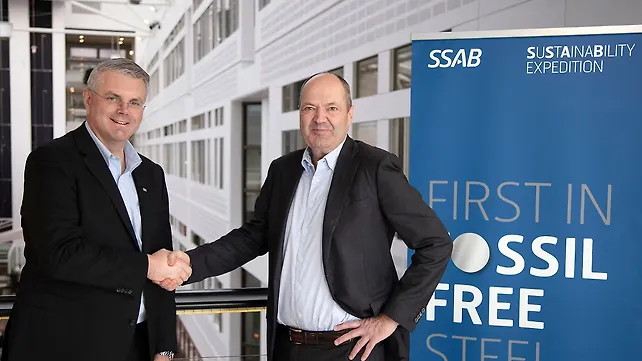
Leading global safety systems manufacturer Autoliv announced on Monday that it has initiated a collaboration with the leading steel manufacturer SAAB to research and develop fossil-free steel components for automotive safety products, such as airbags and seatbelts.
The collaboration enables Autoliv to be at the forefront in producing automotive safety products with fossil-free steel from SSAB. A new process aims to replace coking coal, traditionally needed for ore-based steelmaking, with hydrogen. The result will be unique: the world's first fossil-free steelmaking technology with no carbon footprint.
SSAB aims to start supplying the market with fossil-free steel at a commercial scale in 2026. In 2016, SSAB, LKAB and Vattenfall joined forces to create HYBRIT. A pilot plant has already produced smaller volumes of iron using hydrogen. On August 18, SSAB showcased the first steel made of hydrogen reduced iron.
Mikael Bratt, President and CEO, Autoliv, said, 'As the first automotive safety supplier, we are committed to becoming carbon neutral in our own operations by 2030 and furthermore aim for net-zero emissions across our supply chain by 2040. This means reducing our carbon emissions through use of renewable electricity in our own and supplier operations, improving energy and materials efficiency and adopting low carbon logistics and low carbon materials. We are now turning our commitment into action and are well-positioned to continue supporting our customers and partners to reach their sustainability goals. Gradually switching to fossil-free steel in our products is an important step towards achieving our climate targets.'
Martin Lindqvist, President and CEO, SSAB, said, 'We are looking forward to working with Autoliv and to start the process of research and development of innovative fossil-free steel components for their automotive safety products. We are initiating a number of pilot projects together with Autoliv with the aim to reduce climate impact and strengthen competitiveness.'