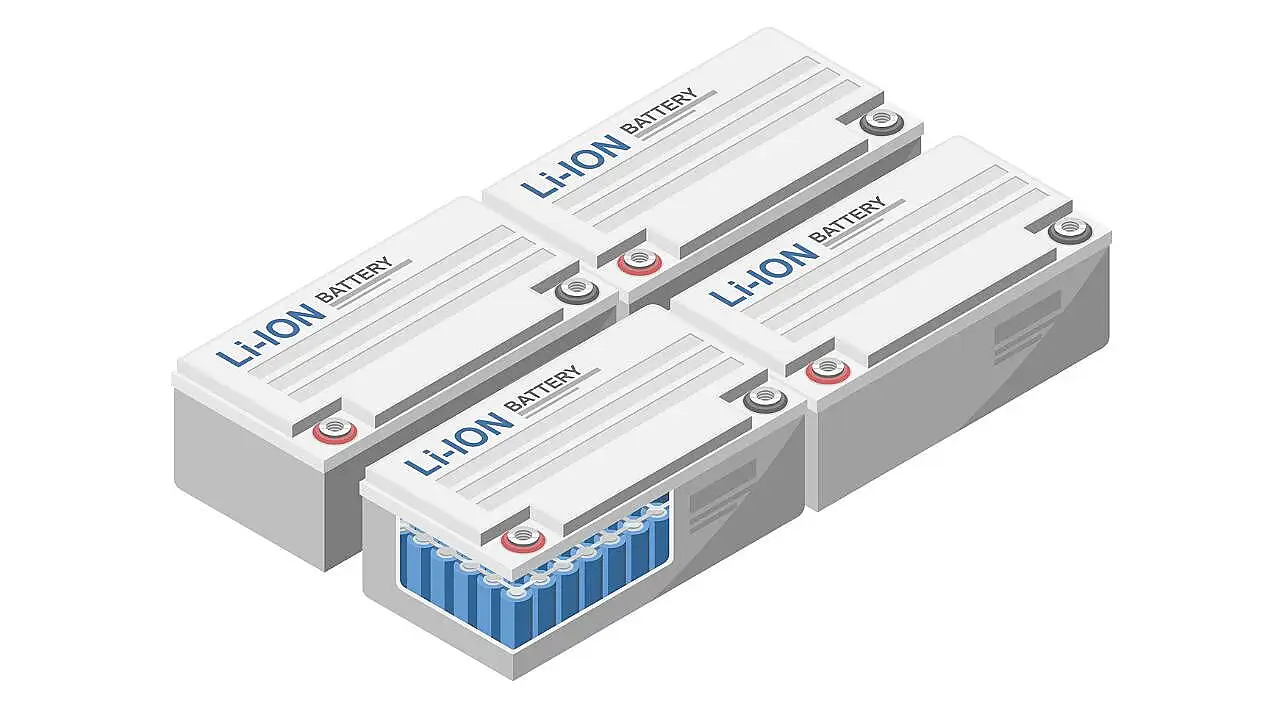
It is no secret that India is heavily dependent on imports of battery cells for sectors such as mobility, telecommunication, electronics and consumer durables. This is only obvious given its scarce reserves of critical metals such as lithium, cobalt, or nickel that are key inputs for battery cells and their development.
Some popular batteries include Lithium Iron Phosphate (LFP), Lithium Cobalt Oxide (LCO), Lithium Titanate Oxide (LTO) and Nickel Manganese Cobalt (NMC). With the advent of electric vehicles, lithium-ion batteries have taken centre-stage and it is in this backdrop that urban mining becomes relevant.
It involves extraction of precious metals from waste batteries and putting them back into the supply chain via recycling rather than digging the planet. While it is a smart way to build a circular economy ecosystem, it also helps meet the demand-supply mismatch of precious metals and safeguard the country against geopolitical risks.
The Ministry of Environment, Forest & Climate Change’s Battery Waste Management (BWM) Rules, 2022, are enabling an ecosystem that can sustain and grow without significantly burdening natural resources and lowering dependency on imports.
According to the Central Pollution Control Board (CPCB) website under the BWM Rules 2022, every producer and person or entity involved in manufacturing of battery must register with CPCB through the online centralised portal. Even recyclers need to do this, and the rules stipulate that the producer “shall have the obligation of extended producer responsibility” for the battery they introduce to ensure the “attainment of recycling or refurbishing obligations”.
