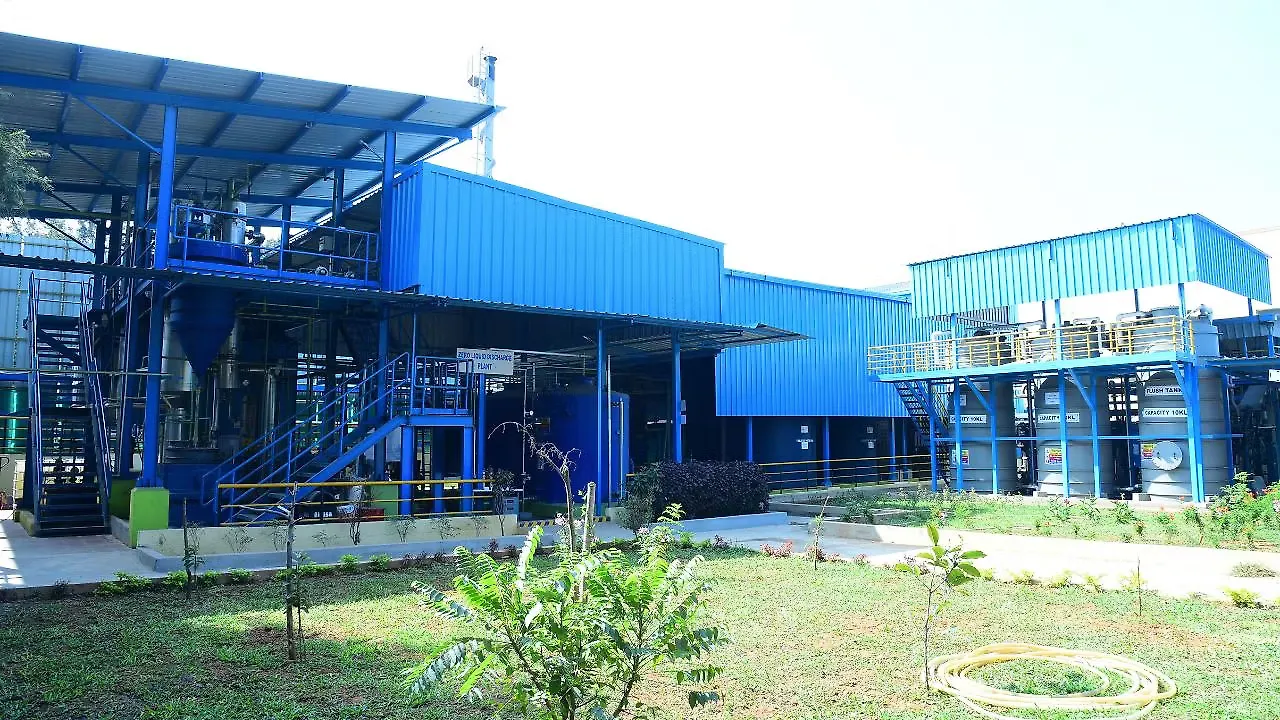
The numbers are mind-boggling.
On an average nearly 400 kilolitres of freshwater are needed to produce a car right from the raw material stage to the time it rolls out from the assembly line.
Now that would be seen as a tremendous waste especially in these times of global warming where water scarcity is a huge threat to reckon with. The good news is that there are technologies that help recover about 98% of the water.
It is here that Veolia of France has been working on solutions to manage water, waste and energy which have helped automakers recycle 97% of an end-of-life vehicle and, in the process, recover metal, glass, plastics etc.
It is this mastery of the water cycle that Veolia will capitalise on to position itself as a key stakeholder in the automotive sector. With its water/wastewater treatment systems, it assures (water) reduction and increased operational efficiency which goes a long way in reducing costs and protecting the environment.
Gopal Madabhushi, Senior Vice President, Business Leader – South Asia, Veolia Technologies & Solutions, told Mobility Outlookthat water is a key resource that is fast depleting. This becomes even more significant in any manufacturing industry that uses large quantities.
