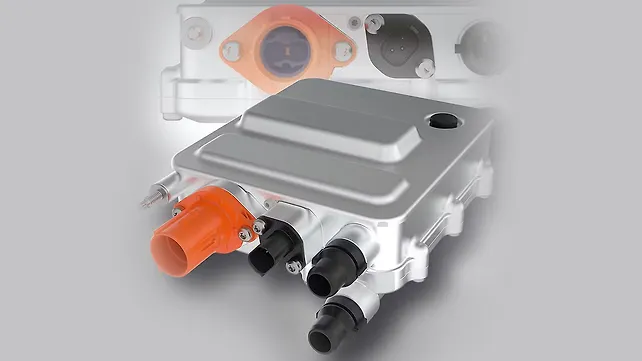
The increasing vehicle electrification is a challenge for the heat management of modern passenger cars. Mainly during winter conditions, auxiliary heating systems are required to ensure maximum heating performance. These solutions have to meet high standards, as they have to deal with the absence of exhaust heat. They also need to be energy-efficient to avoid negative impacts on efficiency, driving range and acceleration.
For this reason, automakers are increasingly demanding innovative solutions for efficient heating concepts, which BorgWarner’s High-Voltage Coolant Heater (HVCH) can provide. The intelligent heat management solution ensures an improved battery-operated range and also works fast in providing a comfortable cabin climate, regardless of outside temperatures.
Battery and Thermal Management
The predominant battery technology for electric vehicles today and in the foreseeable future is lithium-ion batteries with liquid electrolytes. Worldwide, experts are working on advancing this technology so that the lithium-ion batteries deliver better power density and performance. The ultimate goal of research is to improve criteria such as durability, safety and recycling possibilities as well as meeting the industry’s requirements for cost-effectiveness.
In order to function as an Energy Storage System (ESS) for electric vehicles, lithium-ion cells are assembled as modules to begin with. Afterwards, they form battery packs of interconnected cells customised according to particular energy requirements. Since vehicle acceleration and deceleration cycles and other service demands have a huge impact on the temperature, as the battery’s chemical reaction during these operations generates heat, a battery management system (BMS) has to ensure monitoring and control of said temperature.
In addition, the BMS controls all other operations of the battery pack, including charching and discharging the ESS, cell voltage monitoring and balancing, battery protection and diagnosis. An efficient heating and cooling cycle within the BMS, consisting of an expansion tank, a coolant pump and a cooler, is employed to maintain the optimum temperature of the battery pack. For the task of thermal management in electric vehicles, BorgWarner provides numerous battery and cabin heaters. The latest addition to the portfolio is the HVCH.
High-Voltage Coolant Heaters (HVCH)
In an electric car, with no exhaust heat from a combustion engine, BorgWarner’s HVCH (with power variants ranging from 3 to 10 kW) provides heat for the temperature management system of battery pack and cabin. Vehicle range as well as battery life are also improved by this innovative technology as it supports battery conditioning. Furthermore, the temperature distribution between battery packs and cells remains continuously homogenous due to the low thermal mass that ensures fast reaction times for heating up and cooling down.
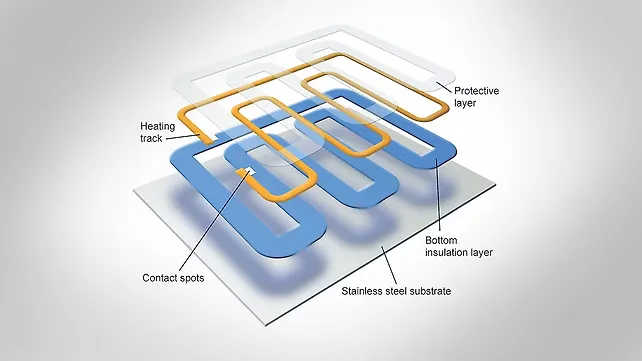
BorgWarner’s HVCH heating technology relies on long-lasting Thick Film Heating Elements (TFE), with a substrate made of stainless steel carrying the dielectric layers and the heating resistors (Fig 1). Available in “single-plate” and “dual-plate” variants, both with high power density at the TFE, the solution also enables integrated hot plate temperature measurement (Fig 2a & 2b).
