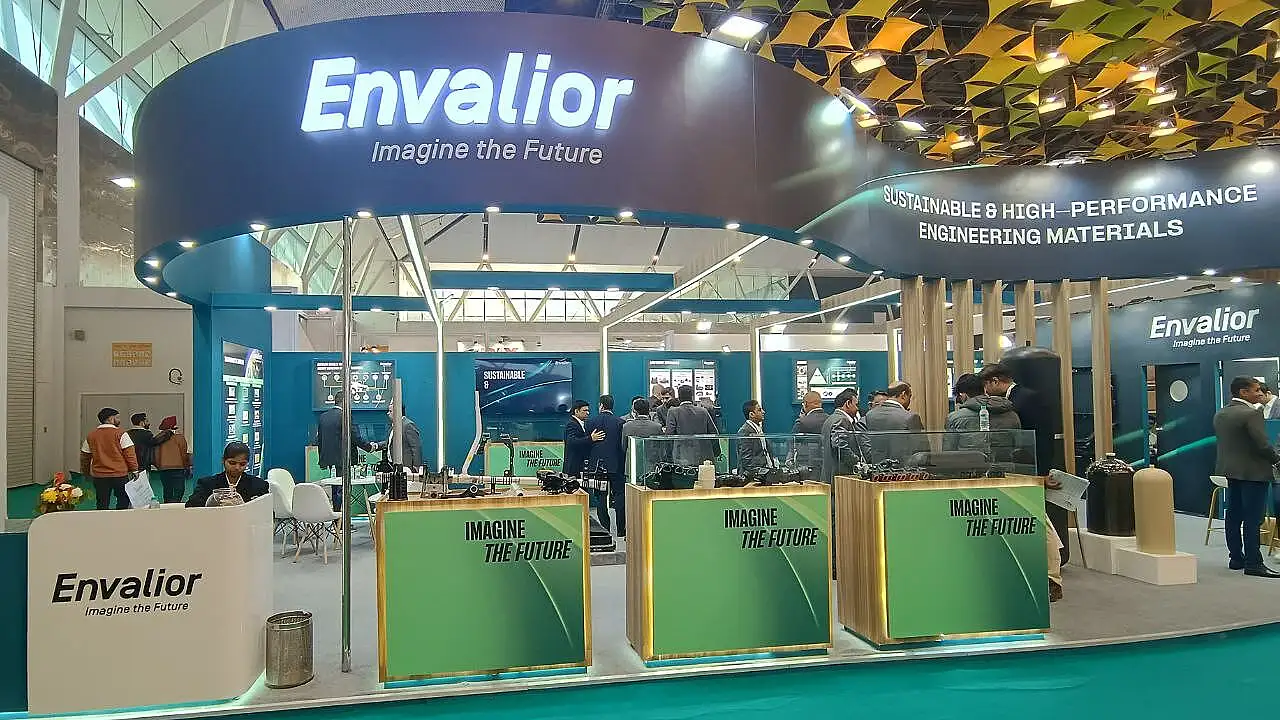
As the automotive industry pushes for greater fuel efficiency and lower emissions, the demand for advanced materials is reshaping vehicle design. Envalior, a global leader in engineering materials, is at the forefront of this transformation, offering tailored solutions that enhance performance, safety, and sustainability.
By developing high-performance materials with superior heat and electrical resistance, the company enables the creation of cutting-edge connected car components that meet stringent global safety standards. For instance, its Advanced Thermoplastic Composites, Tepex, provide a game-changing alternative for OEMs and Tier-1 suppliers striving to reduce vehicle weight without compromising strength. These materials allow for thinner, lighter structural components while maintaining durability.
Leveraging advanced computer-aided engineering (CAE) services, Envalior helps manufacturers predict part fatigue and failure modes, ensuring optimised designs with minimal defects. As lightweighting becomes a crucial factor in next-generation mobility, Envalior’s innovations are paving the way for stronger, safer, and more efficient vehicles.
Greener Automotive Future
As the automotive industry intensifies its focus on sustainability and the circular economy, Envalior is driving change with a strategic emphasis on the three Rs: Reduce, Reuse, and Recycle.
Speaking to Mobility Outlook, Dr Nileshkumar Kukalyekar, Business Director – South Asia, Middle East & South Africa, said, “Sustainability is at the core of our operations, guiding every aspect of our material innovation. Lightweighting in automotive materials is one of our most impactful contributions to reduction. By replacing traditional metals with high-performance plastics, we help create lighter vehicles that enhance fuel efficiency and cut carbon emissions. In electric vehicles, this directly improves battery performance and range.”
