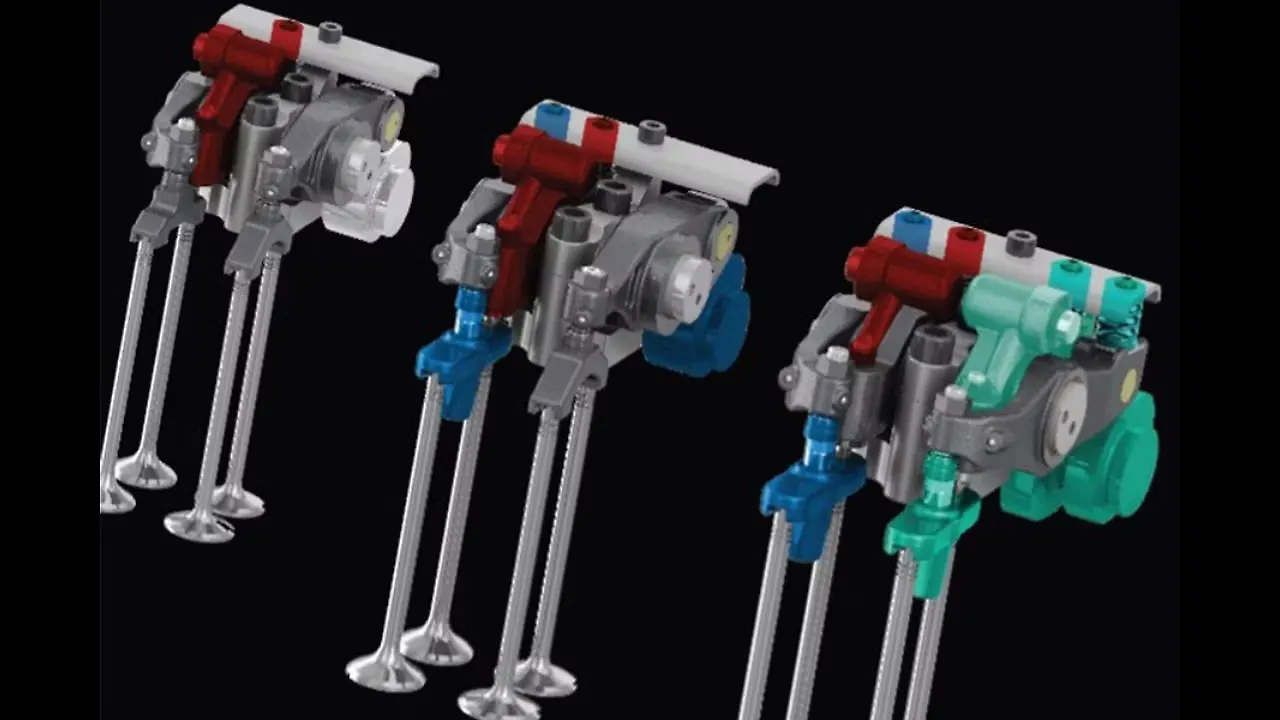
As the automotive landscape evolves, engine and vehicle OEMs are grappling with the immense task of adapting engine platforms to meet the diverse emissions regulations and power requirements of global markets.
Cummins Valvetrain Technologies is tackling this challenge head-on by developing modular valvetrain systems—versatile solutions that not only align with today’s needs but also anticipate future demands in emissions standards and alternative fuels like natural gas and hydrogen. This groundbreaking “Swiss Army Knife” approach to valvetrain technology enables OEMs to customise engines for different markets with minimal modifications, enhancing flexibility and extending the lifecycle of engine platforms.
Modular Valvetrain: The Swiss Army Knife of Engine Technology
Cummins’ engineers are crafting a modular valvetrain system capable of performing a range of functions, from engine braking to Cylinder Deactivation (CDA) and Late Intake Valve Closing (LIVC) for fuel economy improvements. 'We’re creating a valvetrain that does it all—a true Swiss Army Knife,' says Gabe Roberts, Director - Product Development, Cummins Valvetrain Technologies.
This modular system supports multiple configurations, empowering OEMs to integrate advanced functions based on specific market needs without redesigning the core engine. The result? Engines that are not only future-proof but also adaptable to diverse emissions standards as they tighten over the next decade.
Engine Braking: Scaling Up & Down With Global Reach
For over 60 years, Cummins has been a pioneer in engine braking technology, with the Jacobs Engine Brake now a staple in heavy-duty vehicles worldwide. As OEMs look to unify engine platforms for different global markets, the flexibility of Cummins’ braking technology becomes invaluable. The company’s compression release engine brake is widely used across commercial, agricultural, and off-road vehicles, and its modular design enables seamless scaling for different applications.
To meet the varying demands of global markets, the engine maker offers a spectrum of braking options. In regions that require standard compression release braking, it provides this solution as a baseline, while markets demanding higher performance levels can opt for High Power Density (HPD) brakes. These scalable options reduce the need for driveline retarders, offering OEMs a streamlined, cost-effective path to meet market-specific requirements.
