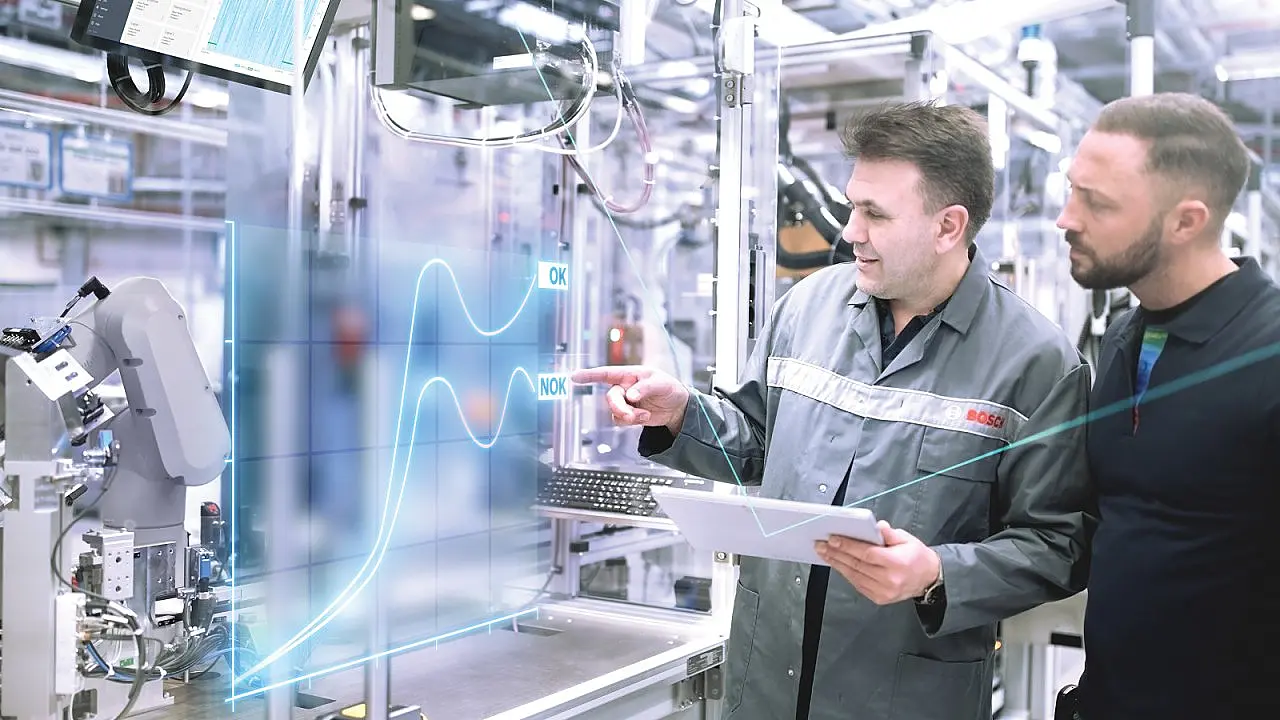
New-age technologies are bringing in disruptions in the industry. While these changes in dynamics have always brought great opportunities for the industry players, they also bring challenges, mostly in the form of training the existing manpower.
According to the European Commission, three-quarters of companies in the EU report difficulties in finding qualified workers, and only 37% of adults engage in regular further professional development.
The German technology company, Bosch say it’s something that affects nearly every company. An ageing society and labour shortages are social trends shaping the 21st century. Bosch hasn’t been spared either.
Stefan Grosch, Member of the Bosch Board of Management and Director of Industrial Relations, says the company is facing up to these challenges as a committed employer and is focusing on training and upskilling as well as on intelligent technology that makes associates’ work easier.
In 2022, the company offered more than 30,000 training seminars worldwide, with more than 520,000 Bosch associates taking part. One focus was technological expertise. More than 130,000 participants were able to acquire knowledge in technologies of the future, such as electromobility, software engineering, and Industry 4.0.
This commitment to training does not end at the company’s factory gates. With academies, training centres, and training courses, the company also offers other companies, customers, and interested parties the opportunity to acquire knowledge.
On the subject of Industry 4.0, for example, the company makes more than 100 training programmes on digitalisation and connectivity in manufacturing available externally through Bosch Connected Industry, Bosch Rexroth, and training institutes.
Grosch said that the company promotes lifelong learning. This is the key to lasting professional and business success.
He added that it is also essential for a country’s economic output. “If we want to maintain prosperity in Germany and remain successful as an exporting and industrial nation, we must invest even more in upskilling and intelligent technology and actively encourage people to enroll,” Grosch says.
Bosch offers all associates the opportunity for professional development. In 2022, the company associates attended one to two training courses on average and completed two to three web-based courses. Roughly 6,000 seminars deal with technologies of the future. Lasting an average of two days, these seminars are particularly thorough.
Digitalisation often determines not only the topic and content of training courses but also their form: in 2022, online courses accounted for two-thirds of all training hours for associates.
“Digitalisation is becoming a training booster for companies and their workforce; it enables learning independent of place and time and gives people a chance to experience new technologies such as artificial intelligence firsthand,” says Bosch CDO and Member of the Board of Management Dr Tanja Rückert. Last year alone, the company spent some €300 million on professional development for its associates.
“At Bosch, we develop technology that is ‘Invented for life.’ To do that, we need the right team with talented people in all positions, and we need them to continuously improve and expand their skills,” Grosch added.
Upskilling In Focus
The Boston Consulting Group estimates the loss in potential output for the German economy to be €86 billion. The German Chamber of Commerce and Industry puts it even higher, at just under €100 billion– annually.
