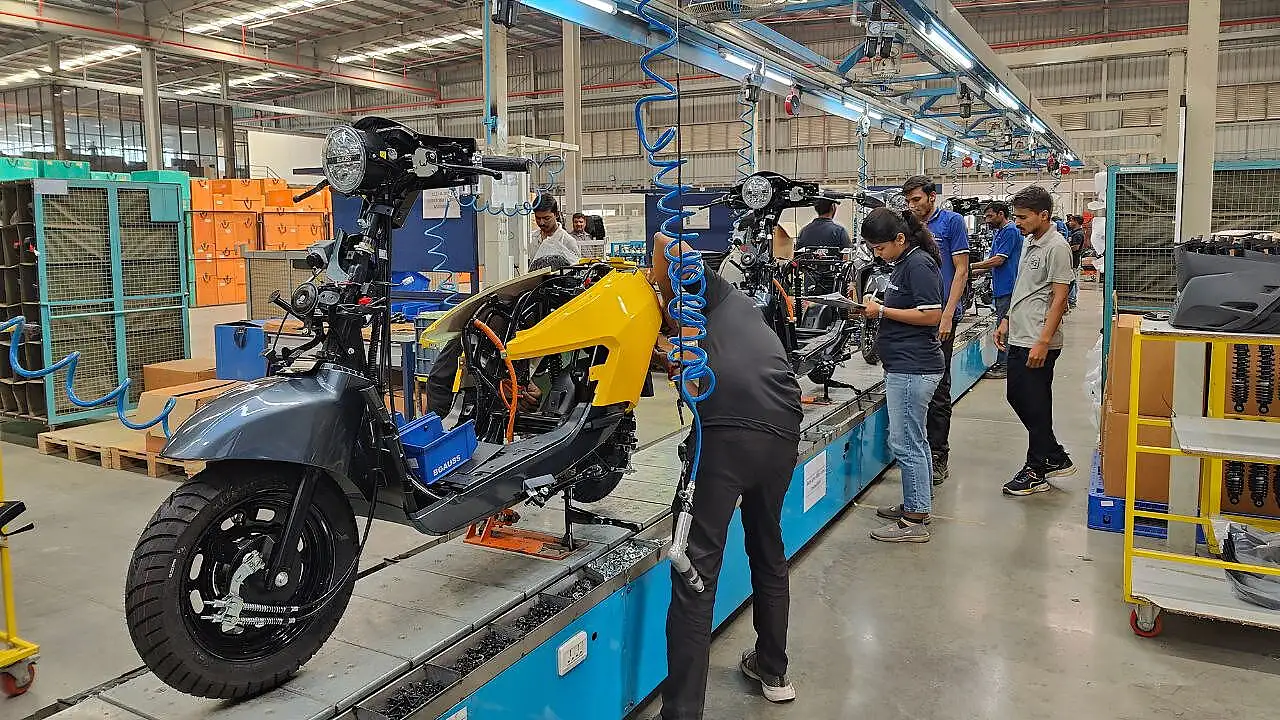
With over 42,000 vehicles rolling off its production lines in just over three years, BGauss Auto has firmly established itself as a formidable player in India’s electric two-wheeler market. Notably, the company emerged as the seventh best-selling EV brand in the last financial year, capturing a 3% market share.
A brand under the RR Global umbrella, BGauss operates with a sharp focus on safety, comfort, and reliability—key differentiators in a fiercely competitive industry. While safety and comfort are integral to design, the brand’s commitment to reliability stems from its meticulous manufacturing practices, ensuring superior build quality and performance.
Currently, the company produces two models—BG C12 and RUV 350—each available in three variants. Strengthening its innovation-driven approach, BGauss has already filed over 80 patent claims, showcasing its commitment to technological advancement.
