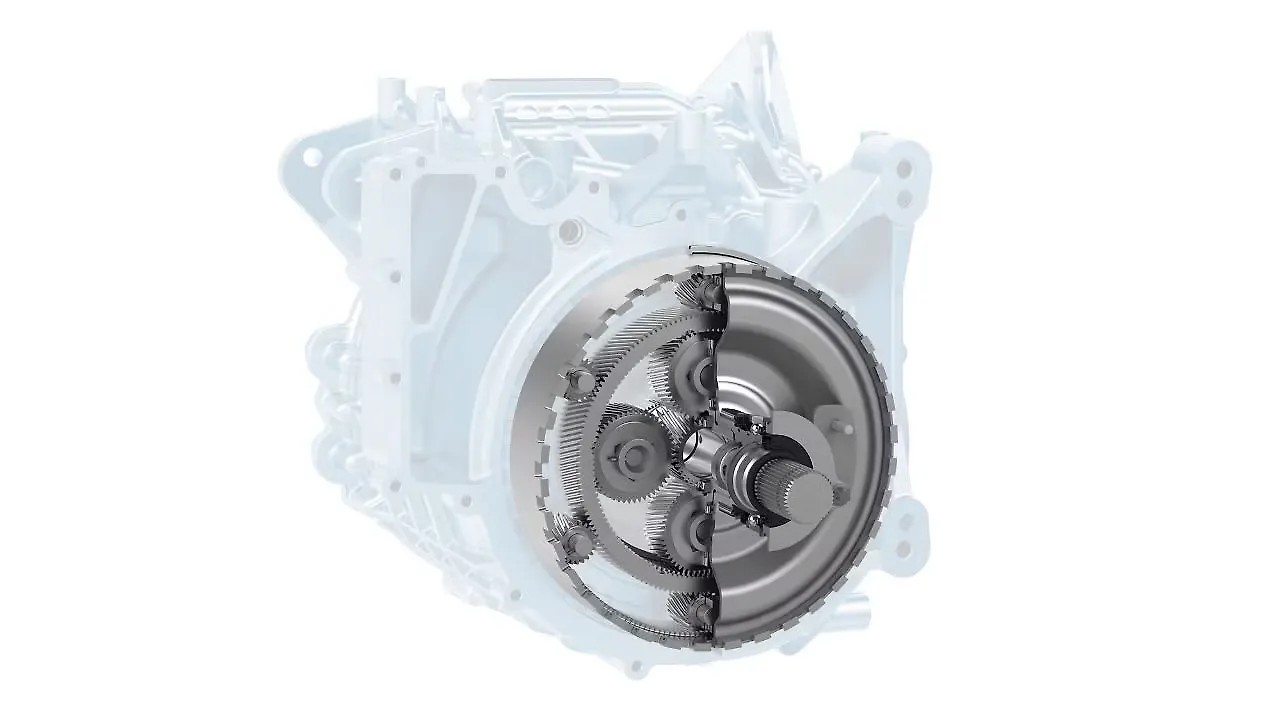
ZF, the global technology company, recently reached the milestone of producing two million electric motors. It supplies these to automakers for a host of applications right from hybrid and electric axle drives for electric passenger cars to electric central drives for commercial vehicles. The performance range varies from 50 kW to 550 kW, with torques from 75 Nm to 1,500 Nm.
ZF was the first volume production supplier in Europe in 2008 to bring an electric motor for premium mild-hybrid applications. Years ago, it had decided to deploy its own technology of concentrated windings, now used for electric motors in hybrid applications.
However, after 2015, when demand for pure electric mobility started to gradually rise, the company decided to focus on new technology such as hairpin winding followed by the more recent braided winding.
Next In Focus
ZF has also introduced planetary gears to enhance the efficiency of the e-motor. Robert Peter, Head of Engineering Product Line – Axles, ZF, said at a recent technical presentation that two or more speeds were the norms for applications in sports cars or LCVs. This helped mitigate the conflict between high-launch torque and the desired maximum speeds.