Best In The World
ALN Rao, CEO, Exigo Recycling, believes that BWM Rules are one of the best in the world — “these are visionary rules and a trendsetter worldwide”. As he puts it, there are thousands of batteries that get disposed including NMC, LFP and LCO from mobile phones and laptops.
Under the BWM Rules, recyclers registered with CPCB will need to carry out their roles as per the guidelines laid down and furnish quarterly returns on the online portal. These relate to the “quantity of waste battery collected or received from various producers or entity, recycled quantities, compliance of material-wise recovery percentage as per recovery targets provided”.
The total quantity of waste battery processed will also be available on the CPCB portal on a quarterly basis. “Earlier, the rule was connected to the producer but now they have made recyclers independent. They can buy waste batteries from wherever and recycle them,” explains Rao.
The Centre has declared the composition of each battery type under the BWM Rules and recyclers have been mandated to ensure minimum recovery of battery materials. They are expected to upload Extended Producer Responsibility Certificates (EPRCs) generated by CPCB online based on “the recycled or refurbished quantities assigned to recyclers or refurbishers”, who can then sell the assigned EPRCs to producers in exchange of a waste battery.
MINIMUM USE OF THE RECYCLED MATERIALS OUT OF TOTAL DRY WEIGHT OF A BATTERY (In Percentage) | ||||
Type of Battery | 2027-28 | 2028-29 | 2029-30 | 2030-31 and onwards |
Portable | 5 | 10 | 15 | 20 |
Electric Vehicles | 5 | 10 | 15 | 20 |
2024-25 | 2024-25 | 2025-26 | 2026-27 | 2027-28 and onwards |
Automotive | 35 | 35 | 40 | 40 |
Industrial | 35 | 35 | 40 | 40 |
*Source: CPCB website.
Supply Risk
“India has not been able to develop a cell manufacturing industry or penetrate any part of the vast battery value chain, including precursors and cathode materials. This has led to the automotive industry rely on a handful of countries and creating a supply risk that can only be counterbalanced via target-based urban mining,” explains Rajat Verma, CEO, Lohum Cleantech.
According to him, the BWM Rules 2022 incentivise battery producers and importers to think and act on the larger environmental impact of their businesses. Domestic recycling — aka urban mining — will help “spur the nascent cell manufacturing ecosystem in the country, eventually lowering prices”.
Under the BWM Rules, batteries have been divided into four types: portable, electric vehicle, automotive and industrial. Producers have obligations on the minimum use of domestically recycled materials in the new battery. As for imported batteries, they must meet the obligation of “minimum use by way of getting such quantity of recycled materials used by other businesses, or by way of exporting such quantity of recycled materials”.
Rao says producers will have to declare the composition of metals and materials by which the CPCB portal can make public the composition of metals, materials and commodities placed in the market. The recyclers are given the target of recovery from these commodities.