Overcame Adversity
How did a company that launched operations amid the COVID-19 crisis—arguably one of the most challenging periods for global industries—achieve such remarkable growth? The answer lies in a meticulously planned manufacturing ecosystem and a commitment to quality, reinforcing its ‘Make in India’ initiative.
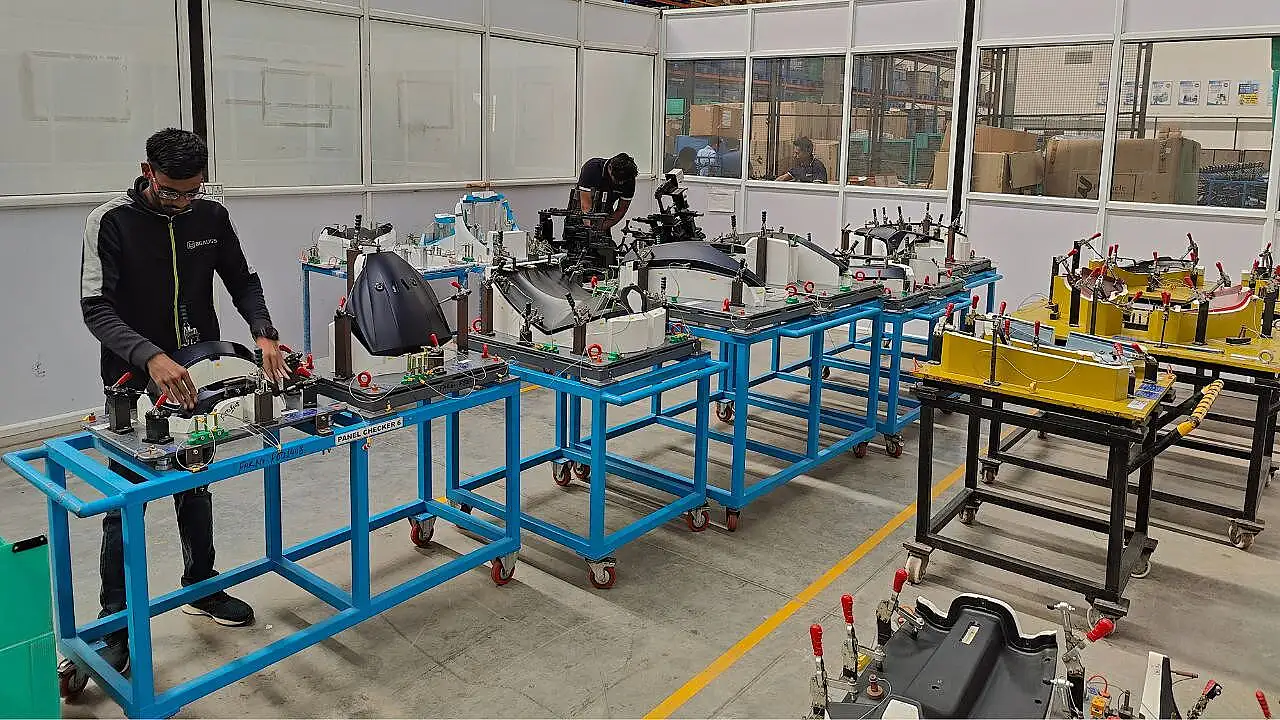
Operating from a 69,000 sq ft facility, BGauss Auto currently produces around 7,000 electric two-wheelers per month, running a single-shift operation. A crucial factor behind this efficiency is its highly localised supply chain—88% of the 550 sourced components come from suppliers within a 100-kilometer radius, while the remainder is procured from Delhi NCR and southern India.
Quality control is at the core of BGauss’ manufacturing philosophy. The company has implemented rigorous inspection protocols to ensure that every component meets stringent standards before entering production. Each part undergoes a comprehensive quality assurance process, including system audits, process audits, and Production Part Approval Process (PPAP) audits.
