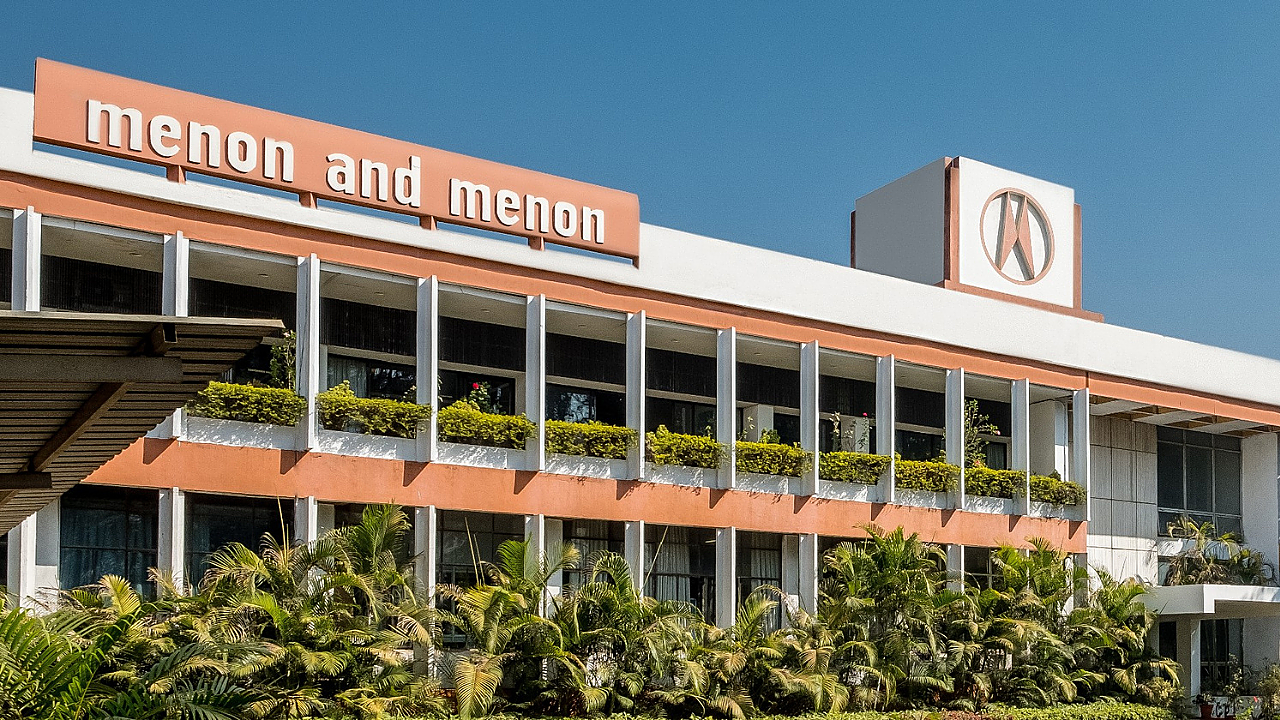
Kolhapur-based Menon & Menon Ltd (MML), a leading manufacturer of cylinder block castings for EURO-III to EURO-VI engine applications, as well as intricate thin-wall castings, is tackling market stagnation with a bold growth strategy.
Despite limited industry expansion over the past two to three years, MML is taking a proactive approach. 'The market has remained largely stagnant, but instead of waiting for a revival, we are doubling our capacity,' said the company’s Managing Director Vijay Menon, in an exclusive conversation with Mobility Outlook. 'By increasing production, we are not only securing a larger share of the domestic market but also positioning ourselves for export growth. This is our strategy for navigating these challenging times,' he said.
Growth-Driven Approach
As part of its aggressive growth strategy, MML has earmarked an investment of INR 110 crore to expand its production capabilities. Instead of relying on external loans, the company is reinvesting retained earnings, ensuring steady growth without the burden of debt repayment. 'Rather than taking on loans, we are building assets that enhance capacity while maintaining financial stability. We believe this is a prudent strategy for long-term sustainability,' said the company’s Managing Director.
