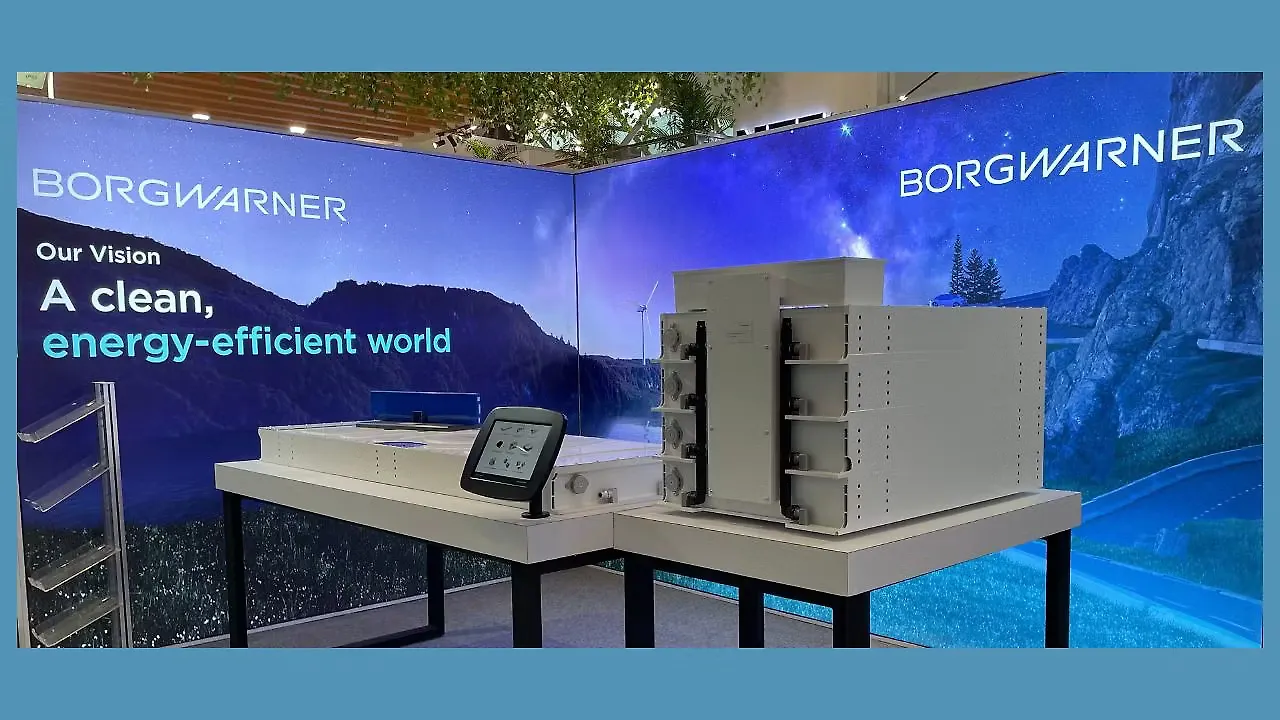
BorgWarner is set to expand its footprint in India’s electric vehicle market with the introduction of its latest LFP (Lithium Iron Phosphate) battery technology. In partnership with FinDreams Battery, a subsidiary of BYD – China, the company aims to leverage its expertise to deliver cost-effective and high-performance battery solutions, specifically tailored for India’s price-sensitive market.
Speaking to Mobility Outlook, Johannes Rossmanith, Director – Business Development, Drivetrain & Battery Systems, BorgWarner Akasol GmbH, highlighted the strategic move. “We have an exclusive agreement with FinDreams for LFP battery chemistry. We are the only non-OEM manufacturer granted access to their blade cell technology, allowing us to develop a modular battery platform for commercial vehicles, including buses and trucks,” he stated.
Since 2021, BorgWarner has been producing NMC-based batteries across Europe, North America, and South America, serving major customers in those regions. Now, with its LFP technology, the company is setting its sights on the Indian market—not just for commercial vehicles, but also for passenger cars.
Beyond battery production, BorgWarner is investing in in-house design, assembly, and battery management systems. “We have all the capabilities, including software development, except for the cell itself, which is sourced from FinDreams,” Rossmanith explained.