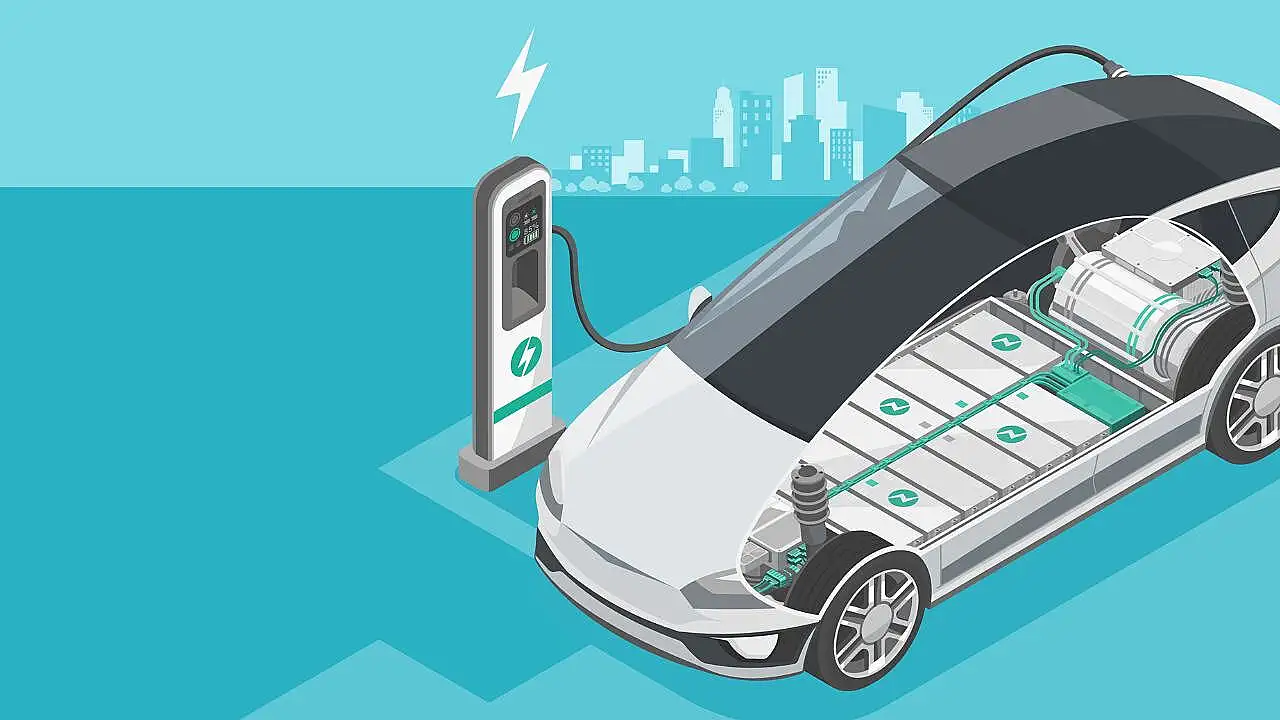
Harsh Penalties
“The market for this has also been created in these rules where certificates can be sold by the recyclers at a value they decide on and can be purchased by the producers to meet their targets for the year,” Rao explains. If producers cannot meet their yearly targets or are unable to buy these certificates in the stipulated time period, the rules dwell upon penalties as well as imprisonment of directors (or both) in select cases.
“Historically, every time you sell a product, there is waste that you produce. Under these rules, you should be recycling this scientifically. Battery waste management rules are a good start in this direction,” avers Nitin Gupta, Co-Founder and CEO, Attero Recycling. He believes one obvious area of improvement in the rules pertains to the amount of recycle content in batteries.
“There is a regulatory push towards recycling in China, the EU, and India. Large companies like BYD and Northvolt are either themselves into Li-ion battery recycling or have partnerships with recyclers. By the 2030s, recycled materials will become competitive vis-à-vis virgin-mined materials in terms of volumes. Most large auto companies with a long-term outlook understand this,” says Verma.
Lithium is seen as the “white gold” for EVs and lithium-ion batteries are the new oil that will define geopolitical relations. The metal is used across sectors, including pharmaceuticals, automotive, speciality chemicals, electroplating and paints.
In India’s recycled lithium market, auto accounts for 60%. “The Indian EV industry is still very small for meaningful volumes. We will see change from this year with more batteries deployed in commercial 2W and 3W applications,” adds Verma.
Risk Of Cobalt Shortage
With growing demand for cobalt — one of the primary metals for lithium-ion batteries — Gupta says that at the current utilisation rate, “we will run out of cobalt by 2030”. Lithium carbonate that was selling at INR 500 per kg a year ago is now INR 5,000 per kg.
According to a World Economic Forum report, lithium production has quadrupled since 2010 to surpass 100,000 tonnes for the first time in 2021. Nearly 90% of its production comes from Australia, Chile and China. Of this trio, China is the third largest producer and controls 60% of global battery-grade lithium refining capacity.
In terms of its end usage in 2021, 74% was in batteries, 14% in ceramics and glass with the balance in other industries such as pharma, adds the World Economic Forum report and BP Statistical Review of World Energy 2022, Statista.
In the context of the EU mandating a minimum 5% recycled metal content of cobalt and lithium (and others) in lithium batteries by 2023 and increasing it to 70% in 2030, Gupta says this will boost the circular economy and help in GDP and job creation.