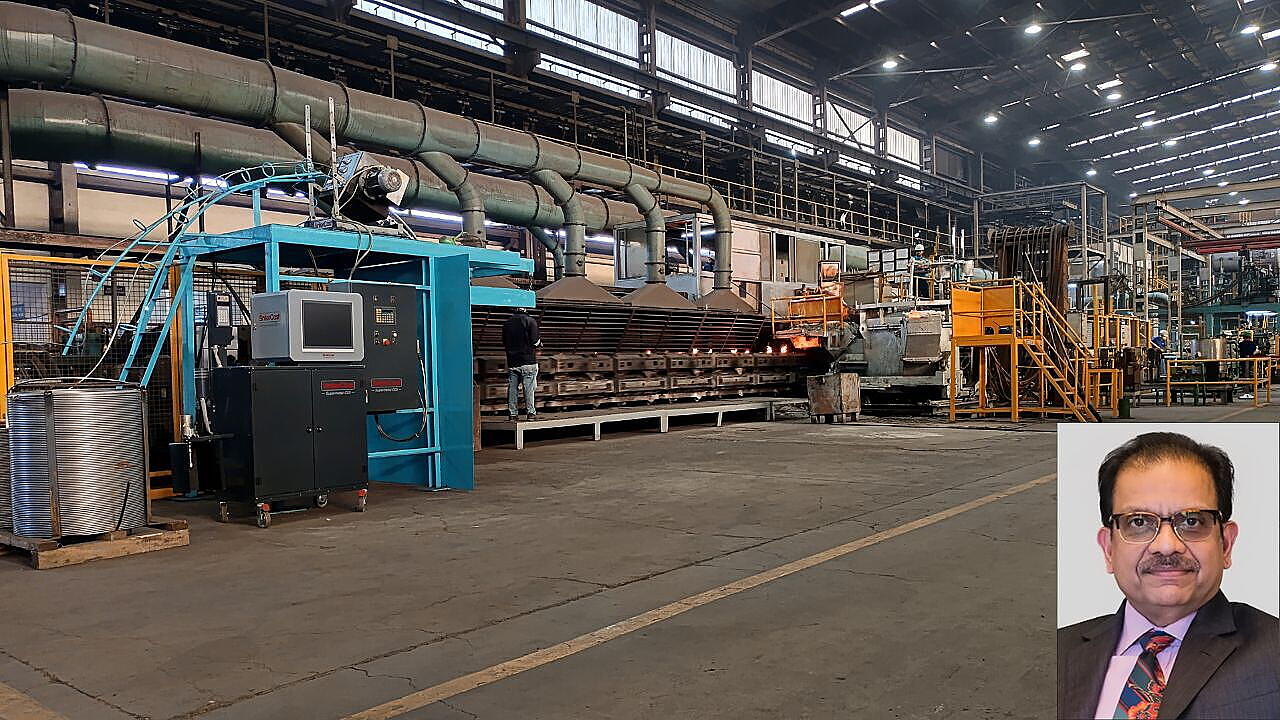
A key component of this expansion is doubling the capacity at the Kagal plant from 2,700 tonne to 5,400 tonne per month. Currently, MML operates at 2,500 tonne per month in Kolhapur, bringing its total capacity to approximately 8,000 tonne per month—equivalent to 100,000 tonne annually. This places the company among the leading global players in the foundry industry.
Looking ahead, MML has further plans for capacity expansion for FY2027, strategically aligning with its efforts to cater to international markets. The company is also investing in larger casting capabilities to meet the demands of global customers, particularly those requiring large-size castings for six-cylinder engines and above—a segment where MML currently faces constraints.
Additionally, MML is enhancing sustainability initiatives, having already commissioned solar panels at its facilities. However, due to spatial limitations, the company plans to adopt larger moulding boxes, enabling the production of bigger castings without major infrastructural changes.
Optimising Efficiency & Expanding Global Capabilities
MML is not just scaling up production but also enhancing efficiency and technological capabilities. The ongoing capacity expansion will double output while maintaining the same box size, allowing the company to manufacture both cylinder blocks and cylinder heads simultaneously.
A significant shift in production methodology will come from adopting cold box water jacket cores, which will replace traditional shell cores. This advancement will drastically reduce in-process inventories and cut cycle times significantly. In most foundries, 40-50% of space is occupied by core inventory, but MML’s approach will minimise stock holding to just two to three hours. By streamlining material flow and reducing footprint usage, the company will double productivity with only a marginal increase in workforce.
The next phase of expansion, planned for 2027, will further double capacity while introducing larger box sizes, allowing it to cater to bigger overseas customers. This will unlock new export opportunities, particularly for large-size castings used in six-cylinder engines and above. However, as the company acknowledges, the challenge remains that cylinder blocks and heads are dependent on fossil fuel-driven engines, requiring a balanced long-term strategy.
Scaling For The Future
MML is gearing up for its next major Greenfield expansion, set to commence in 2027. Unlike the current capacity-doubling initiative, which primarily involves line duplication and additional core routers, the 2027 expansion will be a completely new facility, designed for maximum efficiency and scalability.