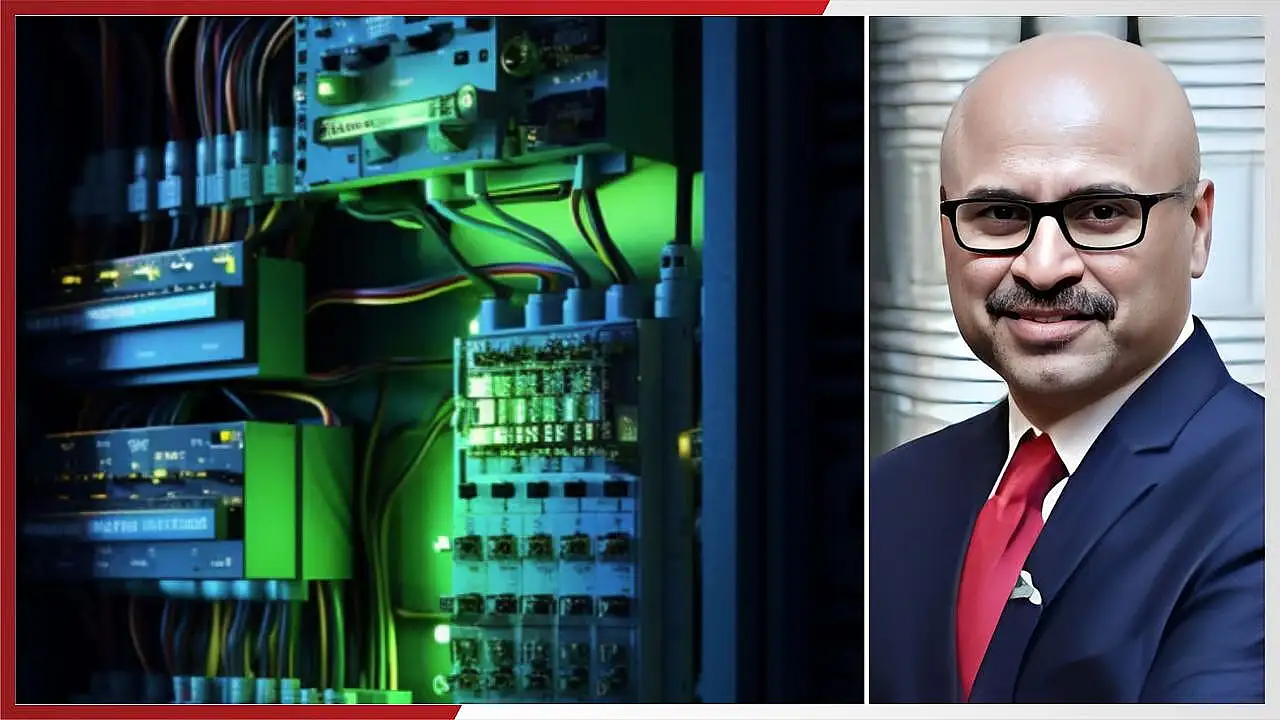
Beyond reduction, reuse and recycling play a vital role in the company’s sustainability strategy. It continuously refines its manufacturing processes to minimize waste while exploring new applications for engineering plastics.
A prime example is its pioneering work in recycling ocean plastics. Every year, around 640,000 tonne of discarded fishing nets pollute the oceans—Envalior repurposes 2,000 to 3,000 tonne of these in India alone, transforming them into high-performance materials for automotive and electrical components. Global brands like Ford and Schneider Electric integrate these recycled materials into truck components and switchgear products, respectively, he pointed out.
The company is also tackling the challenge of recycling tyres and materials from end-of-life vehicles. “Maintaining high performance and safety standards while incorporating recycled content is a complex task. But our expertise in material science allows us to develop recycled plastics that match or even exceed the performance of virgin materials Kukalyekar noted.
Envalior’s commitment to sustainability extends beyond materials to its operations. At its Ranjangaon plant, a solar power facility generates 1.2 megawatts of electricity, covering 30% of the plant’s energy needs. The remaining power is sourced from wind energy, bringing the company closer to achieving 100% renewable energy in its Indian operations, he said.
Innovating For EVs
As electric vehicles (EVs) evolve, the need for lightweight, high-performance materials is greater than ever—especially in battery systems and connectors. Envalior offers advanced solutions that enhance efficiency, safety, and sustainability.
“One of our key focuses is reducing the weight of EV components. Battery enclosures, traditionally made from heavy metals, add significant weight to vehicles. We’ve developed proprietary composite sheets that maintain strength while dramatically reducing weight, improving range and efficiency,” Kukalyekar explained.
Thermal management is another critical challenge. To address the risk of battery fires, the company has developed flame-retardant materials that efficiently dissipate heat and slow thermal runaway, giving passengers crucial extra time to exit in case of an emergency. Additionally, sustainability is a priority—not only does lightweighting improve vehicle efficiency, but Envalior is also incorporating recycled content into its materials to reduce the overall carbon footprint of EVs.
Local Strength, Global Reach
Envalior manufactures a range of high-performance engineering plastics, including polyamide-6, PBT, and PA46, with most of its supply sourced locally in India. “We meet the majority of domestic demand through our local facilities while also exporting to China, the Asia-Pacific, and other regions,” he noted.
Imports account for just 2–5% of its supply, primarily for specialized materials where local production is not yet viable. “Our strong manufacturing base in India allows us to provide high-quality, cost-effective solutions with minimal reliance on imports. Balancing quality, cost, and sustainability remains our top priority,” he added.
