting parameters.
A multi-step vacuum solutionising heat treatment schedule for complex CMSX-4 superalloy to achieve the required microstructure and mechanical properties has also been established. Further, a stringent non-destructive evaluation (NDE) methodology for the blades along with the technique for determining their crystallographic orientations has been developed by DMRL, the release said.