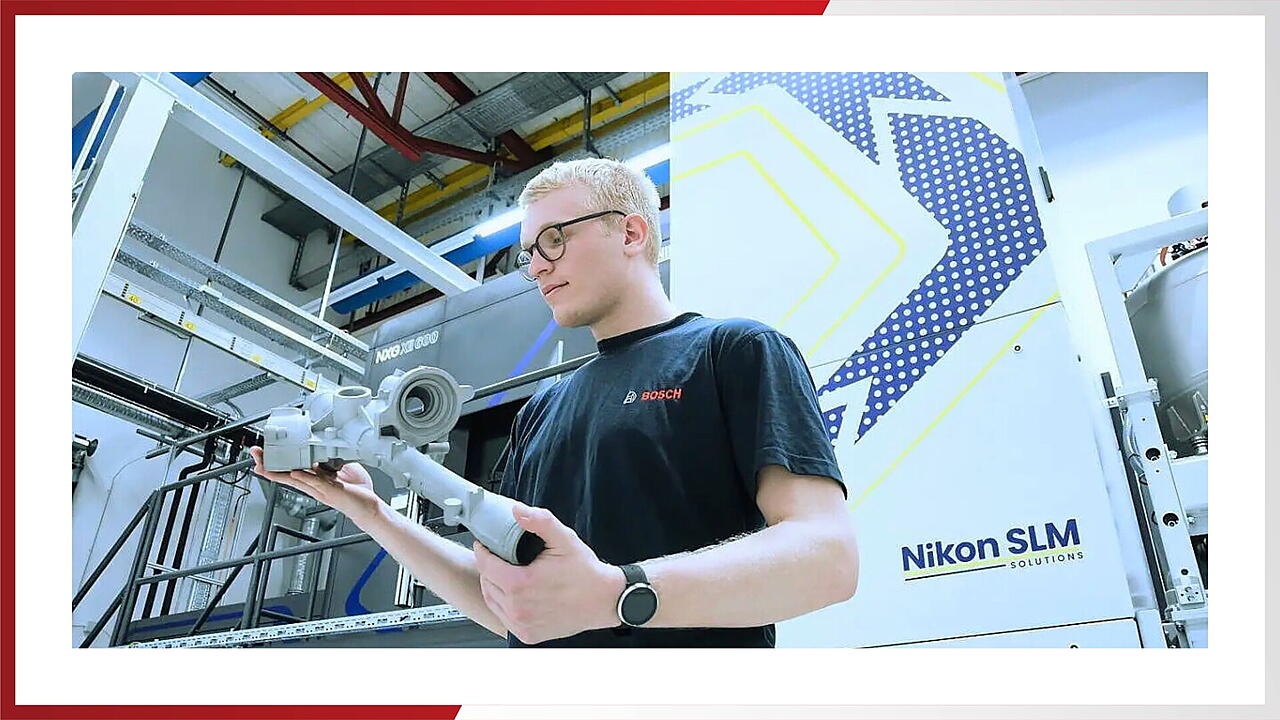
Speed, precision, flexibility, and sustainability—these are the pillars driving Bosch’s latest breakthrough in metal manufacturing. In a bold move that cements its status as an industry pioneer, Bosch has introduced a state-of-the-art metal 3D printing facility at its Nuremberg plant, becoming the first Tier-1 automotive supplier in Europe to operate a 3D printing centre of this scale. With an investment of nearly €6 million, Bosch is setting new standards in automotive production and industrial manufacturing.
The new facility is equipped with the Nikon SLM Solutions NXG XII 600 metal 3D printer, one of the most advanced high-performance additive manufacturing systems in the world. This cutting-edge technology is designed to accelerate development cycles by drastically reducing the time required to manufacture complex metal components—critical in industries where precision and efficiency are paramount.
Klaus Mäder, member of the Bosch Mobility sector board responsible for operations, said, “By introducing new technologies in our plants, we are securing considerable sales potential. Bosch remains committed to Germany as an industrial location and is investing large sums to strengthen our global competitiveness.”
The capabilities of Bosch’s 3D printing facility are game-changing:
- Up to five times faster than traditional 3D printing systems.
- Eliminates the need for complex tooling and moulds, reducing lead times.
- Minimises material waste, making the process highly sustainable.
- Allows for the production of previously impossible geometries, including interior curved channels and drilled corners.
“With this facility, we are setting the highest standards in metal 3D printing. In volume production, this opens up completely new possibilities for us,” said, Jörg Luntz, technical plant manager.
Breaking Barriers In Automotive Innovation
The applications for Bosch’s new metal 3D printing technology are vast and diverse. It will be used to manufacture components for hydrogen applications, motor housings for electric vehicles, e-axle components, and even engine blocks for high-performance racing vehicles.
One of the most striking examples of its disruptive potential is the production of engine blocks. Traditionally, designing and manufacturing an engine block involves lengthy and expensive tooling processes, with mould creation alone taking up to 18 months. With Bosch’s 3D printing technology, this process is reduced to just a few days, bypassing the need for moulds and slashing product development time from three years to mere months.
“We want to be faster than with traditional manufacturing processes and use this technology to get products to market more quickly. Even today, only a few companies can produce technology on an industrial scale the way Bosch does. Now, we’re taking metal 3D printing to the automotive level,” Luntz emphasised.
Scaling Up
At full operational capacity, Bosch’s 3D printing facility can produce up to 10,000 kilograms of metal components annually, with production speeds reaching 1,000 cubic centimetres per hour. This advancement is not just about faster prototyping—it is about bringing full-scale production into the realm of metal additive manufacturing.
Beyond the automotive industry, Bosch’s pioneering work in metal 3D printing is poised to benefit a range of sectors, including energy, aviation, and industrial manufacturing. With this initiative, Bosch is not just keeping pace with the future of production—it is defining it.
Also Read
Bosch Leads The Future Of Smart Manufacturing With Bold Software Push