Modular Solutions For Emissions Control
In a world where emissions regulations vary significantly, OEMs face the challenge of balancing NOx and CO₂ reductions across markets. Cummins has risen to the challenge with its in-engine modular emission technologies, including CDA and Variable Valve Actuation (VVA). By leveraging its well-established engine brake technology, it has adapted these components to meet strict emissions standards in both North America and Europe.
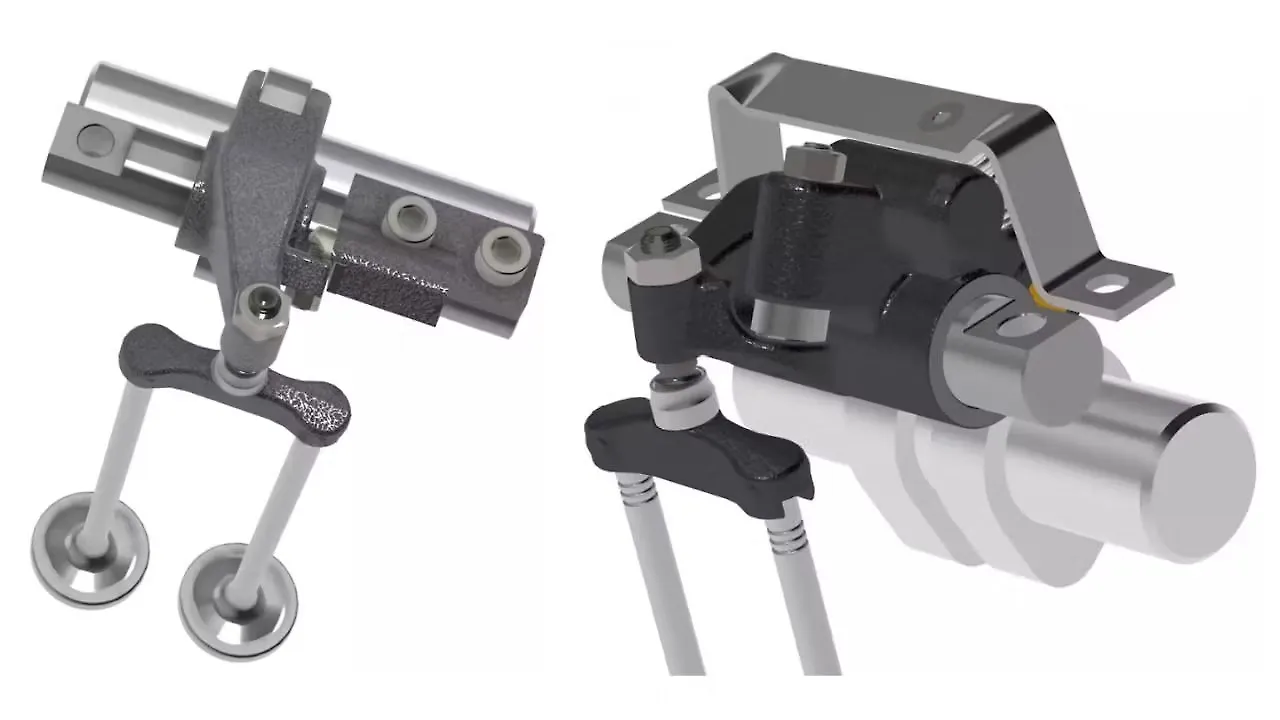
CDA technology enables selective cylinder deactivation in low-load scenarios, allowing a six-cylinder engine to function as a three-cylinder engine, thereby reducing both NOx and CO₂ emissions. This innovation, essential to the “Keep It Hot” aftertreatment strategy, is set to play a significant role in the US as emission regulations become more stringent. In Europe, where CO₂ reduction is a primary focus, VVA provides critical fuel efficiency and emissions control benefits. Cummins’ modular approach makes it possible to integrate both CDA and VVA within the same engine, allowing OEMs to cater to diverse regulatory requirements on a single platform.
Active Decompression & Hybrid Transition
Cummins’ valvetrain technologies are also pushing the boundaries of start-stop and hybrid applications. Active Decompression Technology (ADT) allows for smooth transitions between electric motor (eMotor) and internal combustion engine (ICE) modes, crucial for hybrid powertrains. This feature appeals to a wide range of applications, from light-duty vehicles to heavy-duty trucks, enabling enhanced driveline electrification. ADT not only optimises fuel efficiency but also ensures a seamless driving experience, making it an attractive solution for modern, hybrid-ready engines.
