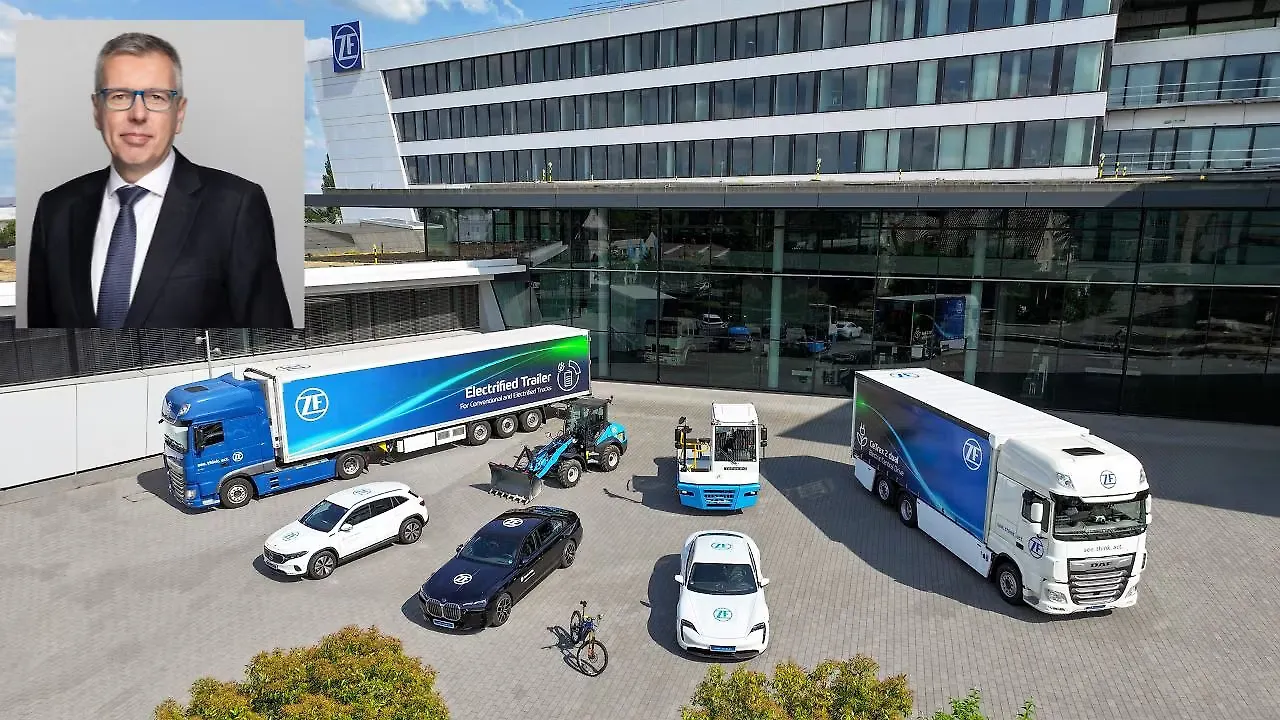
The basic definition for the term is ‘software that acts as an intermediary between two applications.’
More specifically, middleware is a prerequisite for intelligent mechanics which serves as an intermediary between vehicles’ operating systems and functions. It plays a crucial role in software-defined vehicles (SDVs).
From Holger Klein’s point of view, it made sense for his company to join forces with “someone who does the same things with complementary expertise” instead of wasting resources by going it alone. The CEO of ZF drove home this point at the recently held Technology Day at its headquarters at Friedrichshafen, Germany.
“We need to define standards for middleware and there is nothing specific in terms of customer experience. There is a lot of waste in our industry as everybody is doing their own middleware,” said Klein. Hence, he continued, ZF was inviting partners to be part of its joint venture with the Pune-based KPIT and harmonise middleware development.
“For us, it is very important to position this as something that we don’t lock with customers,” he added. The tie-up with KPIT, and allowing other partners to come onboard, was a pragmatic move as this was not a “monster profit engine” for the company but would play a specific role as a business enabler.
“Along with KPIT, we will develop an independent middleware solution for mobility applications and a joint venture called QORIX to offer mature, modular and integrated solutions,” said Klein. This route will offer state-of-the-art software architecture even for vehicles with lower economies of scale.