Their solid aluminum die-cast housing is resistant to thermal shock, vibrations, oscillations or mechanical stress and provides electromagnetic shielding. BorgWarner’s intelligent heating solution includes sophisticated safety features to prevent thermal events like overheating: Designed to comply with the latest safety requirements, the system will switch-off automatically as soon as it detects an error.
Single and Dual-Plate Versions
The new HVCH is available in two versions: the single-plate to provide battery conditioning or cabin heating and the dual-plate HVCH providing both at the same time. The former consists of one hot plate and needs internal combustion engine waste heat in order to heat the cabin, when the BMS operation is employed exclusively to control the battery pack heating.
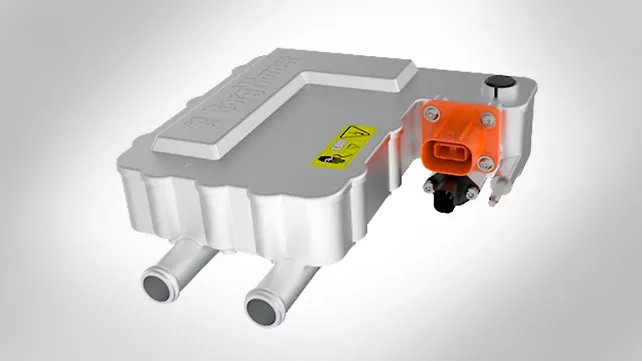
The latter is designed with two hot plates and is particularly suitable for electric vehicles as it can generate battery conditioning and cabin heating at the same time. By means of the dual-plate, the HVCH offers up to 80 % more heat transfer surface. In addition, there are minimal heat losses, since the heating modules are covered with coolant. As a result, the dual-plate version is more efficient. It improves battery performance by providing consitent temperature distribution inside the battery packs.
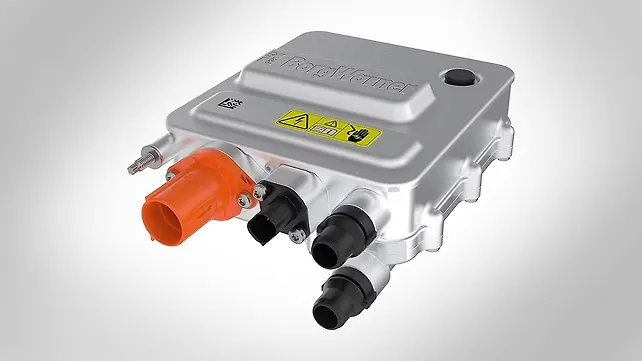
In practice: A 5 kW version with an input voltage of 220 to 470 V and an efficiency of more than 97% weighs just 1.85 kg (dimensions: 207 x 151 x 80 mm). A longer version (weight between 2 and 2.5 kg and dimensions of 288 x 151 x 80 mm) with 9 kW and input voltages of 270 tp 500 volt has an efficiency of more than 98 %.
Outlook
The development of reliable heating solutions for modern passenger car cabins is challenging as electric vehicles provide only limited or no usable exhaust gas. Electric heaters are becoming more and more important considering the increasing electrification of the powertrain. BorgWarner’s range of innovative high-voltage auxiliary heater systems supports global OEMs by offering reliable solutions to provide comfortable cabin heating in all conditions. Furthermore, this sophisticated technology also secures higher battery-operated ranges for electric vehicles. Engineers currently work on driving the development even further designing 800 V solutions.
About the Author: Timo Stifel is Engineering Manager for High Voltage Coolant Heaters at BorgWarner Emissions, Thermal & Turbo Systems.
References:
Fig 1: BorgWarner’s HVCH heating technology relies on long-lasting Thick Film Heating Elements (TFE), with a substrate made of stainless steel carrying the dielectric layers and the heating resistors.
Fig 2a & 2b: BorgWarner’s HVCH is available in “single-plate” (left) and “dual-plate” variants.