Systemic Approach To Fuel Efficiency
In the quest for fuel efficiency, Cummins goes beyond individual components to consider the entire vehicle system. Every part of the vehicle, from the engine to the aftertreatment system and transmission, plays a role in fuel consumption. Its modular technologies are designed with this holistic perspective in mind. For instance, CDA and ADT contribute to fuel savings, but Cummins also optimises valvetrain design to reduce engine friction and support low-viscosity oils. Advanced in-house solenoid technology and rigorous testing ensure that these components perform consistently, further enhancing fuel economy.
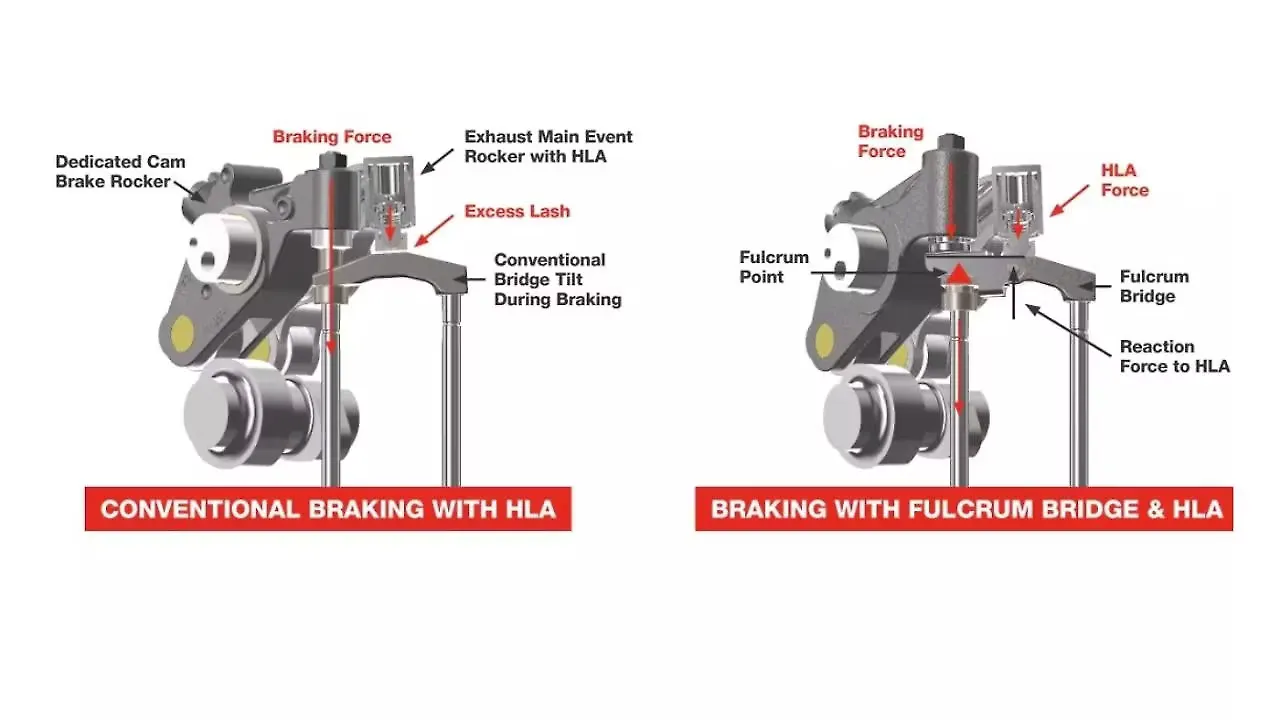
Lash-less Valvetrains
An essential factor in improving fuel efficiency is the use of lash-less valvetrains—systems with Hydraulic Lash Adjusters (HLAs) that eliminate the need for manual adjustments over time. Previously incompatible with engine brakes, Cummins’ innovative Fulcrum Bridge and Spring Bridge technologies have now made HLAs viable for heavy-duty engines. This innovation ensures consistent performance throughout the vehicle’s life, enhancing both fuel efficiency and emissions control.
Future Of Modular Engine Technology
Cummins’ modular valvetrain technologies are paving the way for a new generation of adaptable, efficient, and future-ready engines. With innovations like CDA, VVA, ADT, and lash-less valvetrains, the company provides OEMs with a versatile toolkit that meets the demands of various markets and regulatory environments. This adaptability is essential as OEMs strive to streamline their engine platforms while addressing global emissions standards and the shift toward alternative fuels.
In an industry where regulatory landscapes and consumer expectations are constantly evolving, Cummins Valvetrain Technologies is empowering OEMs to stay ahead of the curve. By “future-proofing” engine designs with scalable, modular solutions, the engine maker not only addresses today’s demands but anticipates tomorrow’s challenges, positioning itself—and its partners—at the forefront of a rapidly changing industry.
With Cummins’ modular approach, engine and vehicle manufacturers can seamlessly adapt to the diverse needs of global markets, ensuring that their vehicles meet regulatory standards while remaining robust, reliable, and fuel-efficient. The result? A new era of engines ready to power the vehicles of the future.
Also Read:
Cummins ReCon - Mastering The Craft Of Engine Remanufacturing