Future Of Mobility
He cautioned against playing down the importance of hardware — “we tend to always talk about software defined vehicles (SDVs) but if we don’t have hardware as a combination it becomes very difficult.”
As Klein explained, “We want to play a key role in the future of mobility with our technologies and make it safer and more sustainable. This is a factor for us in transforming technologies across all sectors right from cars, small and large trucks, buses and construction equipment to agriculture machines and wind turbines.”
The focus now is on e-mobility and chassis technologies which are the “key defining elements” of future mobility. ZF’s first generation 800V drive for passenger cars has been in production in China for the Lotus brand since the beginning of this year.
“Today, we are seeing the next generation of technology and have brought it into our EVbeat concept car. It is the heartbeat of innovation with an ultracompact, light and efficient 800V e-drive that will come a year later,” said Klein.
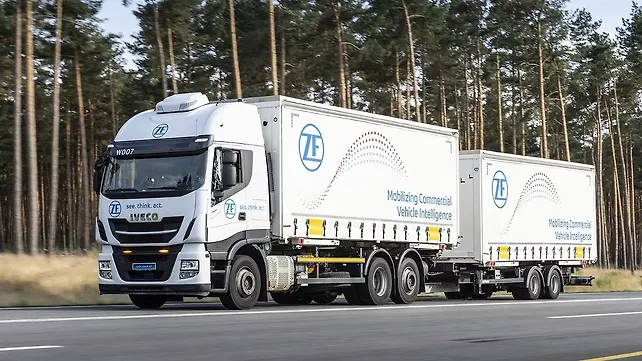
ZF has also developed software for connecting the powertrain to other systems and the cloud. A few months ago, the idea of the EVbeat concept vehicle was merely a vision but the prototype is now ready and has been tested too. EVbeat combines the state-of-the-art inverter with an electric powertrain into a holistic system.
New standards of compactness have led to the drive package being 30% lighter and, along with thermal management, spawned a torque density of 70NM per kilogram. According to Klein, this is a peak value for passenger cars now available on the market.
Mastering Transformation
It was made possible thanks to the new thermal management system and braided winding which enhanced power density of the powertrain. These technologies ensure that the EVbeat’s range increases significantly and ZF is now “mastering its transformation while laying the foundation for a successful future.”
As Klein said, “We are accelerating the development processes, adapting to new speeds, and shortening development and production cycles of the entire automotive industry. We are becoming even more agile and will develop new products in a few months.”
The silicon carbide inverter also helps EVbeat achieve greater range and shorter charging time. This will then result in more demand for the material even while silicon carbide is more expensive than silicon. The ZF CEO was confident that the company would find the right mix. It had, in this context, teamed up with a US-based chip manufacturer earlier this year to develop and optimise silicon carbide technology.
In the future, 200mm wafers will be produced in a joint venture factory in Germany and will be the world’s largest for production of chips used in power modules. “ZF will develop these in Nürburgring which offers proximity to the research centre,” he said.
Reducing Energy Losses
The company aims to reduce energy and conduction losses of chips by up to 40% of today’s standards. It is also looking at increasing power density by 30% and maximum operating temperature by 15%. The new chip design will enable thinner architecture and ZF will transfer these technologies to commercial vehicles and construction equipment for higher productivity.
Beyond this, production of the CeTrax 2 dual central drive, meant for light and heavy-duty trucks, has begun with Isuzu being the first customer. With a continuous power of 85kW, it offers improved performance for vehicles up to 7.5 tonne. As Klein said, the system is a convenient turnkey solution for existing vehicle platforms.
He also made a reference to the AxTrax 2 electric axle platform — which replaces engines, transmissions, and conventional axles — that will be used for light and medium commercial vehicles. The compact drives maximise battery space and deliver 210kW continuous power.
In construction equipment, ZF offers the eTRAC drive while its expertise with NVH in passenger cars comes in handy for wind turbines where noise is kept in check. This is particularly useful for turbines with a diameter of over 140 metres and “higher than the Eiffel Tower.”
Solutions For Electric
ZF’s revenue from combustion engines has fallen by over half to 27% in the last decade. The electrified powertrain division, which began in 2016, provides solutions for all vehicle segments. The e-powertrain and brake are key components for vehicles' longitudinal dynamics.