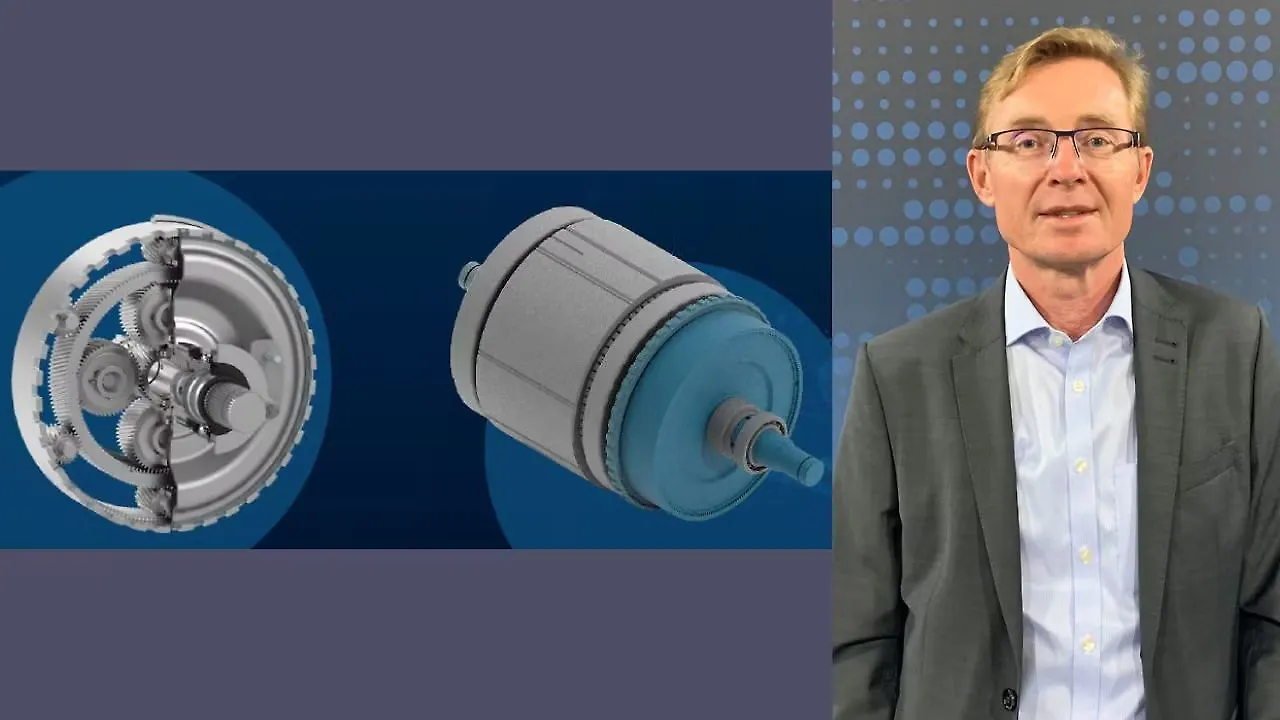
Apart from standalone reducers bolted together with the e-motor unit, the solutions offered today are integrated. Here, the reducer is encapsulated within the motor housing with common gears, bearings and cooling features.
As for the reducer’s geometric architecture, there are two options: offset design (where the e-motor has a parallel offset to the output axis) and coaxial design (where the e-motor axis and the output axis are identical). Vehicle packaging determines which of these two must be chosen.
More than a decade ago, continued Peter, ZF introduced a two-stage helical gear offset design along with a partner. Subsequently, various designs were developed with different axle ratios and launched in combination with its integrated 3-in-1 systems, otherwise called EVDs – electric vehicle drives.
Here, the bevel gears are deployed and laser welded to connect them with the differential case. These are derived from the company's conventional axle drive technologies.
Learnings From Automatic Transmission
Peter reiterated that the company’s traditional 9HP automatic transmission design helped it identify the best design solutions for managing different requirements, including NVH, weight etc. This transmission is deployed in a host of models such as Acura TLX/MDX, Chrysler 200, Chrysler Pacifica (2017– gas versions), Fiat Doblo, Fiat 500X, Honda Pilot, Honda Odyssey, Honda Passport, Honda Civic (2018-), Jeep Cherokee (KL), Jeep Renegade, Ram ProMaster City, Range Rover Evoque, Land Rover Discovery Sport and Jaguar E-Pace.
Market Evolution
Peter believes that market requirements are evolving with customers expecting more speed options from the electric motor. They also seek integration and design architectures, minimal noise, low weight etc. This is in addition to higher efficiency, high torque/power density, package flexibility and options for add-on features while also being cost-efficient.
Coaxial Reducer
With its new coaxial reduction gearbox, ZF transfers its know-how in planetary gearboxes to the next generation of electric drives. The two integrated planetary gears not only generate the desired axle ratio but also include the fully integrated differential function.
The uniqueness of the design is that the two stacked planetary gear sets are fully integrated into the differential function. As a result, these gears not only create or form the transmission ratio but also include a completely integrated differential function.