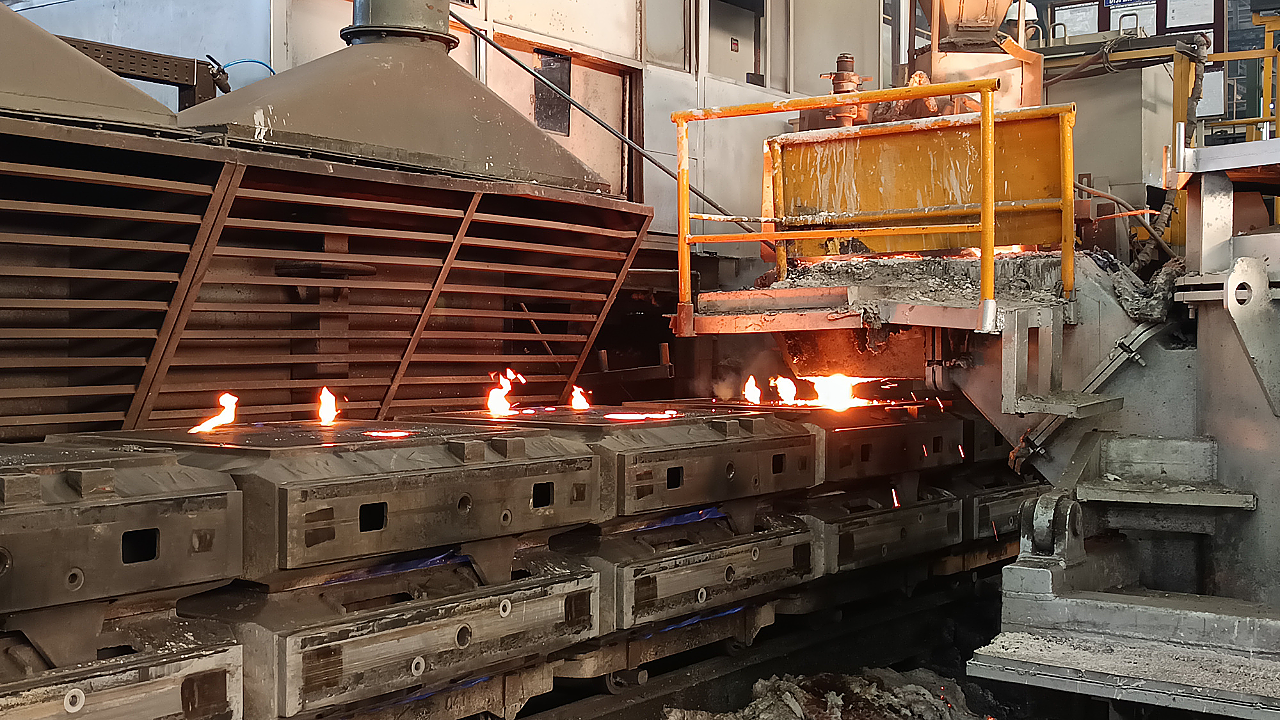
The project will be executed in two phases, with the first phase estimated at INR 250 crore, while the second phase will require slightly less investment. However, much of the groundwork has already been laid—the company owns a 15-acre plot designated for this expansion. Once fully operational, the new facility will add 12,000 tonne per month to MML’s production capacity, making it one of the most efficient foundries globally in terms of output per square foot.
Automation-Driven Operations
MML’s Kagal plant currently operates with just 38 people per shift, with only 30% of the workforce involved in direct production. The remaining personnel are dedicated to diagnostics, quality control, material verification, and maintenance—a model that reflects the company's push towards automation and efficiency.
'A modern foundry should focus on precision, quality, and diagnostics rather than just manufacturing,' he said. This philosophy will be embedded in the 2027 Greenfield expansion, ensuring that the plant is not only scalable but also highly efficient, data-driven, and globally competitive.
Transitioning From Mother Plant To Kagal For Long-Term Viability
MML’s mother plant in Kolhapur, located within city limits, faces operational challenges due to urban constraints such as noise, pollution, and regulatory restrictions. Additionally, the plant is more manual-intensive, contributing to higher employment costs of 12-13%. In contrast, the Kagal facility operates with only 4% employment costs, which will drop further to 3% post-expansion, delivering a 9-10% cost advantage.
While setting up operations in Kagal required higher initial investment, the plant is now virtually debt-free, with low depreciation and finance costs. This makes shifting certain functions from the Kolhapur plant to Kagal a strategic necessity. MML plans to relocate portions of its mother plant, including its machine shop, to Kagal, ensuring cost efficiency and long-term sustainability, Vijay Menon explained.