In an international comparison of the nations with the strongest economies, the losses suffered by the German economy are the second highest after the United States.
Grosch believes that having highly qualified personnel is a decisive competitive advantage. As a manufacturer and technology company, the company pays close attention to professional development for its associates in manufacturing operations.
This year, for example, its mobility business launched the LernWerk initiative to train 24,000 associates in readiness for the digital transformation, initially at German sites.
“Manufacturing is where value creation begins in our company. This is where we lay the foundation for business success. Our progressive and efficient manufacturing operations feature an impressive degree of connectivity and digitalisation. One important prerequisite for this is ensuring associates receive the necessary training,” Rückert says.
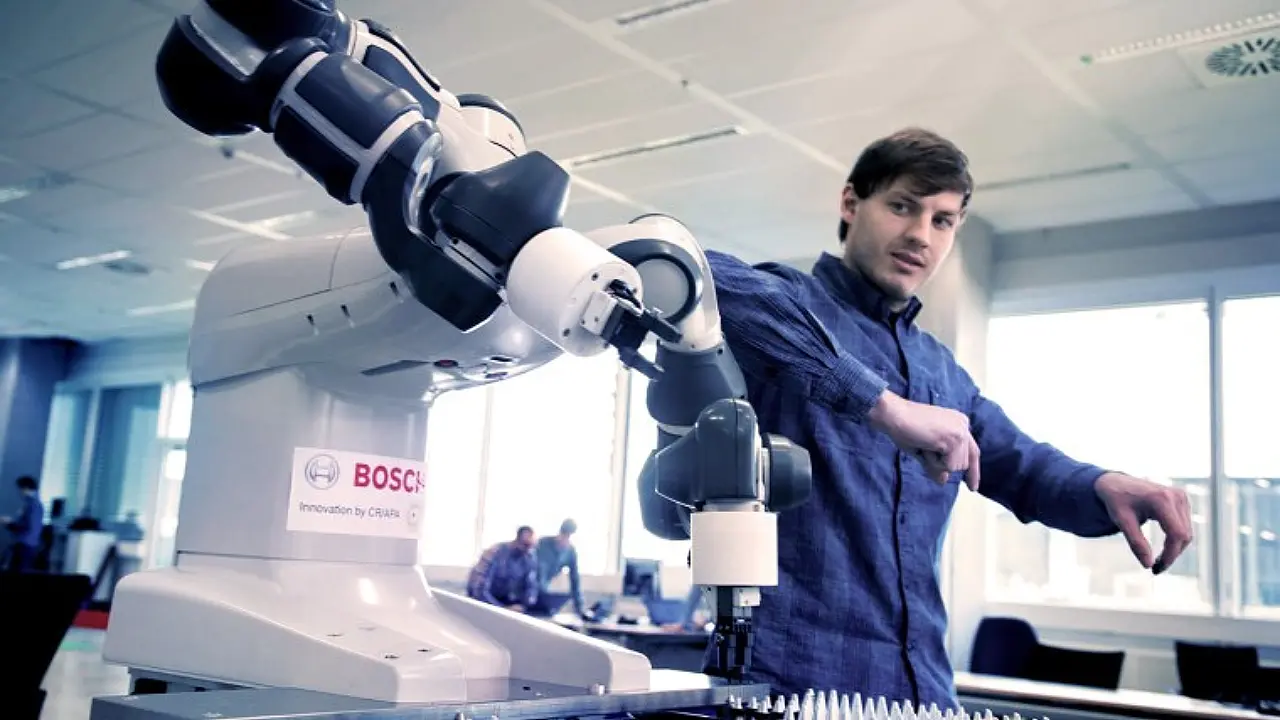
As part of Bosch’s training programme for other companies, its Industry 4.0 courses are additionally offered in Germany and elsewhere through partners such as chambers of industry and commerce, colleges, and universities.
“From France and the Czech Republic to China, India, and Singapore, companies are training their manufacturing workers according to the German model. Industry 4.0 training ‘made in Germany’ is becoming the global standard,” Rückert says.
In addition to vocational training and professional development programmes, Bosch develops training systems that are compatible with the syllabuses of industrial and educational institutions.
Bosch Rexroth is launching its new Automax 600 training system. Using internationally standardised programming languages and open interfaces gives users practical experience in digitalising production processes – including controlling robotic systems, operating autonomous transport systems, and using cloud applications such as data analysis and machine learning based on artificial intelligence.
Automation Is Key
There are various remedies for labour shortages. One is vocational training and professional development; visa programmes for skilled workers are another. And technology also has a key role to play.
Bosch Rexroth, for example, has developed an automation solution that no longer requires any previous specialist knowledge of automation. Users of ctrlX Automation can choose from over 30 popular programming languages.
The company is taking a similar approach to hydraulics. In the future, customers can use H4U to integrate Bosch Rexroth software into the automation architecture they are already familiar with, eliminating the need to build their own hydraulics expertise.
“By opening up systems, making technology interoperable, and moving hardware applications into software, we reduce complexity and dependencies, such as on specialists,” Rückert says.
Moreover, technology makes life easier for workers whose tasks are monotonous, strenuous, or hazardous. Robotics supports loading and palletising, Artificial Intelligence helps with the optical inspection of workpieces, augmented reality guides through work processes, and driverless transport systems take goods directly to where they are needed.
“Only by increasing productivity can we manage the impact of an aging society. This calls for well-trained specialists, as well as technology that allows them to work rationally and efficiently. The interplay between humans and machines and between training and digitalisation is a key success factor,” Grosch says.
Looking at the metrics for the first half of the year, the company expects to train around 50% more participants in 2023 than it did the year before, he concluded.
Also Read