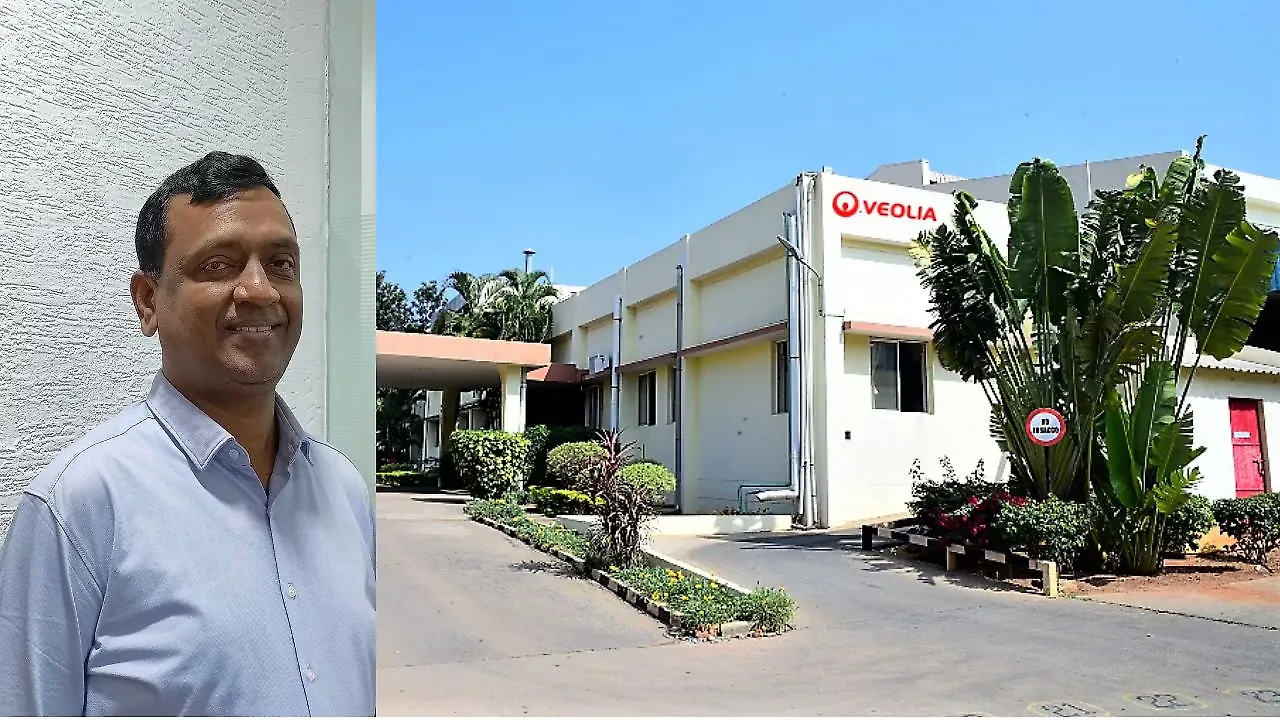
Adding Value
Right from process design and on-site trials to supplying high-quality water to offices while optimising effluent treatment plants, Veolia strives to add value at any stage of the water cycle. Its basket of solutions helps provide quality water and treat pollutants. Some of its major customers include Stellantis (where it manages six main sites and 19 others), Volvo, and Renault.
Veolia provides innovative solutions and a portfolio of technologies while helping these companies comply with stringent environmental standards. Some of these include water softening, microfiltration, reverse osmosis, and electro-deionisation for purity.
With electrification now the name of the game, innovative wastewater management is top priority with a focus on recycling and zero liquid discharge.
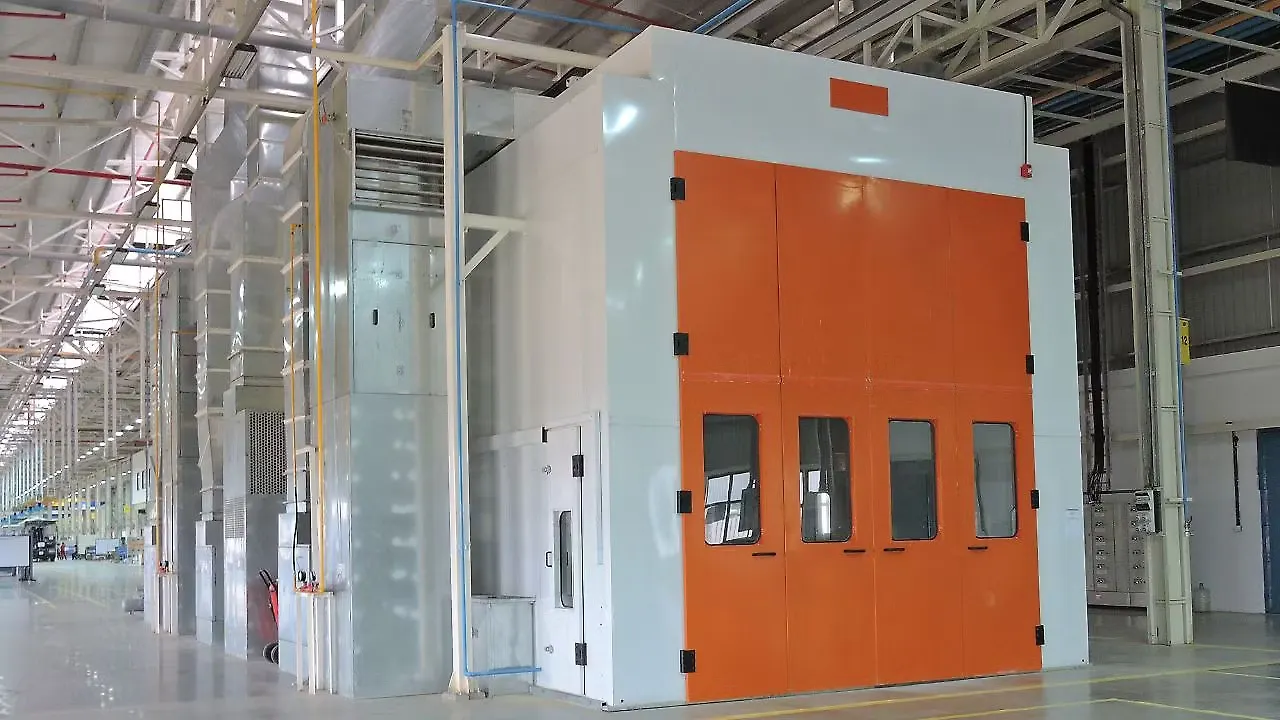
Water is largely used to rinse and clean treated surfaces during the process of manufacturing vehicles. Huge quantities are needed to paint car bodies and it is pertinent to note that suppliers of child parts, systems and modules need more water than their OEM customers. Semiconductor manufacturing needs ultra-pure water to rinse and clean silicon wafers as also in removing minute particles.
From Veolia’s point of view, the common processes for treating wastewater in the automotive industry include vacuum evaporation, chemical-physical wastewater treatment, membrane and mechanical treatment. The choice of process is based on the amount of wastewater and where it will be deployed in meeting zero liquid discharge (ZLD) commitments.
For instance, a large amount of wastewater is generated when raw materials are extracted for the batteries. The presence of rare materials and chemicals poses a huge challenge in recycling water especially when the objective is ZLD.
Extending Support
Veolia ensures support services at automakers’ production sites by way of reducing energy and water consumption, recovering waste, and creating local circular economy loops. A case in point is the company’s installation of a waste heat recovery system for Volkswagen’s Poznan plant in Poland which has helped reduce annual CO2 emissions by 1,000 tonne and water consumption by 17 million litres.
Back home, Veolia India Technologies & Solutions has helped out when the membrane bioreactor (MBR) technology is deployed. A leading transmission manufacturer adopted this and helped the automaker concerned to recover over three million litres of water everyday.
Likewise, a two-wheeler major adopted MBR and EDR (electrodialysis reversal desalination) technology to enhance recycling water capacity without increasing the size of the ZLD unit. This increased recovery of recycled water significantly. Yet another two-wheeler maker adopted MBR to treat wastewater and it warrants mention that automakers have also adopted UF/RO at various stages.
According to Madabhushi, companies seeking water management solutions worry about initial investments or the lifecycle cost. While both are doubtless important, users need to focus more on operational expenses as water treatment plants run for over 25 years.
“Our technologies and solutions focus on reducing the burden on operational expenditure since there are a host of elements including energy cost, parts replacements and maintenance,” he explained.
India Drive At Hoskote
The company’s plant in Hoskote near Bengaluru is seen as a model plant globally in terms of eco-friendly production and sustainable operations through digital water management system and automation. The team here treats all wastewater generated without leaving out a single drop.
The facility has ZLD for chemical wastewater treatment, ETP for all other wastewater and a RO plant to process raw water in process and product needs.
The team at Hoskote has also set up rainwater harvesting to conserve water and reduce the stress on ground reserves. This has helped cater to over 40% of annual water requirements.
Veolia’s global team has used the Hoskote site as the reference point for digitalisation of the water management system. This has helped visualise overall water balance to measure actual consumption versus requirement as well as losses in the system.
The idea is to take necessary action and improve efficiency and effectiveness. Once this is done, the plan will be implemented across other facilities and similar water intensive industries.
Walking The Talk
Over the last two years, Hoskote collected over 7.2 million litres of rainwater with a TDS (total dissolved solids) value of 60 to 75. Water procured from outside had 800 to 1,000 TDS. The plant managed over 40% of water requirements for production and saved significant amount of money beyond 20% of electricity, which otherwise would have been used to filter the outsourced water.
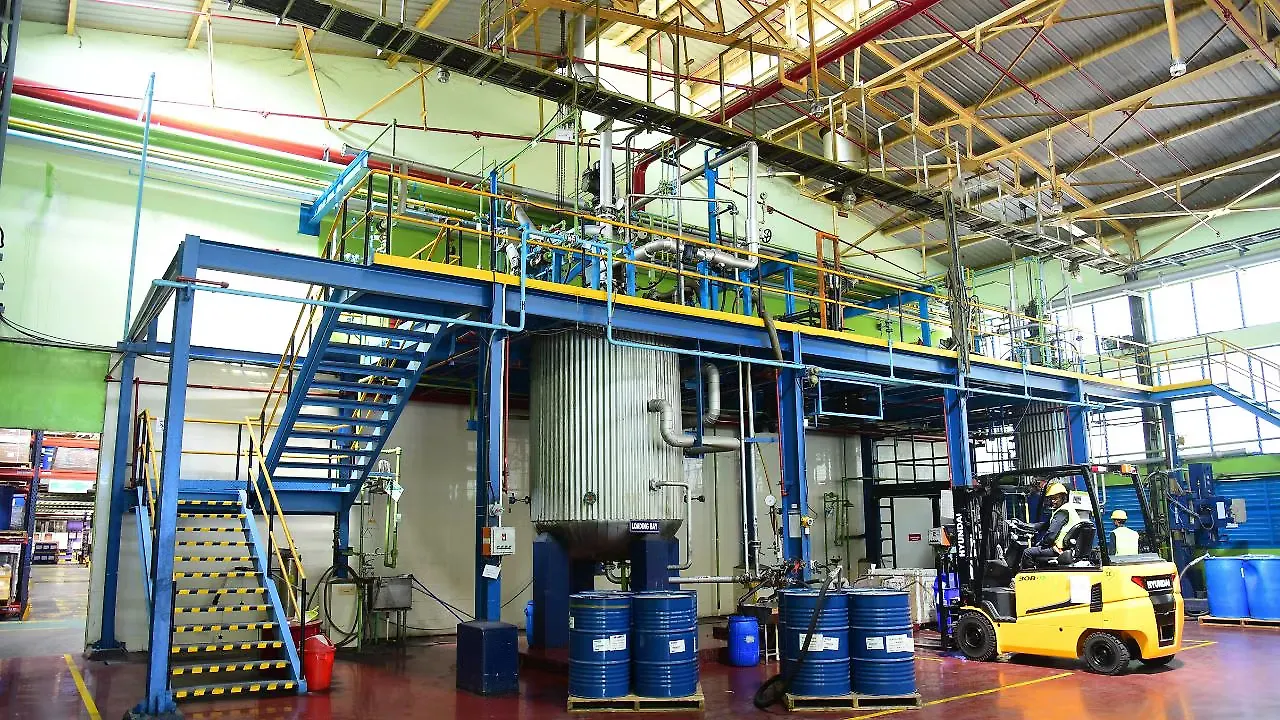
Transportation of chemicals internally used to be with diesel operated forklifts which have now been replaced with battery operated instead, hence saving tremendous amount of fuel required for this operation and reducing CO2 emissions.
While chemical factories are not permitted to place solar panels on sheet metal rooftops for reasons of safety, the Veolia unit used them in every possible space other than the sheds. Today, nearly 20% of the energy consumption is managed through this route.
ZLD at Hoskote has helped recover 98% of the effluent water despite massive contamination with different chemicals. With continuous improvement projects, the cost per litre for filtration has fallen drastically.
Plant Processes
This has happened thanks to efficiency improvements and use of CNG instead of diesel which also kept CO2 emissions in check. An effluent treatment plant here also treats sewage.
The Hoskote facility has two product lines: filters and membranes, and chemical monitoring solutions. It is one among the five plants to make the former with the other filter and membrane units in Germany, Hungary, China, and the US.
Various filters and membranes, chemicals are made in multiple combinations depending on customer’s application based outcomes. All the products are inspected and tested for performance before being shipped. Customers use the elements connected in series for their desired levels of filtration. A renowned steelmaker uses 400 units of 8-inch elements.
Also Read:
Renault, Nissan Conserve 50,000 L Of Water Daily At Its Oragadam Plant