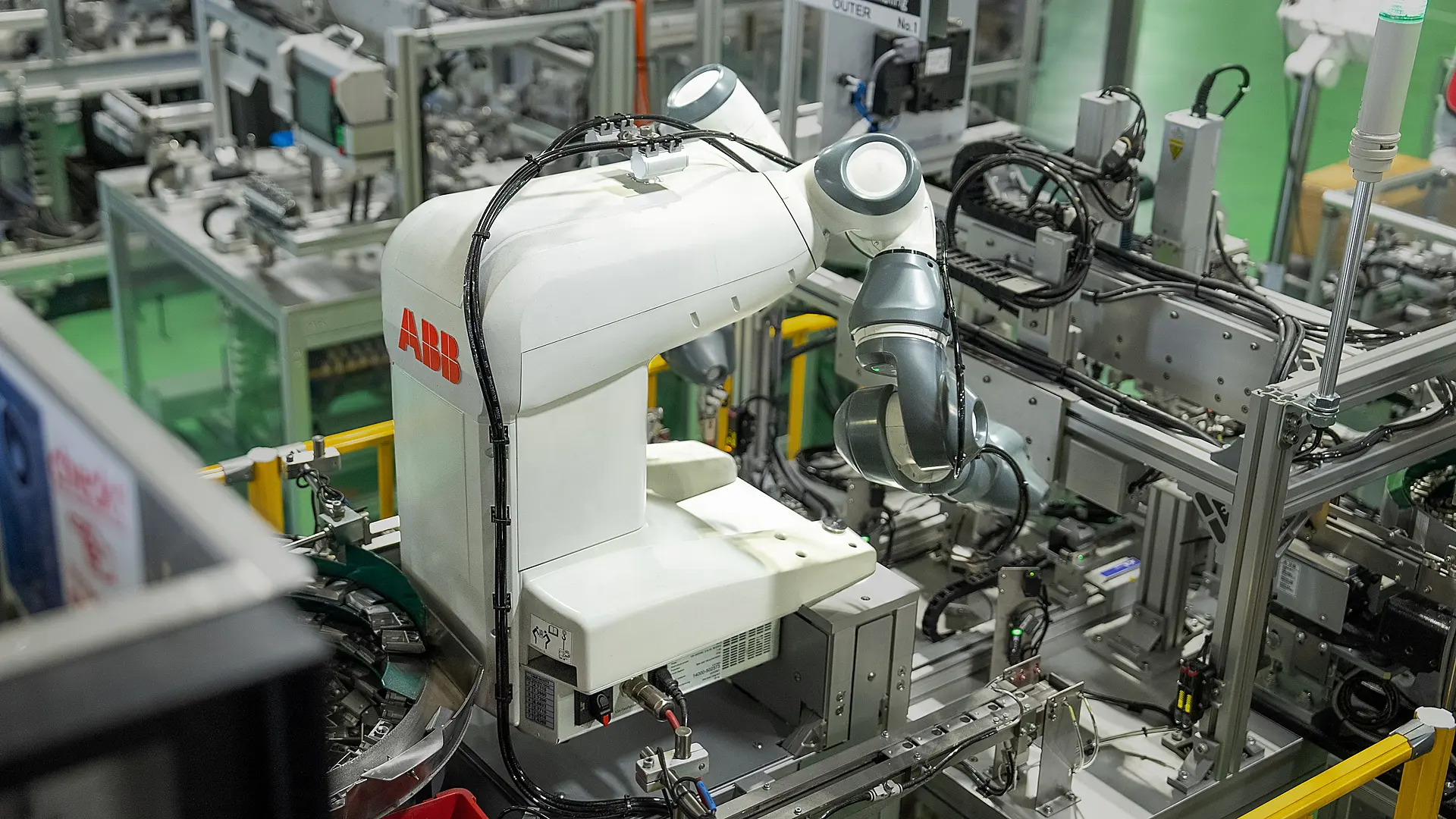
SUS Corporation, a leading supplier of aluminium frames and die-cast components for the automotive and other manufacturing sectors, has decided to go in for domestic production at Shizuoka in Japan.
This is expected to help SUS Corporation manage its lead times and introduce greater flexibility.
The move to opt for domestic production comes in the wake of significant disruption to global supply chains in recent years.
A combination of factors – ranging from manual and repetitive nature of the production process to mounting labour shortages, has made it difficult for the company to recruit and retain sufficient workers to achieve the required production volumes. The company has gotten over this issue by deploying a series of YuMi dual-armed cobots. The company was able to reduce assembly time, increase productivity by 20% and introduce the much-needed flexibility.
ABB Survey
ABB recently conducted a survey about labour and skill.
The survey threw up interesting findings. About 56% talked about ‘specific skills shortages’. But the report revealed other challenging aspects. About 48% of the respondents talked of the ‘new skill sets required’. Nearly 38% spoke of the ‘general labour shortages’. About 35% of the respondents pointed to ‘lack of education, training and qualifications’. While 33% spoke of ‘competition from other industries’, 29% respondents stressed on ‘uncompetitive pay and conditions.’
The decision by SUS Corporation to deploy ABB YuMi dual-armed collaborative robots must be read in the context of the findings of the ABB survey. The cobots are said to enable the re-shoring of production and help in fixing the challenges presented by workforce shortages.
Co-existence
The cobots' seven axes of movement per arm were able to replicate the complex twisting actions needed during the assembly process.
In 2015 ABB introduced the YuMi collaborative robot. YuMi enables people and robots to safely and productively work side-by-side without barriers.
Collaborative robots are adept at adding flexibility to assembly processes that need to make small lots of highly individualized products in short cycles. By combining people’s unique ability to adapt to change with robot’s tireless endurance for precise and repetitive tasks, it is possible to automate the assembly of many types of products on the same line.
According to Joerg Reger, Managing Director of ABB Robotics Automotive Business Line, re-shoring is increasingly viewed as a way to address the challenges of disruptive supply chains and uncertainty. But, it can introduce complexities of its own. However, according to him a range of flexible automation solutions can help resolve these challenges.
With the deployment of YuMi robots, SUS is now hoping to achieve payback on its investment within two years.
The automated solution was developed by SUS using ABB’s RobotStudio simulation software to design and optimize the operation in a virtual space, ahead of deployment in the real world. The simulation verified that YuMi’s seven-axes of movement per arm were able to replicate the complex twisting actions needed during the assembly process.
RobotStudio’s accurate calculations for achievable production volumes also made it easy for SUS to make informed decisions about its investment. The company is now exploring the possibility of adding further cells for other products and automating other processes.
Advantage new system
Akihiro Taki, Team Manager, Die-casting Team, at SUS Corporation’s Shizuoka site, said that the robots had taken on monotonous, repetitive jobs, enabling workers to be reassigned to more rewarding tasks such as operation management.
The new system has also made it possible to operate at night with fewer workers, with the number of dedicated assembly machines in operation reduced from 11 to five.
ABB is adding a new member to the YuMi family, 7 axis YuMi, the smallest and most agile collaborative robot yet, making it easier than ever to put into production. The new 7 axis also opens up a world of flexible possibilities – for example a single-arm and a dual-arm YuMi could be combined to add a parts feed or inspection station to an assembly cell. Additionally, customers might want to have three or five YuMi arms in an application to improve the cycle time.
The entire YuMi family is designed to be easy to set up and use, thanks to its intuitive lead through programming. That means that even people without specialized training or prior experience can successfully use robots.
Also Read