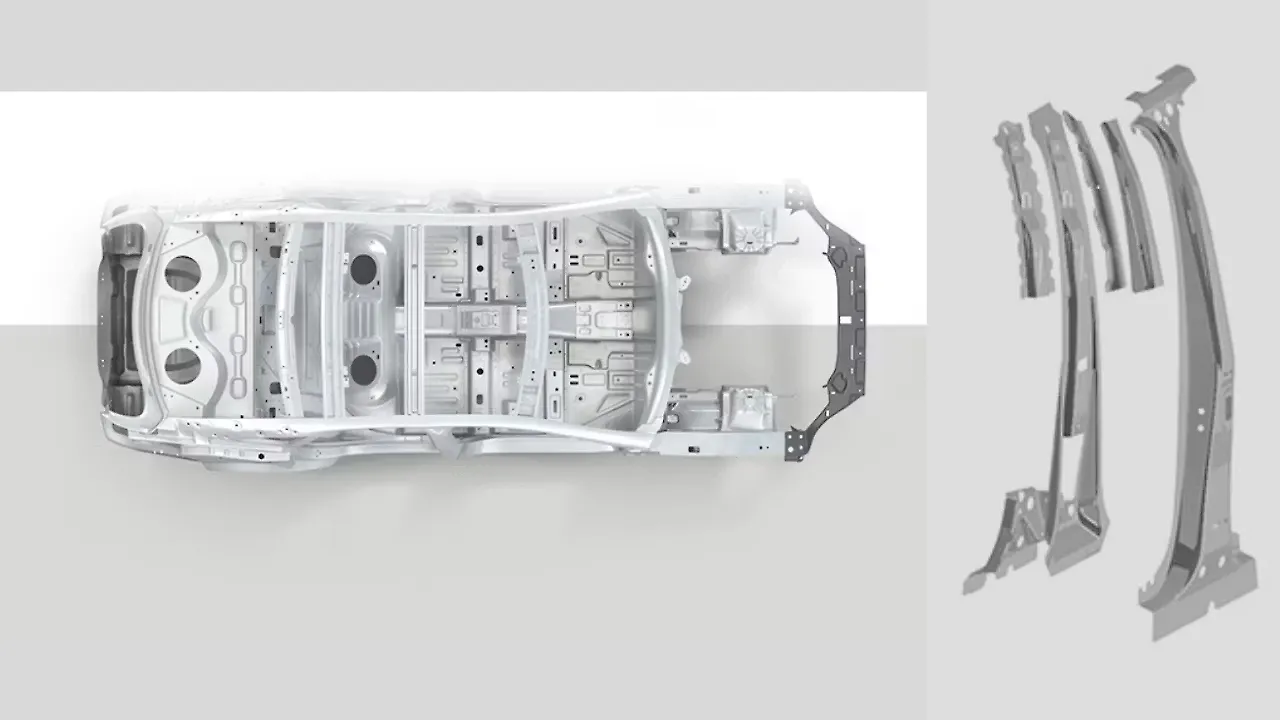
Designing a new aluminium door for C-segment SUV and passenger vehicles can meet or exceed safety and other customer performance criteria to reach 45% weight savings, states a study conducted by Alumobility.
A global ecosystem of leading aluminium and downstream technology partners, Alumobility supports automotive manufacturers in creating lighter, safer, smarter and more sustainable vehicles.
According to the results of its technical study demonstrating affordable lightweight through the proposed conversion of a mass-produced C-segment SUV passenger door from steel to aluminium, the non-profit organisation said, while the study focused on a mid-size SUV door, it expects comparable results for other door architectures as well.
Automotive companies have constantly been working on lightweight as it improves fuel economy and helps contain emissions. As they look for ways to lightweight vehicles at a competitive cost throughout the manufacturing process, the adoption of aluminium doors has increased exponentially.
Over the last two decades, adoption has grown from use in the premium segment to millions of aluminium doors produced annually, primarily in the booming SUV, pick-up truck and battery electric vehicle markets.
According to Alumobility, the next-generation aluminium door design can offer greater value given the lower gauges and higher strength levels through new innovative aluminium alloys that are now available. Moreover, these lightweight doors would also be highly recyclable at a vehicle's end of life, contributing to overall sustainability, reducing CO2 emissions and enabling a more circular economy, the firm said.
