
In today's automotive landscape, the practice of remanufacturing engine parts is swiftly gaining momentum, hailed for its dual benefits of environmental sustainability and economic efficiency. By refurbishing and reconditioning engine components, remanufacturing significantly extends their lifecycle, presenting a compelling solution that aligns with both ecological and financial objectives.
Remanufacturing engines is not just a process for Cummins; it's an art form, as every component is carefully inspected, cleaned, and tested to ensure it meets its rigorous standards for performance and durability.
ReCon, also known as remanufactured parts, are components sourced from Cummins engines that undergo a rigorous process involving disassembly, thorough inspection, meticulous cleaning, precise calibration, and comprehensive testing to ensure they match the performance standards of brand-new parts. Following this meticulous process, ReCon parts are made available for individual purchase or utilised in the assembly of ReCon engines.
Engines approaching the end of their lifespan undergo a complete disassembly process to prepare each component for remanufacturing. Advanced cleaning technologies, such as laser cleaning for rust removal and environmentally friendly enzyme cleaning for grease and oil, are employed to ensure thorough cleansing. Following cleaning, each part undergoes a meticulous inspection using techniques like ultrasonic inspection to verify that it meets the original factory specifications. Any upgrades or modifications made to the original design are incorporated during the remanufacturing process to enhance performance and durability.
The engine maker has continually enhanced its remanufacturing process over several decades, integrating cutting-edge tools and technologies such as additive manufacturing (commonly known as 3D printing), collaborative robots (referred to as 'cobots'), laser cleaning, and more. Unlike traditional engine shops that simply replace faulty parts, the company’s remanufacturing process involves a thorough examination, cleaning, and testing of each component to ensure optimal performance. Any enhancements or upgrades made to the original design are seamlessly incorporated during the remanufacturing process, ensuring that customers receive top-notch quality and reliability.
Components Eligible For Remanufacturing
According to the engine manufacturer, up to 85% of an engine's components can undergo the remanufacturing process, ensuring extended lifespan and optimal performance. From turbochargers and fuel pumps to injectors, actuators, and cylinder heads, a wide array of parts can be remanufactured to stringent standards. However, parts with predetermined lifespans or those challenging to detect fatigue are excluded from remanufacturing and are replaced with new or ReCon alternatives.
In Cummins' state-of-the-art remanufacturing facilities, each of its ReCon engine undergoes a comprehensive process. This includes meticulous disassembly, thorough inspection, advanced cleaning techniques, rigorous testing, precise painting, and meticulous reassembly. All these processes adhere strictly to ISO 9001 standards, ensuring unparalleled quality and reliability. The result? Newly built engines equipped with the latest ReCon or new parts warranty, boasting zero hours/miles and restored to a 'like new' condition, ready to deliver optimal performance on the road.
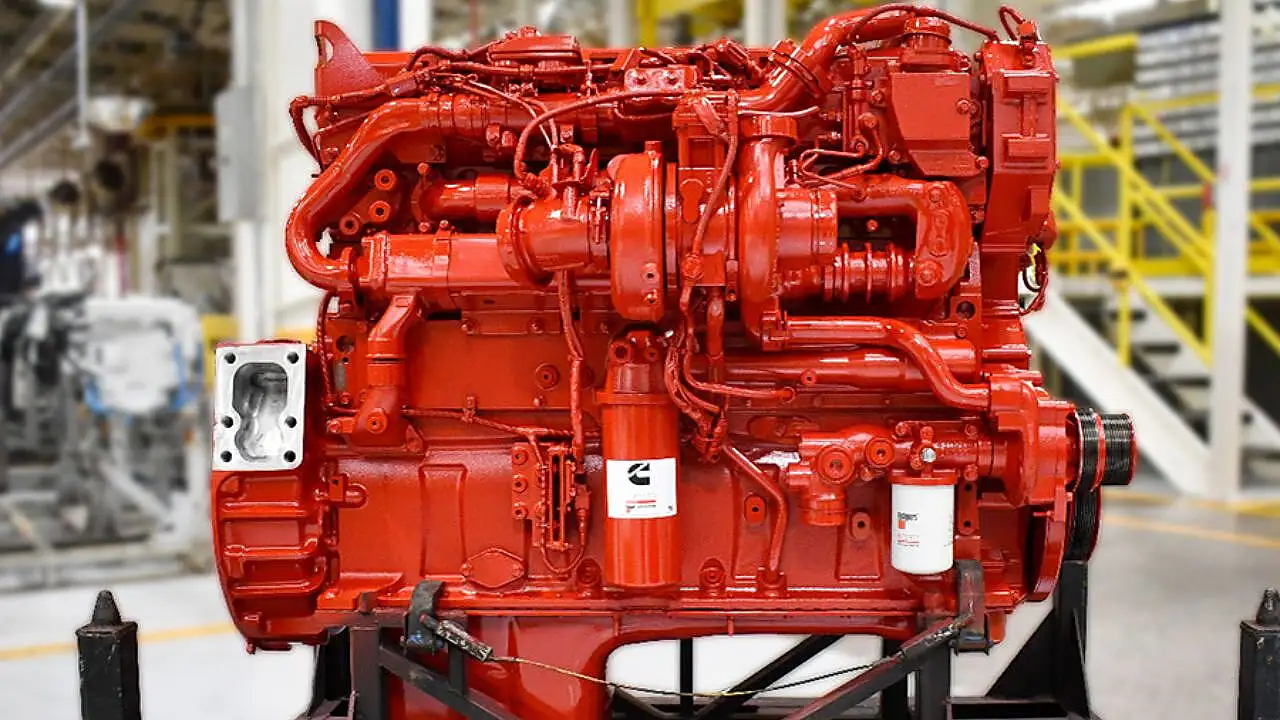
Benefits Of Remanufactured Parts
But remanufacturing at Cummins goes beyond just restoring engines; it's about sustainability and environmental responsibility.