Blending Efficiency, Quality
Quality assurance at BGauss Auto goes beyond standard inspections—it is a fusion of precision engineering and innovative processes designed to ensure seamless production and superior product reliability. Among its standout quality control measures is the ‘panel checker’ for FRP components, which meticulously verifies the profile of these critical parts, ensuring dimensional accuracy. Another notable innovation is the ‘chassis relation gauge,’ a sophisticated tool that inspects 39 critical points for structural conformity, improving safety and durability.
Battery reliability is paramount, and every single unit received undergoes a comprehensive inspection before being cleared for integration. These stringent quality control protocols ensure that only flawless components move forward in the production line.
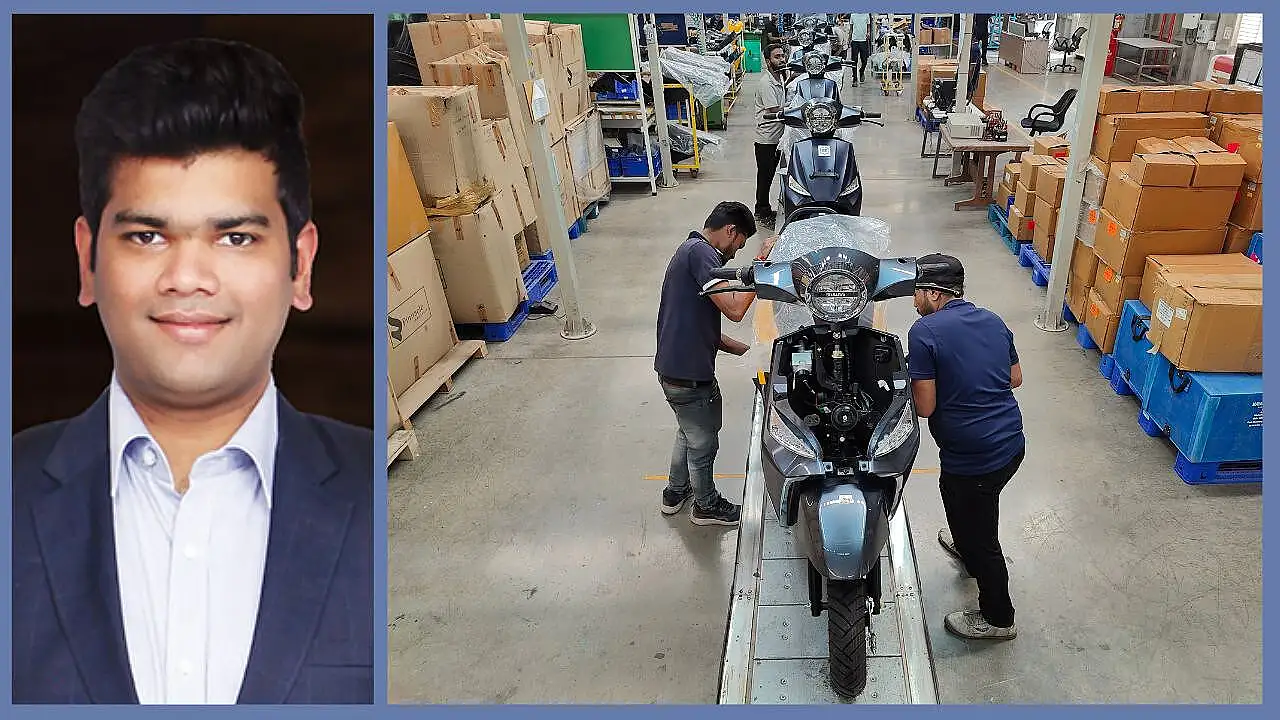
Precision-Driven Manufacturing
At the heart of BGauss’ manufacturing lies a meticulously structured assembly process, designed to maximise throughput, precision, and reliability. The production workflow begins with a pre-assembly stage, consisting of 13 sub-assembly stations and 12 main assembly stations, ensuring a seamless integration of components before final assembly. With a TAKT time of approximately five minutes per unit, the company efficiently produces 100 electric two-wheelers per shift, balancing speed with uncompromising quality.