Blade Cell Technology
As BorgWarner expands its battery technology portfolio, its adoption of blade cell technology is set to bring significant advantages in energy density, heat management, and safety. Unlike conventional cylindrical cells, blade cells are elongated and designed with terminals on the smaller side, optimizing heat dissipation and enhancing overall durability.
“The internal stacking and jelly-rolling process within the cell improves heat distribution, resulting in better energy efficiency and a longer lifespan. Additionally, the blade cell's puncture resistance is superior—you can drive a nail through it, and nothing happens explained Rossmanith.
LFP battery chemistry is inherently safer due to its thermal stability, requiring less complex cooling and propagation protection compared to NMC (Nickel Manganese Cobalt) packs. This translates into lower production costs while maintaining high safety standards. 'Our NMC packs are equally safe, but they demand additional design efforts in cooling and protection. LFP’s natural safety gives it a cost advantage,' he added.
BorgWarner's blade cells, developed in partnership with FinDreams Battery, will be manufactured regionally, following a 'local-for-local' approach. 'The blade cells will come from China, but production will take place wherever we have customers. We are already manufacturing in Europe and North America, and as soon as we secure a viable programme in India, we will establish production there,' Rossmanith confirmed.
As BorgWarner gears up for the launch of its LFP battery technology, the company is laying the groundwork for its start of production in Europe by late 2026 or early 2027. Currently in the B-phase prototype stage, the batteries will undergo validation before moving into the final production phase.
“We haven't started supplying OEMs yet, but we are actively developing and refining our battery systems. Our goal is to have them ready for deployment by 2026-27,” Rossmanith said.
800V-Capable, Fast-Charging Battery Systems
BorgWarner's new LFP battery packs will offer approximately 100 kWh of energy and operate at a nominal 670V, with a voltage range between 550V and 800V. This high-voltage capability enhances efficiency and allows compatibility with modern electric vehicle platforms.
Charging speed is another key advantage. “Our systems support megawatt (MW) charging, depending on configuration. The industry standard for commercial vehicles today is a 20-80% charge in under 30 minutes, and our technology easily meets that requirement,” he explained.
Induction Charging: Not A Priority Yet
As the industry explores alternative charging solutions, some companies are investing in induction charging—similar to wireless phone charging, where vehicles charge simply by being within a short distance of a charging pad. However, BorgWarner currently does not see this as a major trend.
“Our batteries are compatible with induction charging, but we don’t integrate inductive charging technology into our packs. Induction charging systems would transfer energy to our batteries through the high-voltage connection, but for now, we see limited market adoption,” he stated.
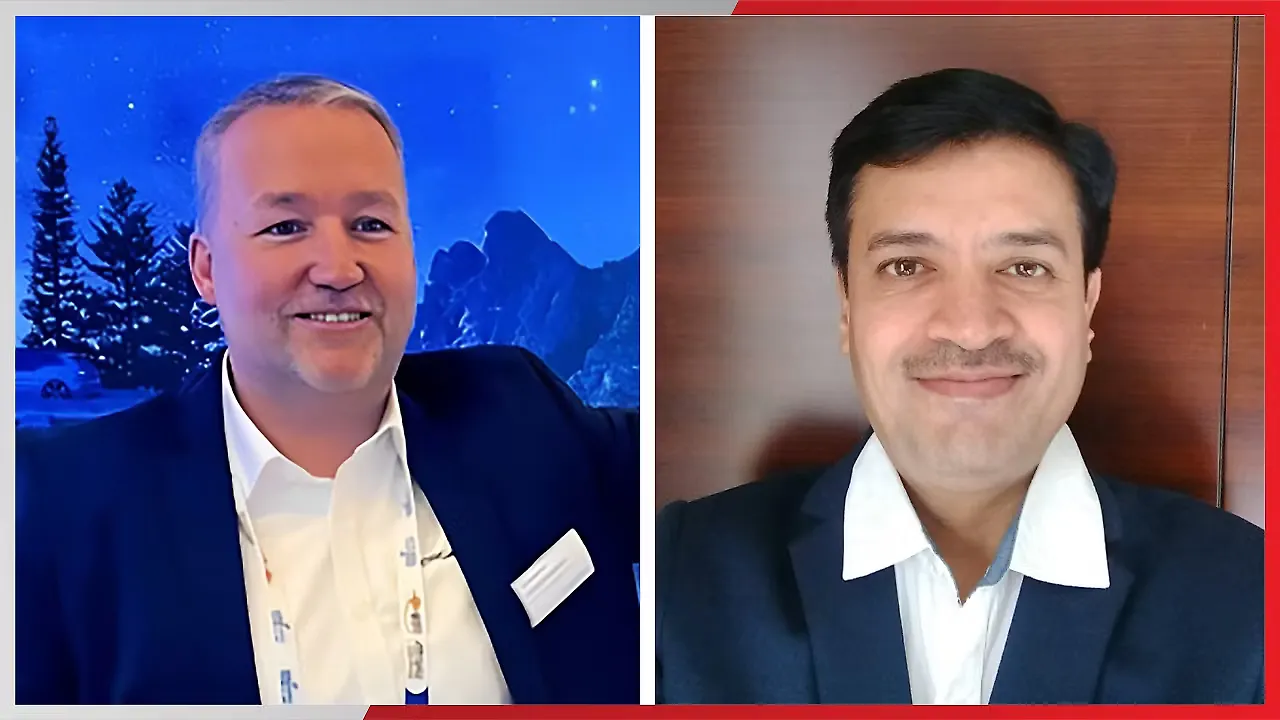
Expands Engineering Capabilities In India
BorgWarner is strengthening its presence in India with an expanded engineering centre in Bangalore, reinforcing its commitment to innovation and local market needs. The BorgWarner India Technical Centre now operates from a new 80,000-square-foot facility, featuring a dedicated 10,000-square-foot high-voltage lab space.
“We have always had a captive engineering centre in Bangalore, but two years ago, we moved to a larger facility and have been expanding ever since. Today, we have over 500 engineers supporting multiple product lines across various business units said Swaroop Sundararajan, Head of Engineering – Turbos & Thermal Technologies, BorgWarner India Technical Centre.”
The centre houses key divisions, including the Turbo & Thermal Technologies and PowerDrive Systems units. These teams work on system development, software and hardware engineering, as well as system and software testing, contributing to BorgWarner’s global innovation efforts.
As the Indian automotive market evolves, the company is increasingly aligning its engineering expertise with local customer demands. “We recognize the growing need to cater to India-specific projects, and our expanded footprint allows us to do just that,” Sundararajan added.
Thermal Management Solutions For EVs
As the global automotive industry transitions from internal combustion engines (ICE) to electric vehicles (EVs), BorgWarner is leveraging its expertise in thermal management to develop advanced cooling solutions for electrified platforms.
Sundararajan, highlighting the company’s growing focus on EV cooling technologies, said, “We already have global projects for our E-fan technology, primarily for commercial EVs, and we’re now exploring opportunities with Indian OEMs.” The E-fan, designed for power ranges between 10kW and 20kW, integrates an inverter, motor, and fan to efficiently cool critical EV components, including the battery system.
While cooling technologies differ between ICE and EVs, thermal management remains crucial for battery performance and longevity. Rossmanith explained the company’s battery cooling approach stating that “for our LFP battery packs, we use a water-glycol coolant running through integrated cooling channels in the base plate, where the battery cells are mounted. Unlike traditional chiller systems, this method ensures effective temperature regulation while maintaining efficiency.”
Driving Innovation
As India accelerates its shift towards electrification, BorgWarner’s Technical Centre in Bangalore is evolving into a hub for innovation, aligning global expertise with local market needs. With a strong focus on developing cost-effective solutions for India’s price-sensitive market, the centre is playing a key role in shaping the company’s EV technology roadmap.
Sundararajan said, “We recognize the growing need for India-specific innovation, which is why we have invested in both high-voltage and low-voltage labs. These facilities allow us to test and refine our products locally, ensuring they meet customer expectations,” he said. The centre follows a ‘local accountability and global strength’ approach—leveraging global expertise while being accountable to Indian customers.
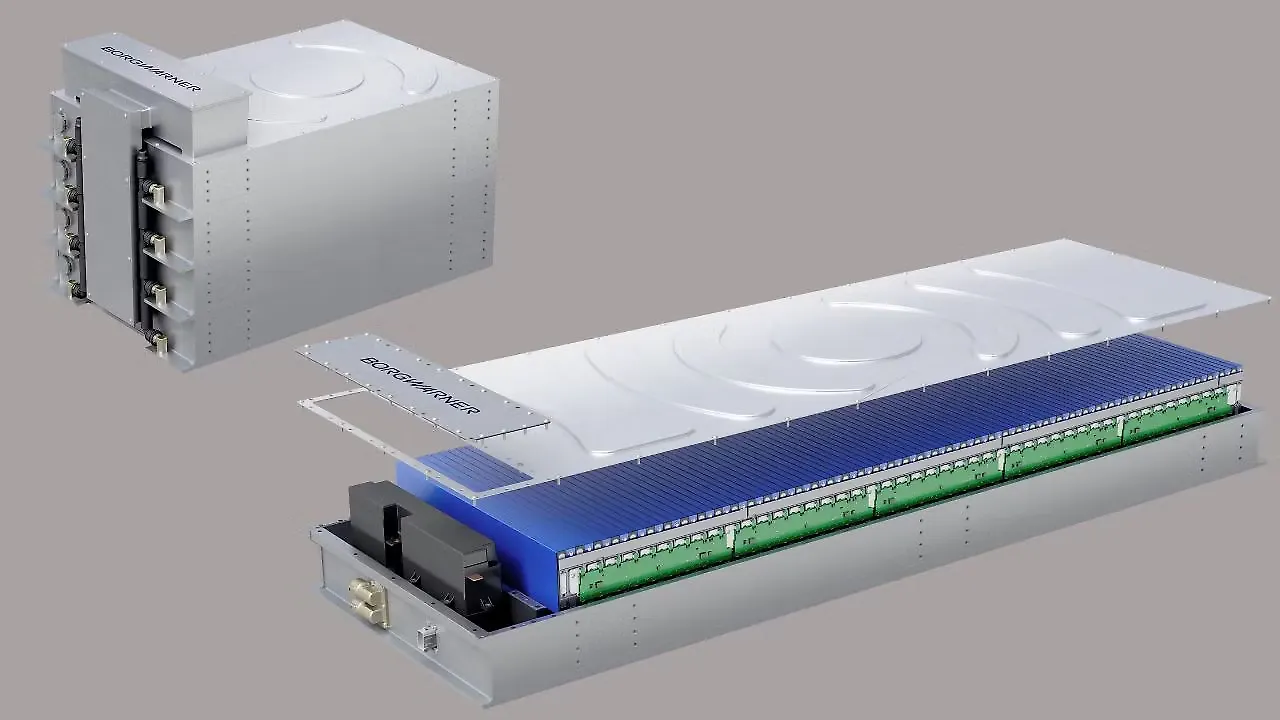
Advanced Testing for High-Voltage Solutions
The Bangalore facility houses a high-voltage test lab designed to validate various electrification products. “We have a dynamometer bench to support inverter development and a high-voltage system bench for testing coolant heaters,” Sundararajan explained. BorgWarner is already in discussions with Indian OEMs to integrate these testing capabilities into new product development.
Tailoring Electrification Solutions
While BorgWarner already has a comprehensive portfolio of EV solutions for both passenger and commercial vehicles, its focus in India is on affordability and efficiency. “Given the cost-conscious nature of the market, we are working closely with Indian customers to develop innovative, cost-effective solutions,” Sundararajan noted.
For example, BorgWarner’s high-voltage coolant heater—already in demand globally—is being adapted to a lower-cost, lower-power version for Indian customers. Similarly, the company is optimizing its E-fan technology, which currently supports up to 40kW, to better suit the Indian market’s demand for 10kW to 20kW solutions. “The challenge is to modify both software and hardware to create a more affordable and efficient solution, and our India Technical Centre is leading this effort,” he added.
By combining global technology with local adaptability, BorgWarner’s Bangalore centre is poised to become a centre of excellence, driving India’s EV transformation with innovative, market-ready solutions.
Also Read:
BorgWarner Secures High Voltage Coolant Heater Contracts Across Key Asian Markets