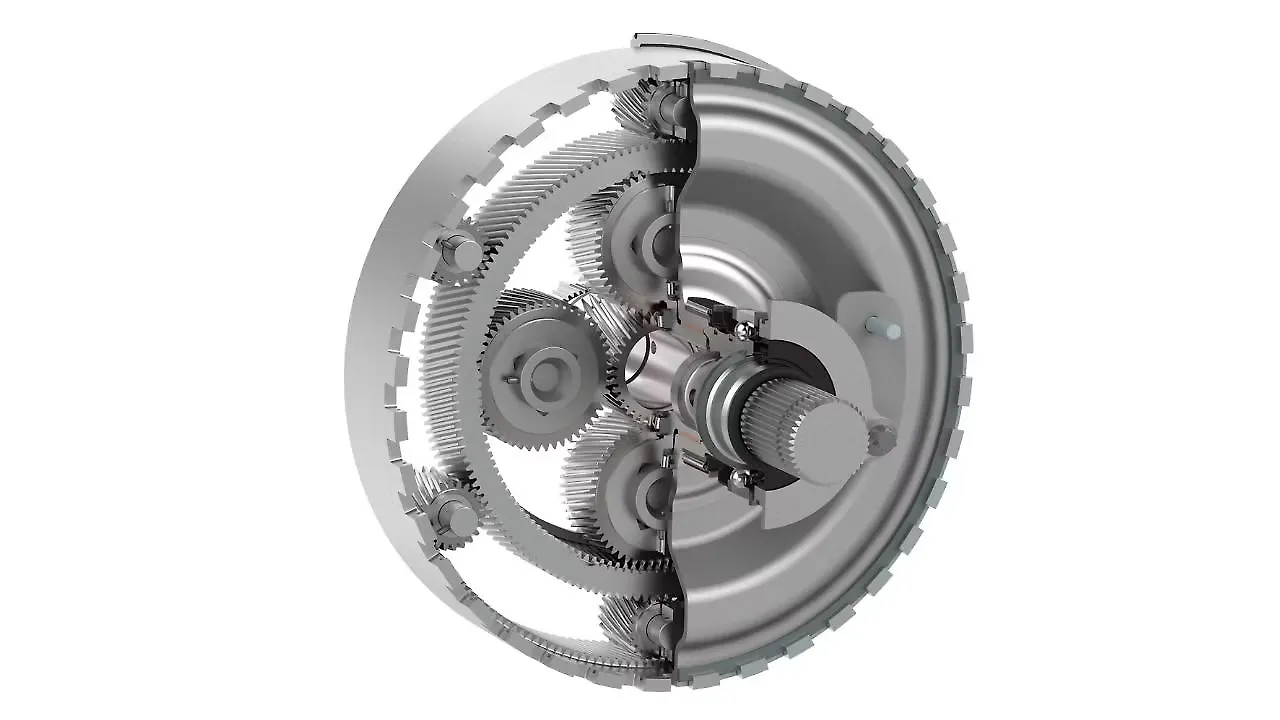
How Does It Work?
The e-motors shaft is connected to the inner Sun of the planetary gear set while the inner carrier is connected to one wheel and the outer ring is connected to the other wheel. This helps in splitting an equal amount of torque to both wheels.
Compared to common offset concepts, the new solution reduces weight and installation space requirements without compromising on efficiency, noise and vibration. In addition, it results in a compact solution. According to Peter, it looks like a disc with about 60mm thickness.
Benefits Over Off-set Design
The coaxial solution with integrated differential offers many benefits. It needs minimal installation space (25% less volume than the current offset designs). The power density is higher due to planetary gear sets while the system's overall weight is 10% less. Transmission loss is also 20% lower while the NVH performance is at par with offset designs.
“This technology creates an attractive solution; we are already discussing applications with some OEMs. We will see more in a couple of years when the solution goes into the market,” said Peter.
Volume Growth
Given the globally increasing volumes and the high demand for electric powertrains, ZF is confident that the next production milestone will be reached in less than two years. This is more so with the new developments in e-motor technology.
If these two million electric motors from ZF replace conventional combustion-engine passenger car drives, they can save about 45 million tonne of carbon dioxide over the average passenger car service life of 15 years.
If the same savings need to be achieved with renewable energy sources, it will call for a wind farm with 80 wind turbines, feeding the grid for about 25 years. These numbers are ample food for thought!
Also Read:
ZF Bets Big On India In Global Electric Transition
ZF’s New E-Motor Tech Helps OEMs Accrue Multiple Benefits
ZF Surpasses Two Million Production Mark For Electric Motors