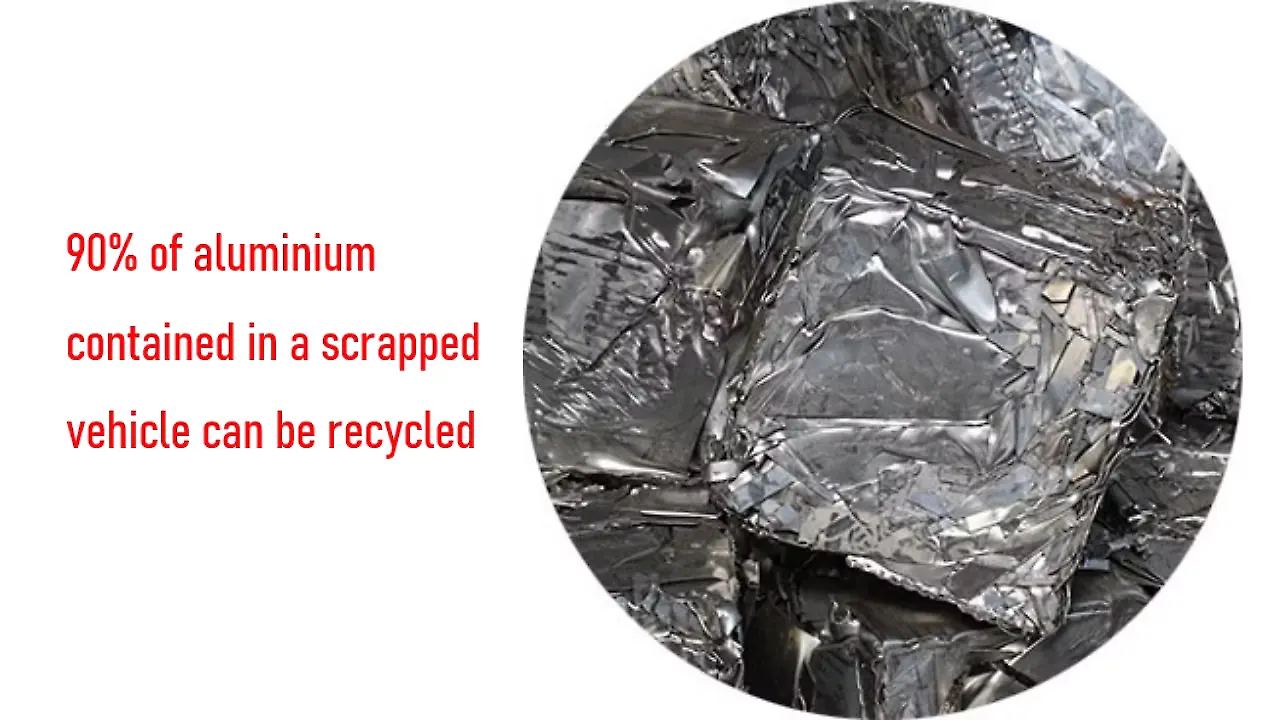
Material utilisation
By using aluminium, a vehicle’s weight can be reduced by up to 40% when compared to steel. A game changer for the reduction of fuel consumption and resulting CO2 emissions.
Alumobility stated that recent advancements in material utilisation, processing and joining allow aluminium doors to be more cost-effective than ever. In addition, with innovative joining techniques, fewer parts may be required, further reducing complexity and assembly time.
For instance, the new aluminium door design enables breakthrough performance via better formability and higher strength. However, customer targets for visual obstruction, ingress-egress and frame stiffness are maintained, the report added.
Mark White, Executive Director, Alumobility, said the latest research indicates that the next-generation aluminium doors can offer automakers affordable, lightweight solutions built for a circular economy. 'Through collaborative technical projects like this, Alumobility will help fulfil the promise of a lighter, more efficient, more sustainable mobility future benefiting automakers and consumers, he added.
High-strength B-pillar
Founded to focus on proven technical solutions to advance the adoption of aluminium automotive body sheets, Alumobility has also worked on the B-pillar, which is one of the most complex parts of the vehicle structure. Due to its importance in both integrity and safety, it has traditionally been very heavy. Alumobility aimed to replace this component in order to lightweight the vehicle without compromising on its core requirements.
To test its premise, Alumobility used a popular mass-production electric vehicle, designing high-strength aluminium B-pillars to test side-by-side with the current steel solution. By using high-strength 6XXX aluminium alloys, Alumobility provides a path to lightweight in essential safety areas. In addition, it saved about 31% of the weight of the component. Interestingly, these alloys are compatible with other aluminium alloys used on production vehicles to simplify end-of-life recycling.
Photo courtesy: Alumobility.