A key differentiator in BGauss’ assembly line is its strategic dual-side feeding approach, which optimises workflow and minimises handling risks. Heavier components such as wheels and motors are introduced from the left side, while delicate, high-precision parts like the handlebar and instrument cluster are integrated from the right side. This purposeful layout enhances operational efficiency while reducing the risk of damage, ensuring superior product integrity.
To maintain rigorous quality control, three critical checkpoints are positioned across the assembly line—at pre-assembly, mid-main-assembly, and final inspection—preventing non-conforming products from advancing further. Additionally, the integration of over 140 Poka-Yoke mechanisms enhances assembly precision, eliminating potential defects before they impact the final product. Advanced testing equipment, including dynamometers and race cone pressing machines, further ensures built-in quality assurance across all production stages.
With sustainability at the core of its operations, BGauss has embraced the Kanban system to optimise supply chain efficiency. This approach regulates inventory flow and replenishes PP boxes for frequently used components such as motors, plastic parts, harnesses, and coloured parts, effectively reducing material wastage and reinforcing lean manufacturing principles.
Strategic Approach
When asked about supply chain challenges, Hemant Kabra, Founder & Managing Director of BGauss, shared an insightful perspective with Mobility Outlook: 'Automotive success is deeply rooted in supply chain mastery. While manufacturing itself is relatively straightforward, managing a robust and agile supply chain is where the real challenge lies. We have learned this through experience, and it remains a fundamental aspect of our operations.'
Kabra emphasised that Chakan, where BGauss is headquartered, provides an unique advantage. As one of India’s most prominent automotive manufacturing hubs, Chakan boasts an ecosystem of seasoned suppliers who have long catered to major OEMs. This strategic location enables BGauss to leverage the well-established supplier base, ensuring efficient procurement and minimal disruptions despite the industry's inherent challenges.
Acknowledging that supply chain hurdles do arise, Kabra confidently stated that BGauss has proactively adapted to navigate and mitigate these challenges, ensuring uninterrupted production and seamless deliveries.
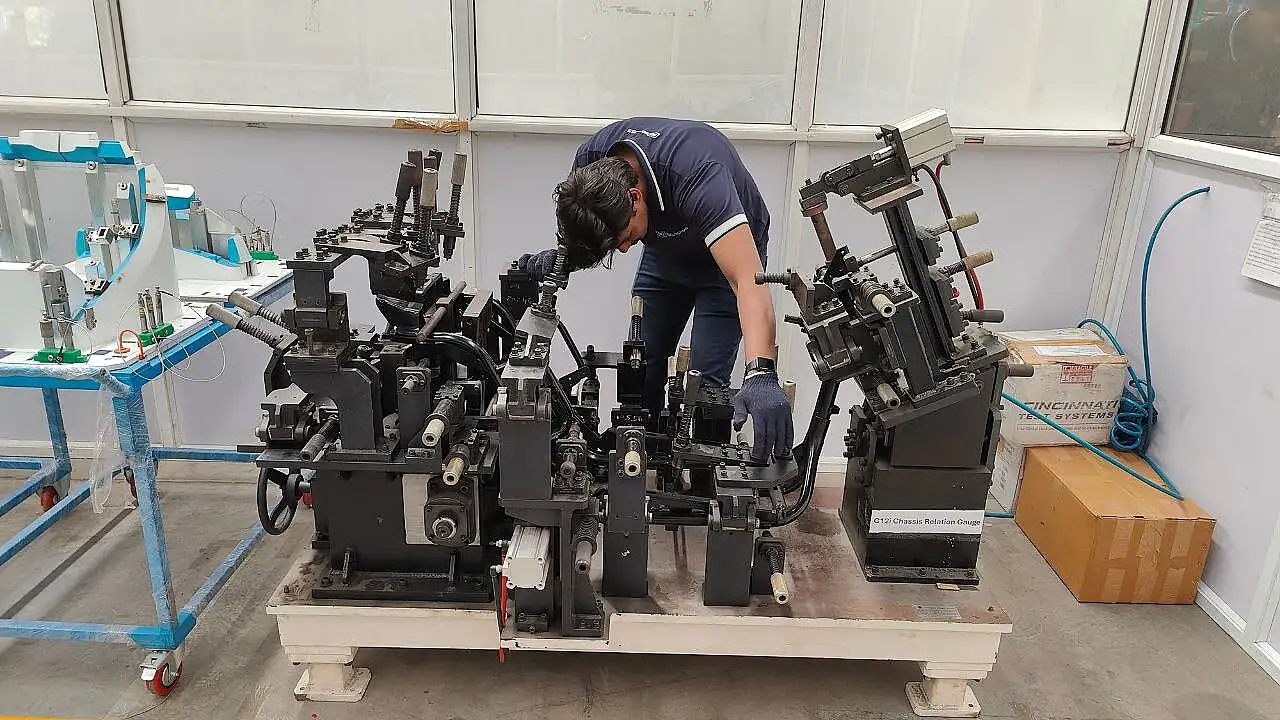
Leveraging Legacy Expertise?