RECOVERY TARGET FOR THE YEAR IN PRECENTAGE | |||
Battery Type | 2024-25 | 2025-26 | 2026-27 and onwards |
Portable | 70 | 80 | 90 |
Automotive | 55 | 60 | 60 |
Industrial | 55 | 60 | 60 |
Electric Vehicles | 70 | 80 | 90 |
*Source: CPCB website.
Changing US Stance
The US, under its Inflation Reduction Act, also refers to benefits for vehicles with battery components made or assembled in the country, or those that use critical minerals extracted in the US or in the countries it has free trade pacts with.
There is also stress on use of critical minerals recycled within the US, reflecting its changing policy on imports of precious metals for batteries and vehicles. Experts believe that “we are not far from a time” when precious metals extracted by recycling (urban mining) will rule the world market. Each nation will strive to keep these critical metals/ materials within its supply chain to ensure better pricing, improved carbon footprint and lowered forex exposure.
In the case of India, a critical area of concern is the export of black mass and lack of expertise in breaking this down into pure raw materials. “Around 1,000-2,000 tonnes of batteries are recycled each month and 1,000 tonnes of black mass exported. These are then routed back after refinement to India and sold at a premium,” says Vikrant Singh, Co-Founder, Director and CTO, BatX Energies.
Instead, urban mining of these precious metals will fulfil 35% of the demand-supply gap in metal availability. According to Gupta, the Centre is contemplating banning black mass exports since it contains critical materials such as cobalt and lithium. “The export of black mass poses geopolitical and forex risks,” he adds.
Black Mass
Every lithium-ion battery recycler in India creates black mass as an outcome of mechanical recycling. As Gupta explains, when these battery cells are shred along with density separation, two outputs emerge in the form of a combination of copper, aluminium and iron as well as black mass.
This black mass contains cathode active materials like cobalt, nickel, lithium and manganese along with anode materials such as graphite and separator materials like copper and aluminium. Attero, continues Gupta, can refine black mass and extract pure battery grade cobalt, lithium carbonate, graphite, and nickel.
“We are putting these back into the circular economy system. Our extraction efficiency is much higher than China with more than 98% of all battery materials in the pure form,” he says. Verma believes recyclers will need to up their game in order to handle the volumes coming in. Till now, most of them have been mechanically separating batteries into black mass, which is then exported for further processing.
“This will change and those recyclers who can effectively and efficiently process black mass into cathode active materials in an economic and environment-friendly manner will be at an advantage,” he adds.
Battery For Circular Economy
Prabhjot Kaur, Co-founder and CEO, Esmito Solutions, says the battery is an ideal candidate for the circular economy. Most rechargeable batteries offer good recoverability of raw materials that can be reused for making new ones. “We can avoid mining for extracting newer material and the growing pressure on mining can be combatted through the circular economy,” she adds.
The Centre has set up circular economy committees under the NITI Aayog umbrella to identify gaps and opportunities. “The waste batteries market is unorganised and the Government is trying to channelise the entire ecosystem. The BWM Rules will change recycling and collection of waste batteries in India,” says Singh.
Kwan Wongwetsawat, Senior Analyst – Asia Powertrain Forecasts, LMC Automotive, a GlobalData Company, points out that most passenger BEVs in India will use LFP batteries. With nickel and cobalt assuring more profits as expensive raw materials, recycling LFP batteries is less profitable in contrast.
“BatX Energies is creating an online portal where we will release data on how many batteries enter the market every month. We will then calculate when they will come in for recycling,” says Singh. BatX will also synchronise data collected on scrap availability using regional pin codes.
Open Platform
By the end of the day, every stakeholder in urban mining, right from the producer, buyer and seller to the scrap collector and recycler, will have to align and create an open platform for exchange of information and data storage.
“The recyclers will be evaluated as per output, delivery and tech used for extraction. The Government will provide financial support for advanced and improved extraction of further rare metals such as titanium and indium,” explains Rao.
According to him, this is just the beginning of the story with 11 more verticals to be added — e-waste, tyres, plastics, solar and oil are already seeing mandates. “In the next 2-3 years all commodities imported today will be used for secondary uses and recycled within India. They will be taken back to the industry and consumed,” forecasts Rao. Clearly, the sky’s the limit.
NB: Photos are representational.
Also Read: