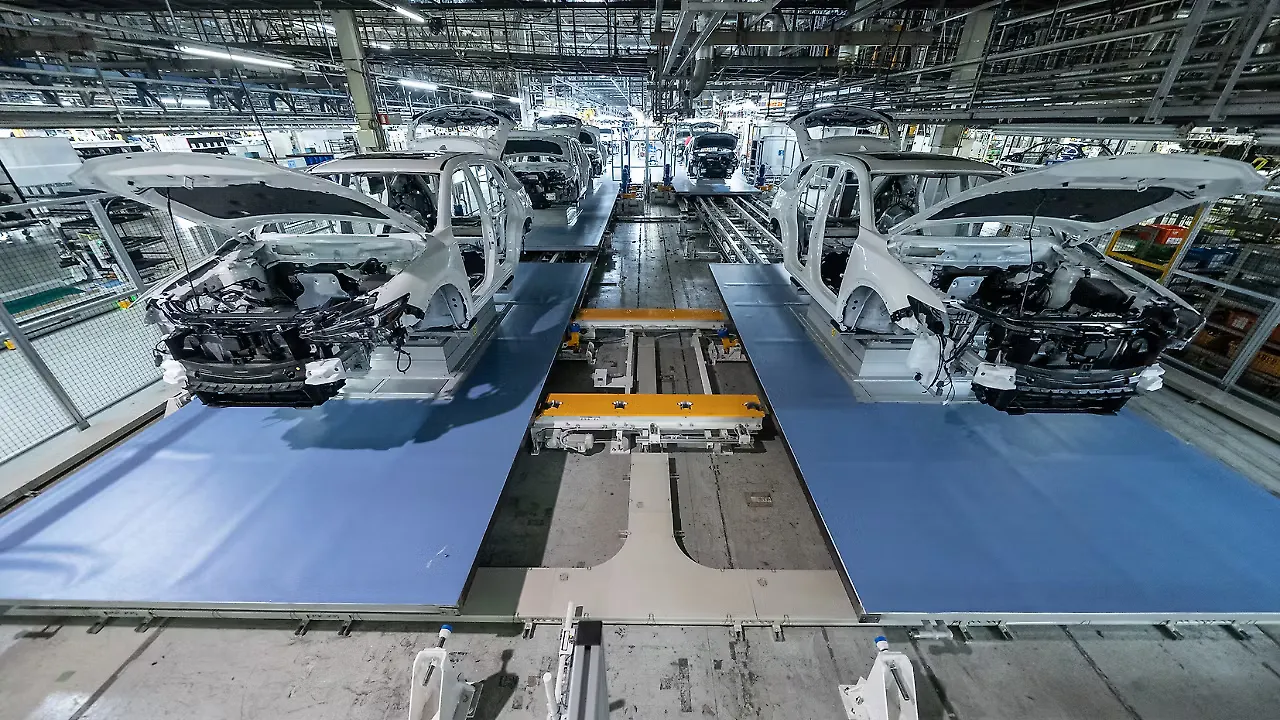
Aiming to offer customers a diverse choice of SUVs that can provide end-users with the driving pleasure and the latest environmental performance to meet demands in the continuously growing global SUV segment, Mazda Motor Corporation unveiled its strategy recently. Accordingly, the Japanese OEM will expand its SUV lineup starting from 2022. The new models will include the Mazda CX-50 to be produced in its new US plant, as well as models in its Large Product group that includes CX-60, CX-70, CX-80 and CX-90, which are slated for introduction 2022 and 2023.
As part of its strategy, the vehicle maker also unveiled the newly remodelled H2 production line at the Hofu plant in southwestern Japan. The H2 production line, which is currently manufacturing the Mazda6 (known as the Mazda Atenza in Japan and China) and Mazda CX-5, has been upgraded to build the Large Product group models, offering a variety of choices of electrified powertrains. In addition, the enhanced production system allows the company to adjust its production more easily to new models or shifting demands, making it the latest example of Mazda’s unique Monotsukuri innovation approach.
Monozukuri, generally inferred as craftmanship, emphasises that manufacturing should be in harmony with nature while offering value to society. It calls for maintaining a balance amongst production, resources and society. As a result of the remodelling, vehicles with different platforms (large or small), powertrains (internal combustion or electric) and engine layouts (vertical or transverse) can be produced on the same line in the future if needed. This mixed production approach is an essential step towards fulfilling the brand’s plans in the future, under its multi-solution strategy.
Traverse Dolly Line
The heart of the remodelled assembly is a traverse dolly line. The system relies on 'rootless' equipment, which disallows the plant to rely on fixed conveyor belts or hangers. Instead, the vehicles are moved on palette platforms that are level with the ground and skate on dolly rollers. These can be arranged more flexibly than a fixed system – if demand increases, production capacity can easily be extended by adding more sections to the production line.
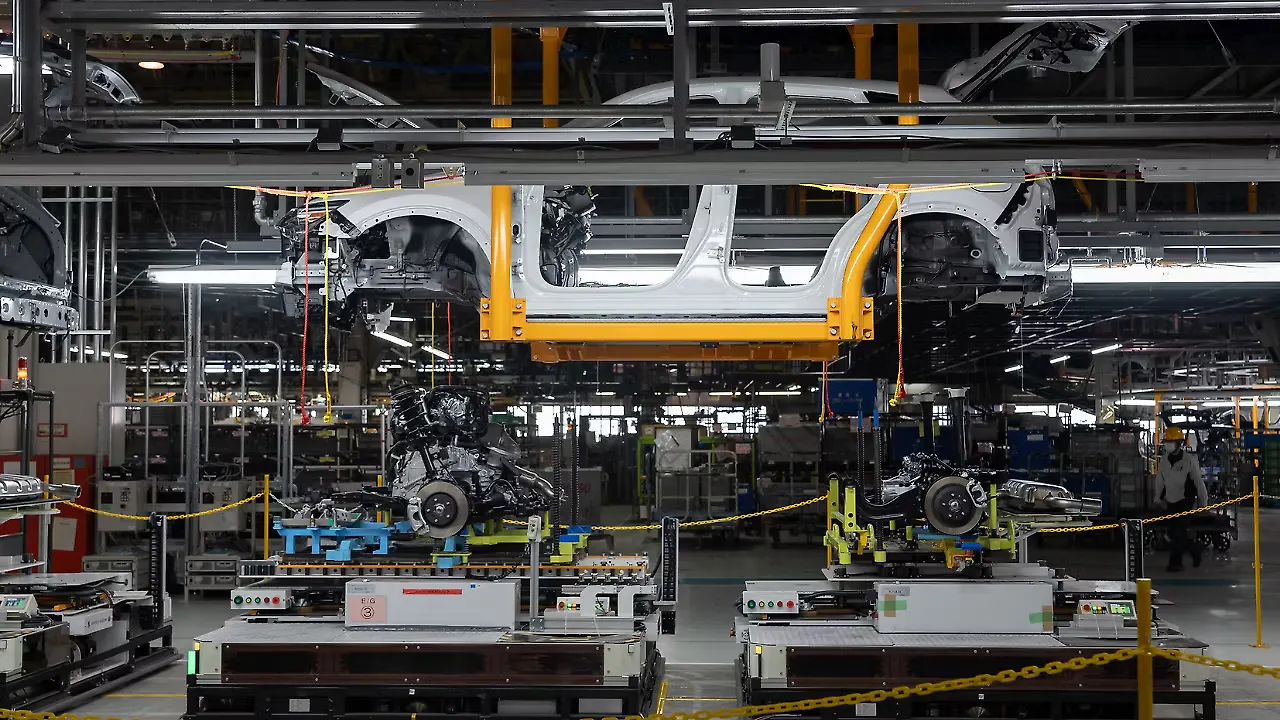
The dolly system also allows workers to move around the platforms freely and perform whichever tasks are required for the vehicle type in front of them. Two automated guided vehicles (AGVs) that align themselves with the length of the vehicle being built at the current moment deliver the engine assembled with front suspension and rear suspension, respectively, or the battery in the case of an electrified vehicle.
At present, over half of the facility is now arranged in such a non-fixed way. Introducing a new flexible module line (FML) in the welding shop will allow the OEM to minimise lead times and investment costs, especially when it introduces new models into its lineup. Moreover, it will enable the company to swiftly introduce new models as the FML warrants changing only the jig to fix the parts instead of repeating the scrap-and-build process.
While in the past it might have taken more time and considerable investment in retooling a production line for a new vehicle type, thanks to the upgrades to both body shop and vehicle assembly line, the same process can now be handled in about one-fifth of the time and at 10% of the investment, compared to conventional systems. These implemented changes will undoubtedly make Mazda mature and modernise, matching the modern and emerging scenario swiftly.