Remanufacturing plays a pivotal role in advancing the circular economy, championing material reuse, and mitigating environmental concerns such as climate change. The company is focussed on its circular ethos, prioritising the reuse, recycling, and remanufacturing of materials as part of its sustainability strategy, PLANET 2050. It has set ambitious goals to reduce its ecological footprint across various aspects of its operations.
To mitigate its impact on climate change, the engine maker aims to cut absolute greenhouse gas (GHG) emissions from its facilities and operations by 50%. Additionally, the company strives to reduce scope 3 absolute lifetime GHG emissions from newly sold products by 25% and collaborates with customers to slash scope 3 GHG emissions from products in the field by a staggering 55 million metric tonne.
Efforts to minimise air pollution include a 50% reduction in volatile organic compounds emissions from paint and coating operations. Embracing a circular economy approach, the firm plans to create a circular lifecycle plan for every part, promoting the principles of 'use less, use better, use again.'
Waste reduction is a key focus area, as it aims to generate 25% less waste in facilities and operations as a percentage of revenue. The company also aims to reusing or responsibly recycling 100% of packaging plastics and eliminating single-use plastics in dining facilities, employee amenities, and events. Furthermore, it is dedicated to conserving water resources and plans to reduce absolute water consumption in its facilities and operations by 30%.
Here's why selecting ReCon engines and parts makes both economic and ecological sense:
Cost-Effective Reliability: Remanufactured engines offer the same reliability and efficiency as new ones but often at a lower cost. This affordability stems from the reduced energy, material, and water consumption during the remanufacturing process. The ReCon parts and engines not only feature the latest engineering updates but also come with the assurance of a Cummins warranty.
Streamlined Efficiency: Opting for ReCon engines and parts can expedite delivery times and streamline operations compared to the prolonged process of disassembling, diagnosing, and repairing existing engines. This efficiency ensures minimal downtime and optimal performance for your fleet or machinery.
Sustainability: By choosing remanufactured parts, the users contribute to sustainability efforts by reducing waste and lessening the demand for new raw materials. Each ReCon component selected supports a greener, more sustainable future for generations to come.
Positive Impact: Remanufactured products not only benefit the environment but also bolster industry dynamics and local communities. By reusing existing materials, remanufacturing reduces the need for resource-intensive raw material extraction and waste disposal processes. Moreover, remanufacturing operations often create local job opportunities, empowering skilled technicians to meticulously restore parts to their original specifications while fostering economic growth in the community.
Challenges
One of the primary hurdles in the realm of remanufacturing lies in aligning with suppliers. Designing parts or engines conducive to remanufacturing necessitates close collaboration with suppliers, not solely from a manufacturing standpoint but also to ensure shared sustainability objectives. It's imperative that suppliers grasp and endorse the principles of remanufacturing to establish a symbiotic cycle that supports environmental conservation while meeting customer demands.
Historically, apprehensions surrounding remanufactured products have lingered, often stemming from misconceptions regarding quality and durability. However, as the global supply chain landscape is anticipated to contract in the coming years, remanufactured goods emerge as a viable solution to potential supply chain disruptions.
At the forefront of this transition towards remanufacturing stands Cummins ReCon business. ReCon engines and parts showcase the fusion of reliability and cost-effectiveness, embodying a broader vision for a sustainable future. While challenges persist, particularly in supplier alignment and broader industry acceptance, the undeniable benefits of remanufacturing underscore its increasingly pivotal role in shaping an eco-friendly, economically resilient manufacturing landscape.
Cummins ReCon is not just about engines; it's about trust, quality, and a commitment to excellence. With Cummins ReCon, you're not just getting an engine; you're getting a masterpiece of remanufacturing craftsmanship.
Also Read:
Cummins' Innovation In Hydrogen & Natural Gas Fuel Delivery Systems