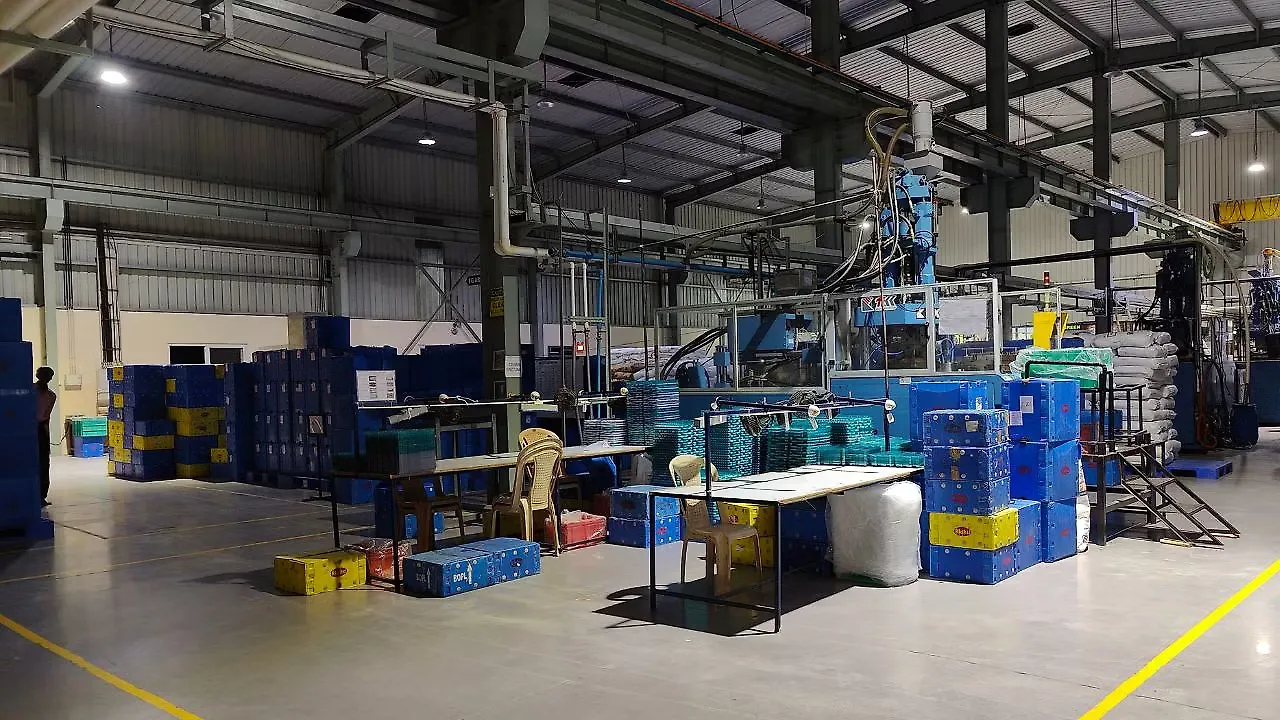
Coimbatore-based Suba Plastics is on an expansion spree. This will see it spread its wings beyond the automotive domain to new segments such as aviation, energy, medical applications and even toys.
At present, Suba makes engineering plastic parts under sub-categories including wiper and starter motor gears, power windows, engine pulleys, oil filters, chain tensioners and machined stems.
The company is a Tier-1 supplier to TVS Motor Company and Tier-2 to BorgWarner, Bosch, Comstar, Inteva, Lucas-TVS, Johnson Electric and others. It also exports to companies in the Americas, Asia and Europe.
Geetha Baskaran, Director, told Mobility Outlook that Suba is now developing engineering plastic parts by moulding PEEK (polyether ether ketone), a tough and expensive material which retails at about INR 12,000 per kg.
