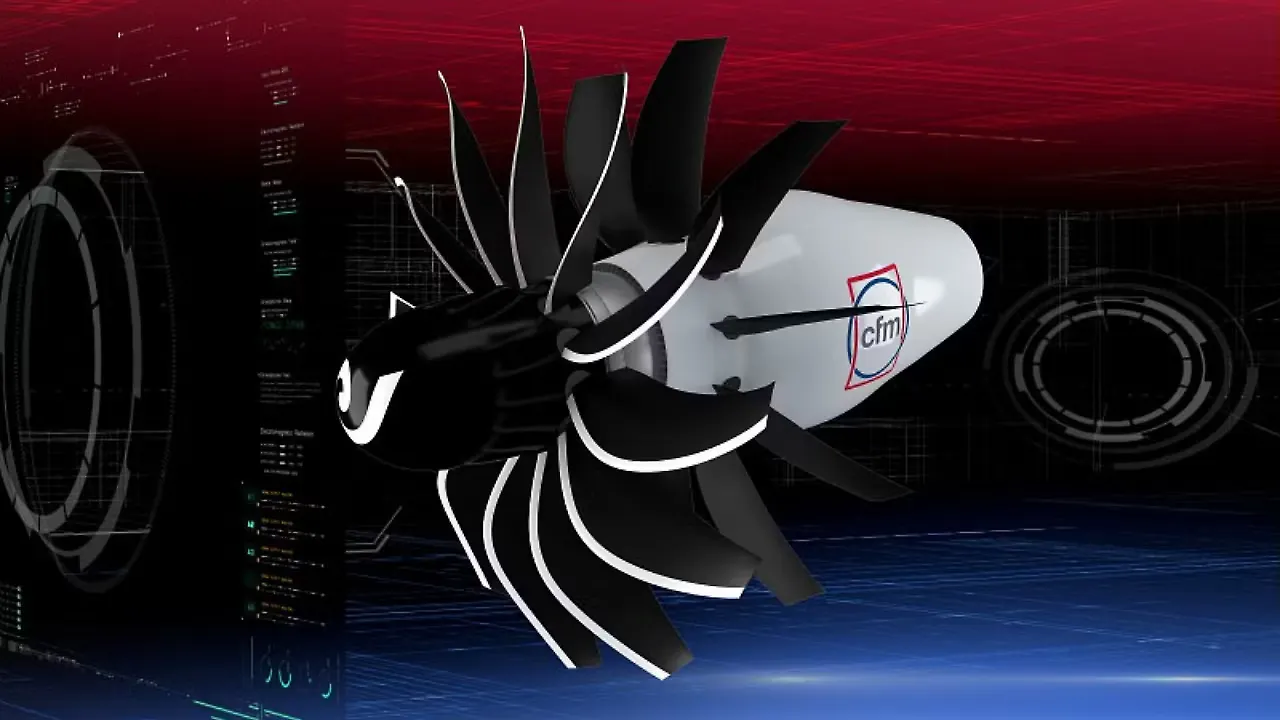
To deliver on the promise of a sustainable future for commercial aviation, CFM International (CFMI) has launched its Revolutionary Innovation for Sustainable Engines (RISE) programme, which aims to deliver dramatic improvements in fuel consumption and CO2 emissions by up to 20% against the latest generation of aero engines in commercial service today.
John Slattery, President & CEO, GE Aviation, said, 'Together, through the RISE technology demonstration programme, we are reinventing the future of flight, bringing an advanced suite of revolutionary technologies to market that will take the next generation of single-aisle aircraft to a new level of fuel efficiency and reduced emissions.'
Future ready
New-generation aero engines stemming from the RISE programme could enter service as early as the mid-2030s. Olivier Andriès, CEO, Safran, said, 'We have to act now to accelerate our efforts to reduce our impact on the environment. Since the early 1970s, breakthrough engine efficiency and reliability have been the hallmark of our historic partnership, and our LEAP engine already reduces emissions by 15% compared to previous generation engines.'