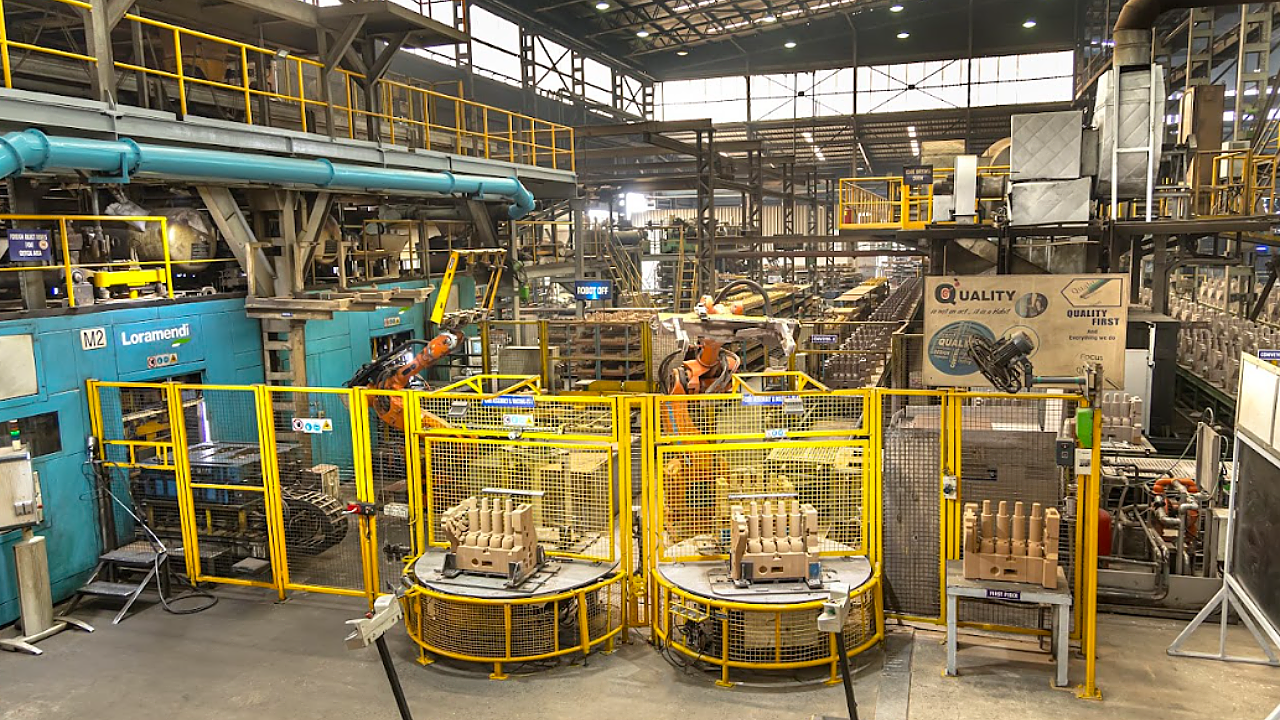
As part of its future vision, the company is also exploring alternative uses for the Kolhapur plant location, considering its limitations in an urban setting. By strategically managing its capacity expansion, production efficiency, and operational shifts, MML is positioning itself for global competitiveness while ensuring financial and environmental sustainability.
Harnessing Digitalisation & AI
MML is embracing digitalisation and AI-driven predictive analytics to enhance efficiency and cost management, particularly at its Kagal plant, where networking and automation capabilities are being integrated. In contrast, its mother plant still relies on manual operations, limiting the scope for advanced digital applications.
A key focus is on predictive AI for supply chain optimisation. In the foundry business, 55% of total costs are attributed to raw materials. Even a 10% inefficiency in procurement can negate gains from improved manufacturing efficiency. 'It's not just about producing efficiently; it's about buying efficiently. When to buy, when to stop, whether to import or source locally—all these decisions impact profitability,' he pointed out.
AI-Driven Decision Making In Procurement
Market volatility, influenced by global events such as natural disasters, geopolitical conflicts, and freight fluctuations, creates challenges in material procurement. AI models could provide predictive insights, analysing variables such as freight rates, supply chain disruptions, and commodity pricing trends.
For example, if a flood in Brazil affects material availability, an AI-powered system could identify early indicators and suggest proactive stock adjustments. Similarly, tracking shipping costs, war zones, or trade policies could help forecast material price fluctuations three to four months in advance. Even a 1% improvement in material cost management could significantly boost profitability—in an industry operating at 5-6% margins, this efficiency could translate into a 16% increase in net profit, he explained.
Although MML is still in the early stages of exploring AI-driven procurement strategies, it recognises the potential of digital tools to enhance decision-making and improve the bottom line.
Achieving Global Productivity Standards At Indian Costs
On the production front, MML is already outperforming the Indian industry average in productivity per worker. The company currently operates at 9 tonne per worker per month, compared to the Indian average of just 2 tonne. The global benchmark is 10 tonne, and with the full-scale expansion, MML expects to increase this to 10-11 tonne per worker, achieving global efficiency levels at significantly lower costs.
With its focus on smart manufacturing, AI-driven procurement, and productivity enhancement, MML is not only scaling up its production capacity but also ensuring that every aspect of its operations is optimised for efficiency, profitability, and global competitiveness.
Also Read:
Menon & Menon Strategises For Early Leadership In Emerging Technologies