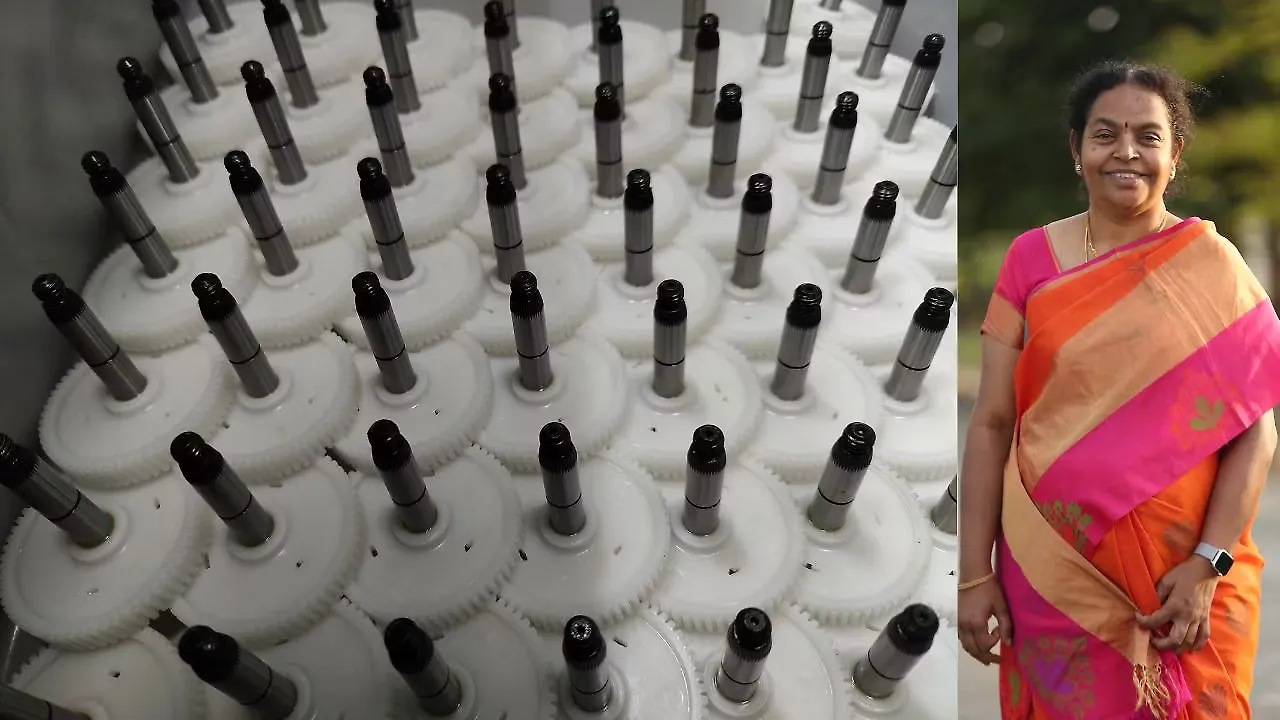
New Materials, New Opportunities
PEEK is used to make parts for demanding applications such as bearings, pistons, pumps, compressor plate valves and cable insulations. Since it is compatible with ultrahigh vacuum applications, Suba is exploring the idea of making parts used in medical applications.
In the long-term, continued Baskaran, the company will develop parts for the aviation sector which will need light materials with high-tensile properties. She said plans are also underway for foraying into electric mobility, industrial pumps, the energy sector and medical applications.
The company has been making sensor brackets for e2W makers but has gone one step further. It is now in the final stages of testing battery enclosers developed for a small electric commercial manufacturer. The toolroom set up in 1991 and the design centre established in 2005 come in handy for the project.
As these enclosers are large (close to a metre), Suba is expanding capacity with a 450-tonne moulding line. Currently, it has moulding lines up to 350 tonne which can make parts weighing around a kilogram and about 0.7 metres long.
The company is sitting on an order book of nearly 30,000 units for the battery enclosures. “The new machine is being commissioned specifically to support EV makers and those in the energy sector. If we are competitive, we can get more business. Our focus is on reducing the cost further,” said Baskaran.