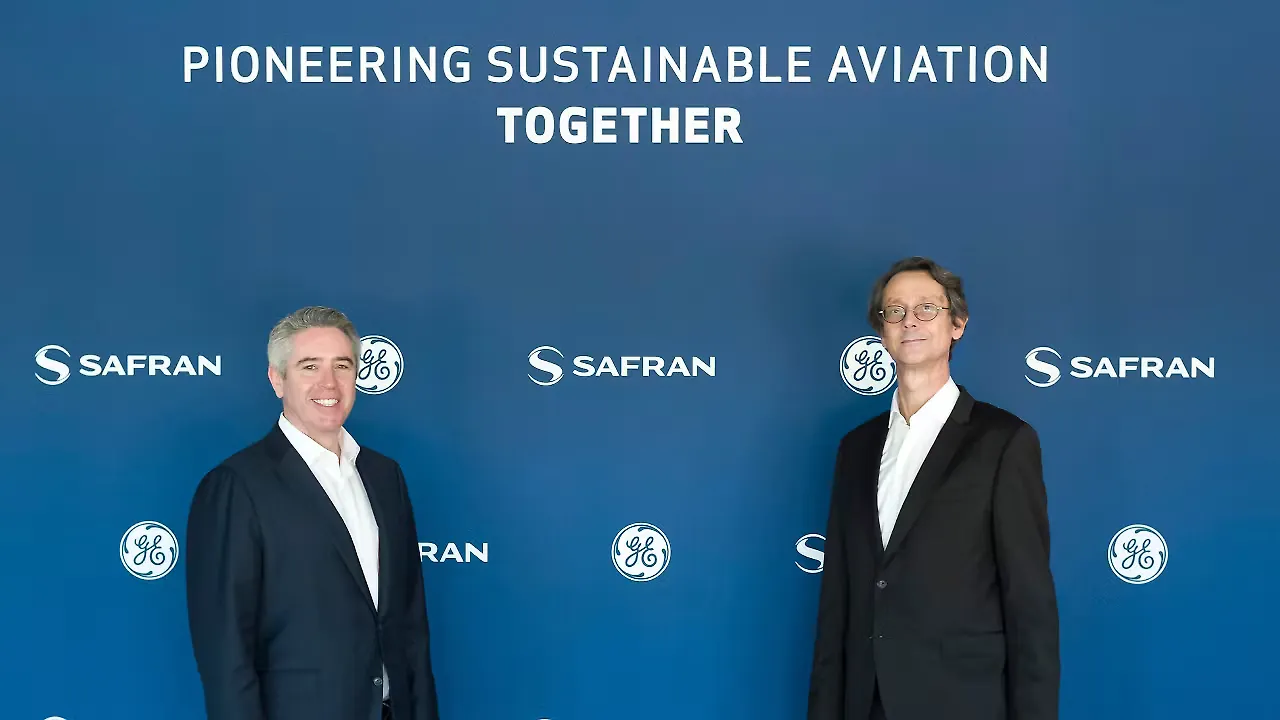
The RISE programme will use a revolutionary open fan architecture to serve as the foundation for the next generation of CFM engines. CFM's current generation LEAP engine is its fastest-selling powerplant, with approximately 4,500 delivered in the past five years. CFMI is a 50:50 joint venture between aero-engine manufacturers GE Aviation and Safran, who have also decided to extend the partnership, which started in 1974, till 2050.
Disruptive innovation
On the CFM RISE programme, Travis Harper, Product Manager, GE, said, 'We work together to define our vision, set our future product requirements and execute our efforts to develop an engine that will best support the future of flight as we see it. The area we believe will yield the most benefit and plan to demonstrate in the coming years is the open-fan concept that would deliver a very significant fuel burn and CO2 emissions improvement.'
Modern turbofan engines that power commercial jetliners today are known as 'High Bypass' turbofans. In turbofan engines, air captured at the engine inlet passes into the core compressor, following which it is mixed with fuel in the burner and ignited. The superheated gases coming out of the exhaust provide thrust. In high bypass turbofans, much of the air goes around the core or 'bypasses' it. But this air has already been accelerated by the engine inlet fan blades and thus provides additional thrust without a large increase in fuel consumption. The bypass ratio describes the relationship between the thrust the rotor (fan) generates and how much energy it takes to drive the rotor. According to CFM, its engines have grown from an initial bypass ratio of 5:1 in the eighties to a bypass ratio of 11:1 for today's LEAP engine. An open rotor fan could achieve a bypass ratio above 70:1. An open fan architecture doesn't have a case covering the fan at the front, as seen in conventional engines, hence the term 'open'.
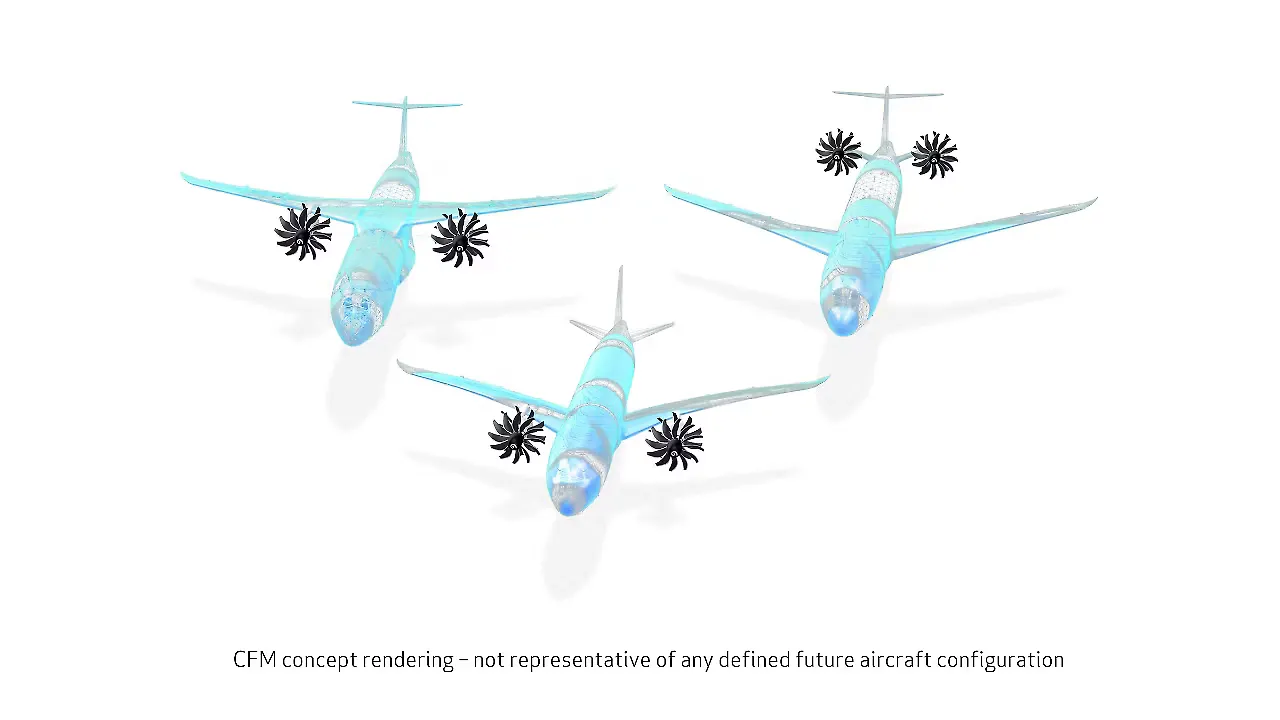
The open fan engines could either be placed under the wings in either a low- or high wing configuration or at the back of the aircraft. Research done on new generation open fan architecture by GE Aviation and Safran has shown that they will power future commercial jetliners to speeds up to Mach 0.8 (similar to current jetliners) but with far reduced emission and noise levels with significantly improved fuel consumption.
Ahead of the curve
CFM is now making significant investments to support the development of advanced foundational technologies for the RISE programme. It has established a comprehensive roadmap with more than 300 separate component, module, and full engine builds to test and mature technologies.
A joint GE/Safran engineering team is already laying out a comprehensive technology roadmap for developing composite fan blades, heat-resistant metal alloys, Ceramic Matrix Composites (CMC), hybrid-electric capability, and additive manufacturing on the planned demonstrator engine.
Several rig tests have already been completed and are already delivering promising results. CFM says it will be ready for full demonstrator engine ground test and flight tests by the middle of this decade. CFM also says that it is on track to be the first to introduce hybrid-electric propulsion in the single-aisle jetliner segment due to the RISE programme. The integration of fuel-powered turbines with electrical-powered motors results in hybrid-electric powerplants.
Materials matter
CMCs will play a vital role in the RISE programme and future aircraft engines as they can withstand temperatures beyond the melting point of many advanced metallic superalloys (up to 2,400 degrees Fahrenheit). It also offers significant weight advantages, being only one-third the weight of steel. The manufacture and production of CMCs in the large quantities needed for commercial aero-engine programmes is a closely guarded and highly proprietary process at GE Aviation. It takes a multistep and secret process to manufacture CMCs, where engineers first cover tiny silicon carbide fibres, which are five times thinner than human hair, with a special coating. These fibres are then embedded in a silicon carbide matrix for further processing. CMC technology took 30 years to develop at GE Research and GE's corporate labs. This breakthrough technology was pioneered inside the LEAP engine and is also being used on GE's latest GE9X engine, which will enter service on Boeing's 777X widebody jetliner.
The RISE team also has plans to use a special carbon fibre woven in three dimensions and injected with resin to build rotors as large as 13 feet in diameter. These composite blades do not require a life limit and hence reduce maintenance and replacement costs. GE has the distinction of being the only aero-engine manufacturer to have used carbon fibre engine blades, which first entered commercial service in 1995 on the GE90. The company has more than 140 million flight hours of experience with composite fan blades on the GE90, GEnx, LEAP, and GE9X engine programmes that all feature lightweight, highly efficient and durable fan blades.
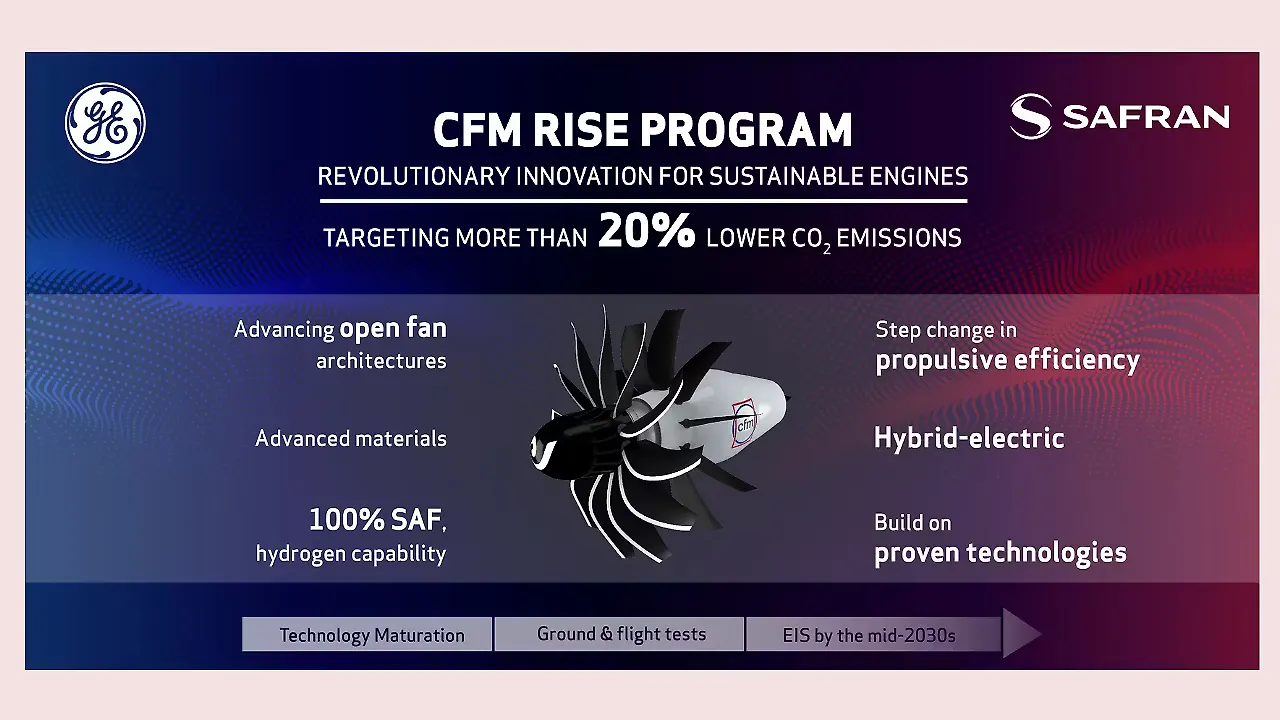
Towards sustainable future
The aviation industry is responsible for approximately 2% of all human-induced CO2 emissions (915 million tonne of CO2 in 2019). However, with aviation being the fastest growing mode of transport, aircraft traffic growth could triple carbon emissions by 2050 if future aircraft do not deliver reduced carbon production targets.
The CFM engine's fuel consumption and CO2 emissions have been reduced by approximately 40 % since the early eighties, compared to the engines they replaced. CFM's latest generation LEAP aero engine, which power jetliners such as the Airbus A220, A320 Family, Boeing 737 MAX Family and Commercial Aircraft Corporation of China (COMAC) C919, have delivered emissions reductions of 15% as compared to previous generation engines such as the CFM 56.
GE and Safran engineering teams will further explore the use of 100% Sustainable Aviation Fuels (SAF) and hydrogen to deliver on the RISE programme goals. Since 2006, CMF has performed extensive ground and flight testing on aircraft using SAF and airline customers have already flown hundreds of thousands of commercial flights with the currently approved 'drop-in' SAF blends. CFM is now working to take this to the next step to assess the certification of 100% renewable fuels for aircraft operating with certified blends of up to 50% renewable fuels. When industry certification for 100% SAF is obtained and supported by the worldwide availability of synthetic fuels, it will dramatically reduce CO2 emissions from the aviation industry.
Photo courtesy: CFM.