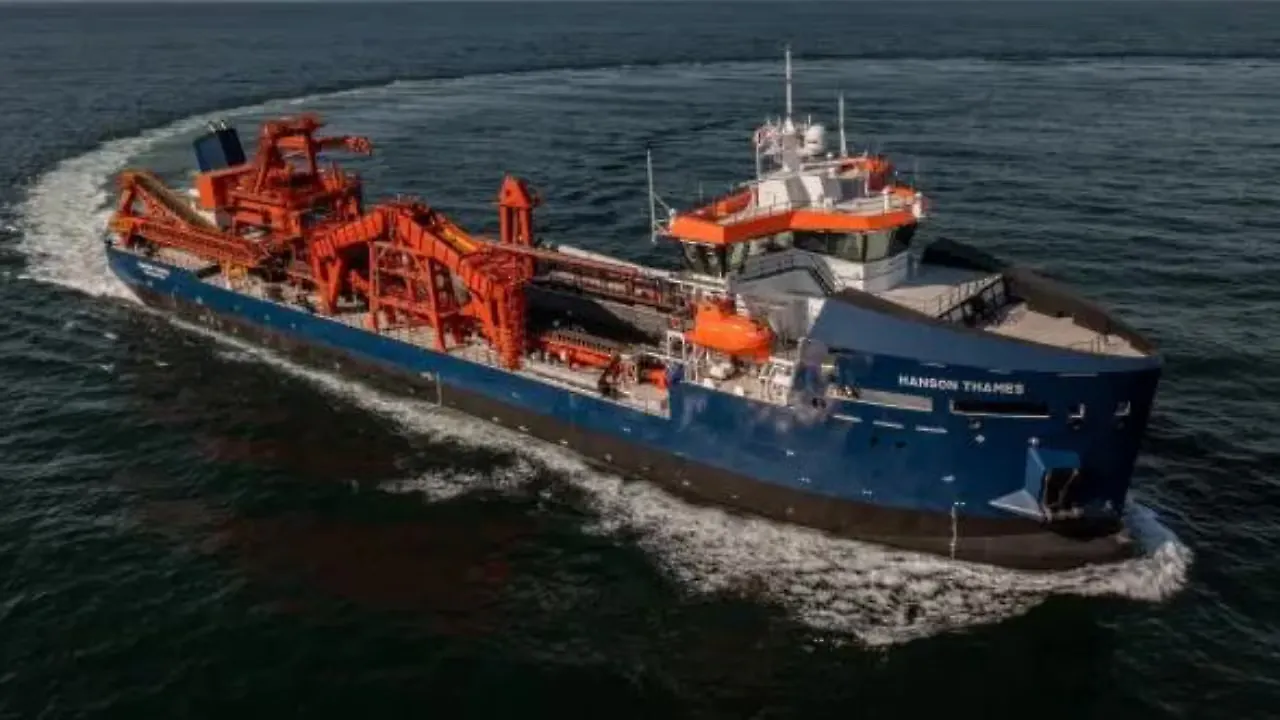
Damen, a family-owned business that stands for fellowship, craftsmanship, entrepreneurship, and stewardship, has recently announced that the second vessel of its new Marine Aggregate Dredger (MAD) 3500 class has now completed her sea trials.
As of January 2022, she has entered service with her owner, Hanson UK, a leading supplier of building materials to the UK market, replacing an obsolete vessel.
With a large part of the English dredging fleet that is now several decades old, the MAD 3500 presents an opportunity to other operators in this sector, as it enables them to take advantage of the significant advances made in aggregate dredging design and technology and the efficiencies that come with it via a proven format from a leading shipbuilder.
Inputs From Operators
The design team at Damen sought input from experienced operators in the sector and its own repair yards, which have been maintaining dredgers for many years, and its dredging mission equipment production subsidiary. These, together with its ship design and building capabilities, makes the company a one-stop-shop for all things dredging. As a result, while the new design is similar in size to its twentieth-century equivalents, the MAD 3500 is an entirely new class that is well ahead, both in the quantity of product it can carry (20% more) and operational costs per tonne.
According to the company, these attributes have been achieved not only by the latest propulsion systems delivering greater fuel economy but also by their ability to conduct operations while running on a single engine. It is also designed to operate 24/7 with just nine crew. At any one time, dredging can occur with only two personnel on the bridge plus an engineer on duty. Unloading the entire vessel can be achieved in just two to three hours and is fully automated.
Operability is maximised with ease of maintenance designed into the vessel from the earliest stages. This is achieved partly through modular systems that allow faulty components to be swapped out for new ones while the defective unit is sent away for testing and repair. This, in turn, is supported and enhanced by using its Triton remote monitoring and analysis system that enables continuous optimisation and pre-emptive maintenance. It is achieved using ship-wide sensors to deliver operational data to both the bridge and managers onshore for real-time analysis.
Building Hanson Thames
TheHanson Thames began her build at Damen Shipyards Galati at the end of 2019. While based on the original MAD 3500 design, she benefited from the experience gained from an earlier build and had some adjustments to meet her particular operational requirements. Key technologies onboard the MAD 3500 include the modular screening tower, which allows material brought up from the seabed to be sorted as it comes aboard rather than once it reaches land. This enables it to retain only the grades that are in demand while returning the rest to the seabed. This makes it yet more efficient and profitable.
Another is the application of the Damen Offshore Bow. This fully encloses the foredeck, protecting equipment and cargo and delivering excellent seakeeping. The mooring system also sets a new standard. It is designed around flow lines to ensure safe and efficient mooring at all times, and the addition of telescopic spud poles enables the MAD 3500 to hold position without the use of lines or the need for constant adjustment.