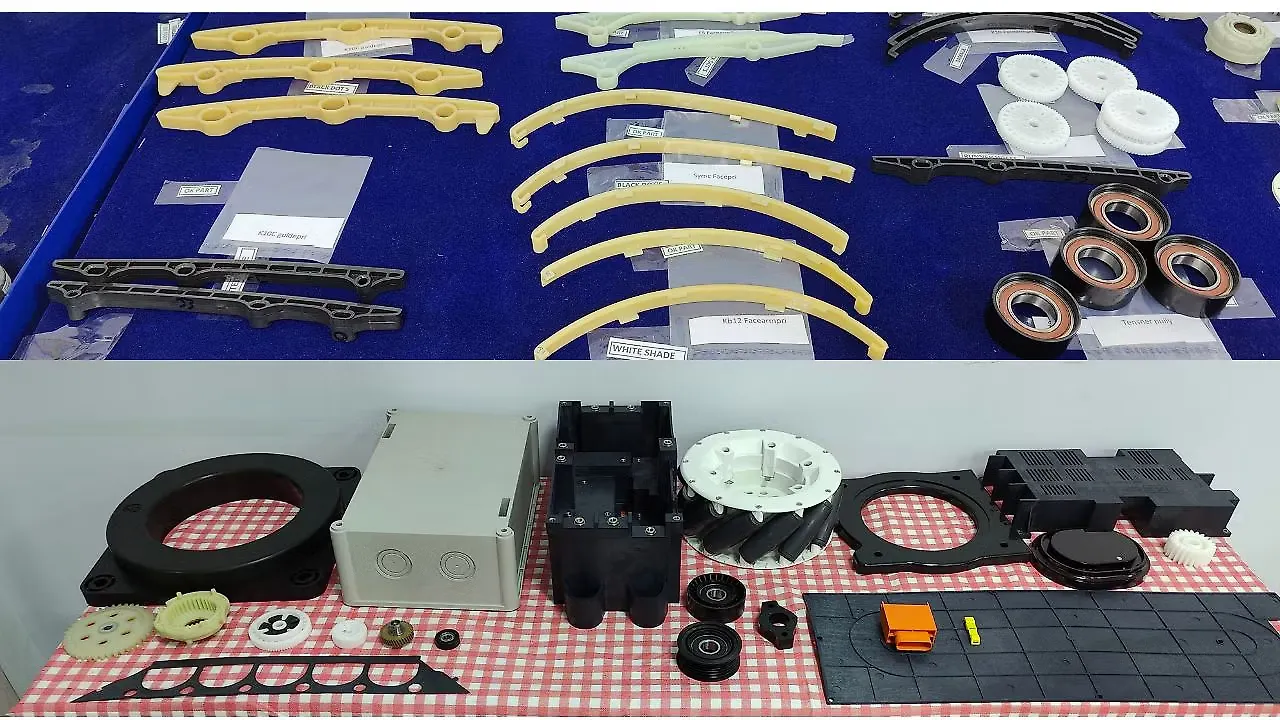
Import Substitute Solutions
As part of its effort to offer import substitute solutions, Suba is working on door latches in engineering plastics. It is also planning to make gears for motors in sunroofs and power-adjustable seats for passenger vehicles. Substituting plastic gears for machined gears is also on the cards.
“In addition to PEEK, we are conducting research on raw material that is abrasive-resistant, lightweight, free from UV-related issues and self-lubricating,” said Baskaran. This, according to her, will open up huge opportunities, especially in the automotive space.
The company, she added, was recently asked by a leading 2W maker to replace metal parts, including those made of aluminium, with plastics to enhance fuel efficiency. The OEM is looking at giving orders for about ten components in the short-term.
Suba is also looking at expanding its toolroom to support new businesses like toys where the potential is immense thanks to huge demand from local manufacturers to get import substitutes, said Baskaran.
New Plant
The mother plant established in Jothipuram (20 km from Coimbatore on the road to Ooty) nearly four decades ago is gasping for space. Keeping in mind these new growth areas, Suba is shifting production to a new facility adjacent to its second plant in Vellamadai, about 25 km from the city. Consequently, the Jothipuram facility will become an R&D hub.
The new plant will be almost equal to its second plant in size (30,000 sq ft) and will soon go green with the proposed solar energy project. This is a temperature-controlled plant where more than half the workforce comprises women.