Harnessing Digitalization
Digitalization plays a pivotal role in Envalior’s operations, enhancing efficiency, safety, and innovation. One of its key applications is virtual reality (VR) training in manufacturing plants. “While our industry isn't as hazardous as some chemical sectors, safety is a core value for us. With VR, new employees can gain hands-on experience in safety protocols and plant operations within a controlled environment, improving preparedness and reducing risks,” he said.
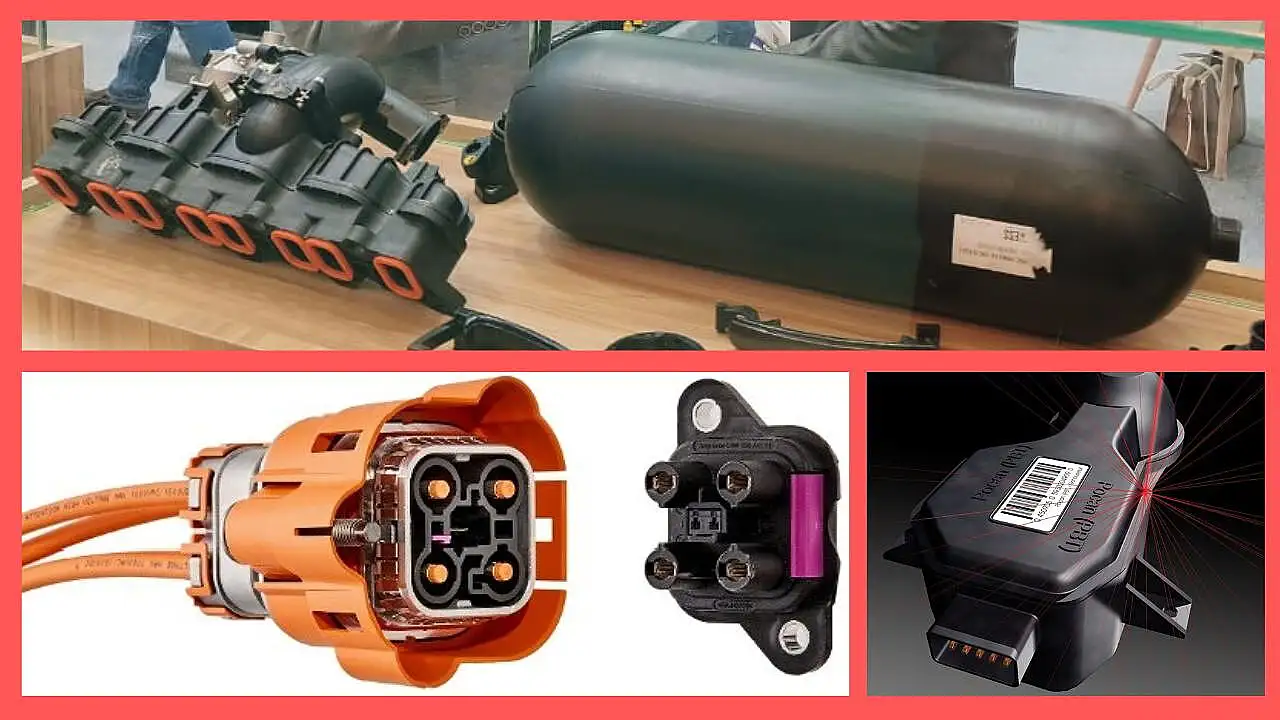
Beyond training, Envalior’s R&D centre in Pune is driving industry advancements by exploring next-generation solutions, including hydrogen storage for future automotive applications. By integrating digital tools into research and production, the company continues to develop materials that are lighter, safer, and more sustainable.
Merging Strengths
The creation of Envalior through the merger of DSM and Lanxess brought both opportunities and challenges. One of the key advantages was the complementary nature of the two companies’ portfolios. DSM specialized in sustainable, safety-focused materials, while Lanxess had a strong foothold in lightweighting solutions for the automotive industry. “Rather than competing, our strengths aligned perfectly, allowing us to offer a broader, more integrated range of high-performance materials,” he mentioned.
However, cultural integration was a more complex challenge. “Merging two organizations is like a marriage—it’s not just about aligning operations, but also values, leadership styles, and approaches to innovation,” he explained. Instead of favouring one corporate culture over the other, the company saw an opportunity to build a new, unified identity that blended the best aspects of both DSM and Lanxess while preparing for the future.
Another key challenge was harmonizing technological processes, digital initiatives, and sustainability efforts. “Both companies had unique approaches to IT systems, production processes, and supply chain networks. We invested significant time in streamlining operations, integrating digital tools, and ensuring employees were equipped with the right training and resources to adapt to the new structure.”
Through a thoughtful and well-executed integration, Envalior has positioned itself as a dynamic player in the high-performance materials industry, poised to contribute to innovation and sustainability in automotive and beyond.
Also Read:
Envalior Joins UN Global Compact, Sets Bold Path To Carbon Neutrality By 2040