As a part of RR Global, a $2 billion multinational conglomerate with a manufacturing presence in 90 countries, BGauss inherits a legacy of engineering excellence. Founded in 2020, BGauss is the latest venture of RR Global, a company with over 13 state-of-the-art manufacturing facilities in India and expertise across multiple industries, including cables, wires, switches, LEDs, BLDC fans, pumps, relays, and multi-level parking systems under the Parkon brand. Given RR Global’s deep-rooted capabilities in motors, wiring, and electrical components, the transition into electric two-wheelers may have seemed like a natural progression.
However, as Kabra admits, the shift was far more complex than anticipated. Reflecting on the journey, he shared, “Before entering the business, I believed we could seamlessly integrate our existing expertise to manufacture electric two-wheelers. However, I quickly realised that it required an entirely different approach. While we had a strong foundation in components, the journey to building a reliable, high-performance EV demanded a completely new level of innovation, adaptability, and understanding of the segment.”
BGauss has since navigated this steep learning curve, integrating precision manufacturing, quality control, and advanced engineering to develop cutting-edge electric two-wheelers that meet evolving market demands. By combining parent-company expertise with EV-specific innovation, BGauss has successfully positioned itself as a rising force in India’s electric mobility landscape.
Building Strong Talent Pool
For any startup, attracting and retaining the right talent is a crucial challenge, and the electric vehicle (EV) industry is no exception. Unlike traditional automotive sectors, where deep-rooted expertise spans decades, the EV ecosystem in India is relatively young, with industry veterans having, at most, a decade of experience. This posed a significant hurdle for BGauss in its formative years.
Reflecting on the early struggles, Kabra said, “When we entered the EV space, the most experienced professionals in the industry had only about 10 years of expertise. While mechanical engineering talent was abundant, specialised knowledge in powertrains, battery architecture, and software integration was still evolving. Four years ago, hiring the right people was an uphill battle. However, the ecosystem has matured significantly since then, making it relatively easier to build a strong, knowledgeable team today.”
With a meticulous blend of innovation, precision engineering, and sustainability, BGauss has carved a niche for itself in India’s electric two-wheeler segment. By integrating smart manufacturing processes, stringent quality protocols, and eco-friendly production practices, the company ensures that every vehicle rolling off its assembly line embodies safety, reliability, and superior performance.
Looking ahead, BGauss is poised to broaden its portfolio with the launch of two new e-scooters, while also setting its sights on global markets through strategic exports.
Also Read:
User Experience, Product Durability - Key Mantras For BGauss’ Sustainable Growth