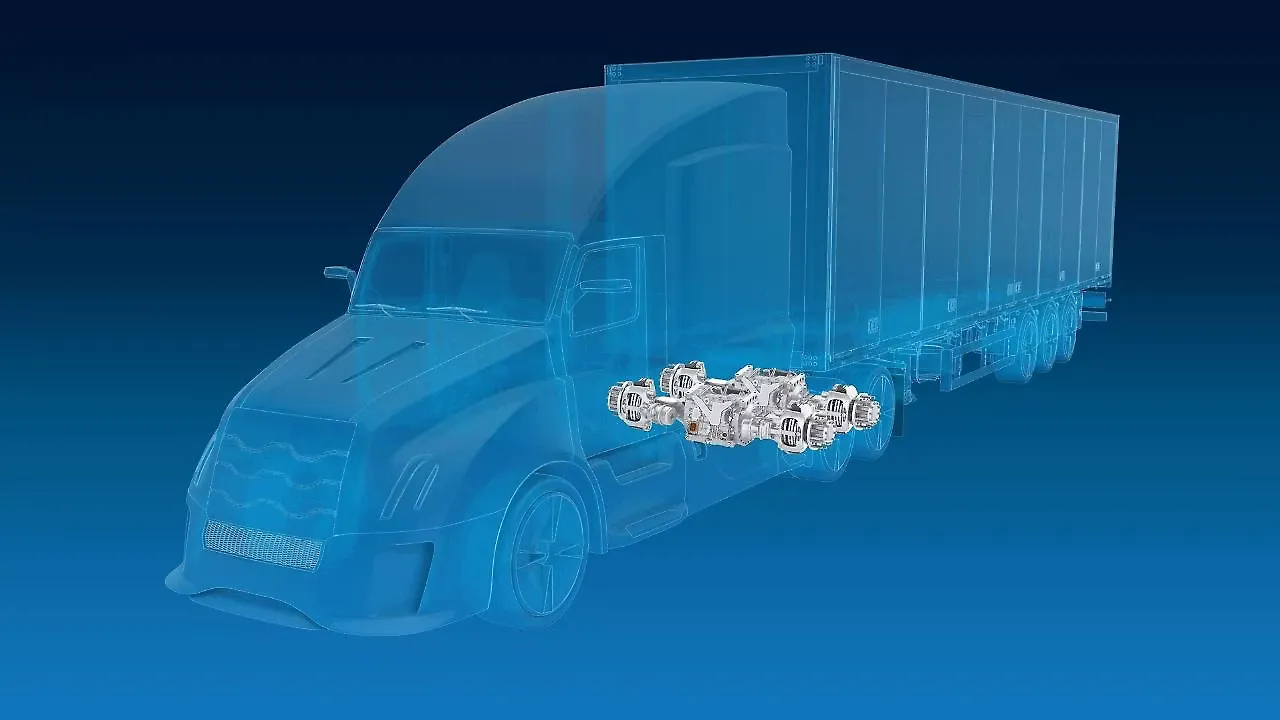
“With our chassis technologies, we can accelerate and slow down vehicles while steering and driving smoothly. We connect smart actuators through software controls to support the entire chassis,” explained Klein.
In EasyTurn, for instance, the steering angle of the front axle can be achieved up to 80 degrees. ZF’s rear axle solution helps vehicles park easily in congested cities besides reducing the turning circles from ten to seven metres.
Information on road conditions sent to the onboard computer helps the chassis adapt optimally. CubiX chassis motion control software, meanwhile, can control the electric powertrain and a leading Chinese electric car brand is already offering this technology.
Klein said this would be used by other automakers in Asia, Europe, and North America in the coming months. Systems such as brakes, steering and damping are electrically controlled without a mechanical connection. As for steer-by-wire, ZF has won orders from three major customers in North America, Europe, and China.
Growth Area
“Chassis technology is clearly a growth area for ZF. We will expand our innovation and technology leadership by establishing a new chassis solutions division,” said Klein. This will see the company bring together its passenger and active safety technology divisions. Scheduled for a launch next year, this new division bundles steering, braking, and damping technology.
The company replicated the same model for its commercial vehicle division when Wabco entered its fold in early 2022 and combined gearboxes and allied segments. “We believe these new entities will increase our customer focus and gain speed,” said Klein. This new division will encompass the needs of electronic steering systems for commercial vehicles and play a key role in their autonomous functions.
Also Read: