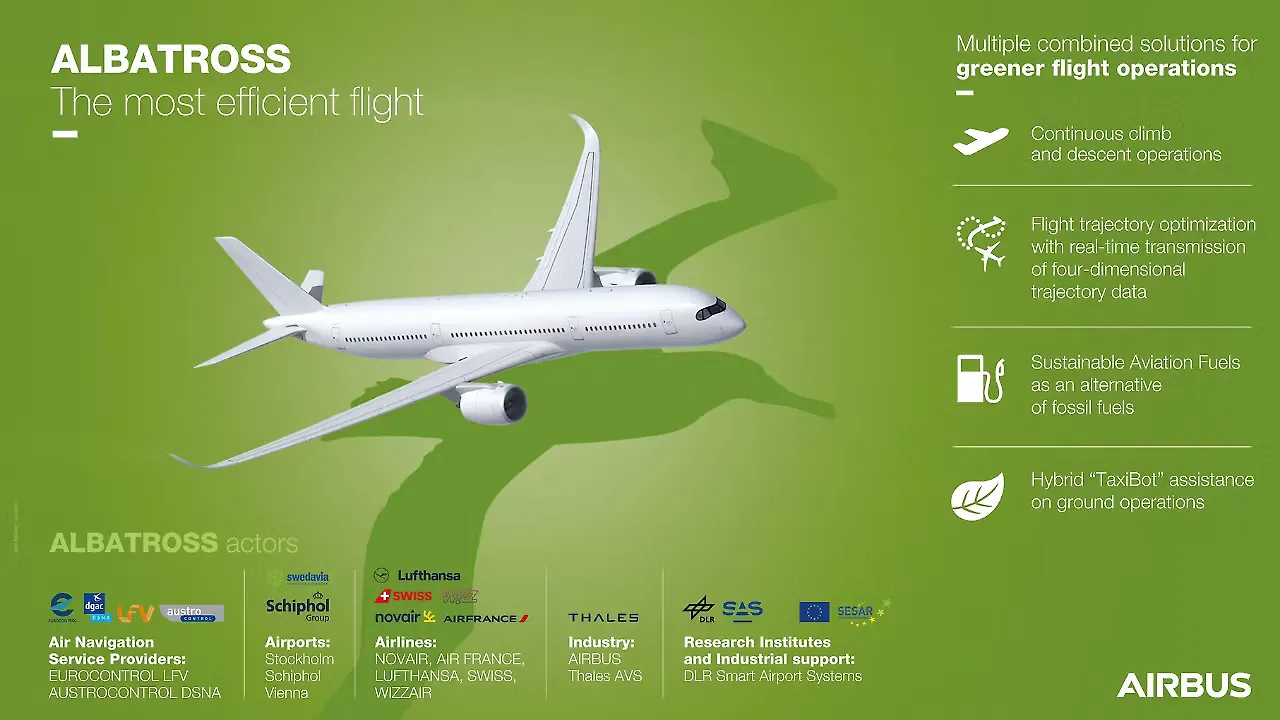
European airframer Airbus has brought to the fore its efforts towards sustainability and decarbonisation, its two pillars for a sustainable aerospace future. To drive the aviation industry path towards net-zero, the company brought together renowned aerospace experts, operators, thinkers, journalists, influencers, and policymakers worldwide to debate the necessary solutions required at the first-ever ‘Airbus Summit’ held recently.
At the conference, Airbus showcased some of its technology initiatives underway and announced several essential initiatives providing an insight into the future of sustainable travel. Decarbonisation will require deep collaboration, cross-sector partnerships, and new ways of thinking as the aviation industry charts a path to change the way we travel forever.
Micro-hybridization: The Next Frontier
One of the options being pursued by Airbus is the use of hybrid-electric power to benefit fixed-wing aircraft and helicopters. Such technologies could provide significant environmental and efficiency benefits as using a battery to provide energy instead of a thermal engine will negate the need to burn fossil fuels.
According to Airbus estimates, an aircraft’s environmental footprint could be reduced between 1% and 6% through micro-hybridisation. For helicopters, which are smaller, lighter and carry fewer passengers, this could grow up to 10%. A future alternative could be using battery-electric to power one engine on a twin-engine helicopter, which could deliver fuel-efficiency benefits ranging between 15% to 25%. There is, of course, the added operational and maintenance savings to be obtained as electrical systems are also likely to be easier to maintain than mechanical ones.
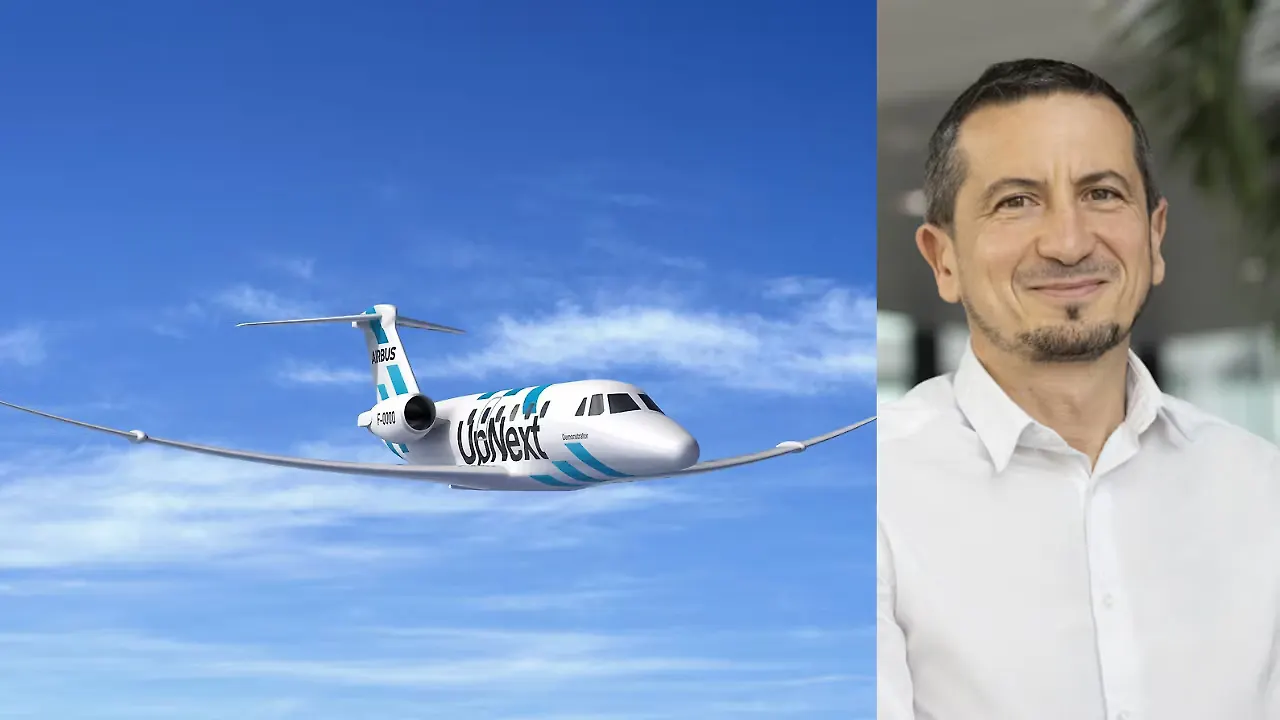
Airbus’ Head of Electrification, Karim Mokaddem, is an automotive industry veteran who believes the time is right for hybrid-electric innovation to make its mark on commercial aircraft operations and beyond. “Until we solve the energy-density challenge for propulsion, batteries can play more of a supporting role to reduce an aircraft’s CO₂ footprint. So instead of relying on thermal engines to completely power the aircraft, we could use small batteries to provide electrical power for some on-board systems, as well as to help relieve the engine in certain operations,” said Mokaddem.
Unlike the automotive sector, which has been powering ahead with battery-electric power in recent years, its leap to commercial aircraft has been beset by slower-than-expected progress. Of course, the scale of the challenge is far larger with the aviation industry, which faces stringent regulatory and safety standards. One of the key differences between the aviation and automotive sectors in the adoption of battery-electric power is that while cars recover energy when braking, airframers are yet to achieve the same balance between weight, energy, and power for a large commercial jetliner or regional transport aircraft, which carry tens to hundreds of passengers. Batteries also add weight to aircraft, an anathema to an industry where airframers and airline operators always seek to reduce weight.
According to Karim, for the aviation industry, the poor battery-specific energy compared to kerosene is a real showstopper as lithium-ion batteries cannot offer the same energy density compared to other forms of propulsion. He adds, however, that while current battery technology doesn’t have the right energy or power-to-weight ratio for intensive operations like take-off and cruise, electric power could be used in the future to assist the thermal engines during taxi and descent. In the near term, he says, battery-electric power could be more suited to powering non-propulsive functions, such as air conditioning and cabin pressurisation, communications, flight controls and landing gear.
Pioneering Efficient Flight
At the summit, the airframer announced the launch of ALBATROSS, a separate initiative from the Airbus “AlbatrossOne” wing project aimed at implementing the most efficient flight across a series of gate-to-gate live trials across Europe. The project will last for two years and is being conducted under the European Union’s Single European Sky ATM Research (SESAR) initiative. The programme's goal is to demonstrate how technical and operational innovations that have emerged in recent years can be combined and used together to reduce aviation’s environmental footprint in the short term.
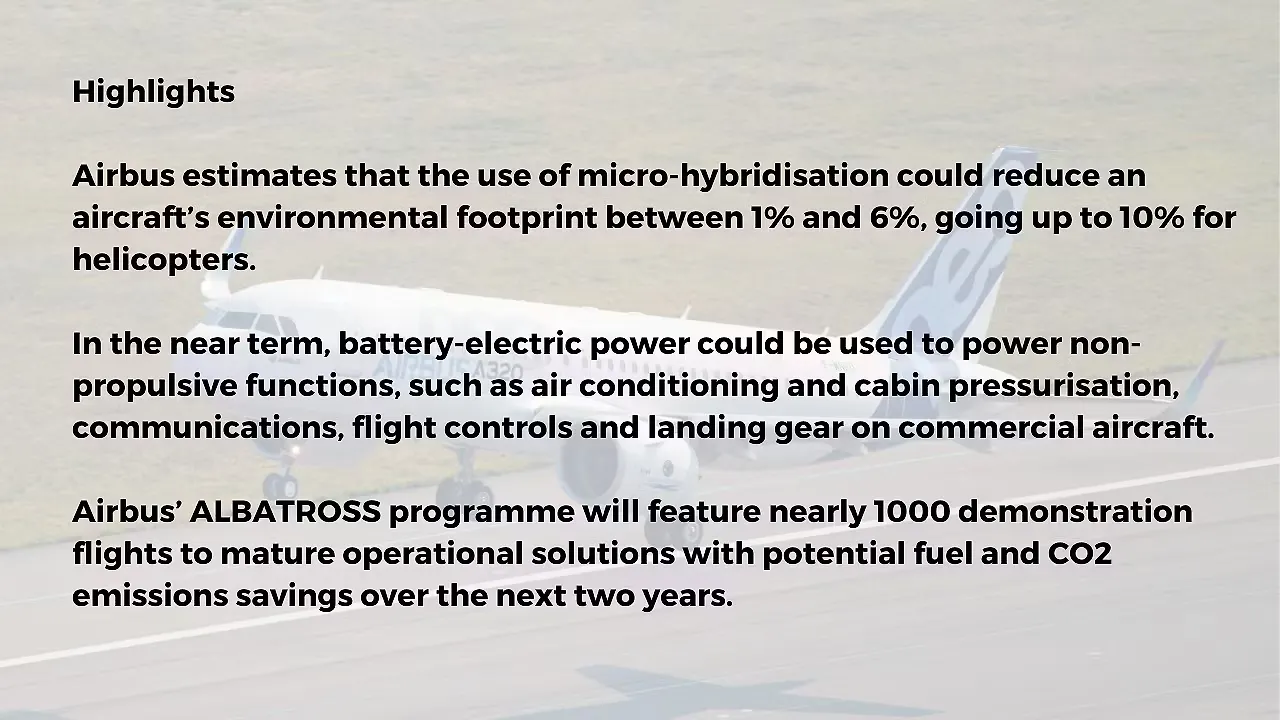
“All the combined solutions will allow us to extend the benefits expected while covering all the flight phases, including operations on the ground and during the flight, and addressing both operational and technological aspects of the aviation and Air Traffic Management (ATM), said Mattia Nurisso, Project Leader, and Thierry Harquin, Air Traffic Management (ATM) Cooperation Manager for Airbus.
According to Airbus, the first demonstration flight will take place this month, and approximately 1,000 flights are planned over two years to mature operational solutions with potential fuel and CO2 emissions savings.
Winging It
One of the most critical and closely guarded technologies in the aviation sector is related to wing design, and Airbus has launched an extra-performing wing demonstrator project to explore the future of wing design. Airbus will seek to accelerate and validate technologies to improve and optimise wing aerodynamics and performance for any future aircraft.
“Airbus’ extra-performing wing demonstrator is another example of Airbus’ novel technology-oriented solutions to decarbonise the aviation sector,” says Sabine Klauke, Airbus Chief Technical Officer. “Airbus is continuously investigating parallel and complementary solutions such as infrastructure, flight operations and aircraft structure. With this demonstrator, we will make significant strides in active control technology through research and applied testing of various technologies inspired by biomimicry.”
According to the airframer, a future extra-performing wing would significantly contribute to its decarbonisation roadmap by reducing CO₂ emissions and being compatible with any propulsion solution and aircraft configuration.
Airbus will use a Cessna Citation VII business jet platform as a scaled demonstrator to test the breakthrough wing technologies in representative flight conditions. The demonstrator programme will be managed within Airbus UpNext, the airframer’s wholly-owned subsidiary, which can build demonstrators at speed and scale, thereby fast-tracking future technologies.