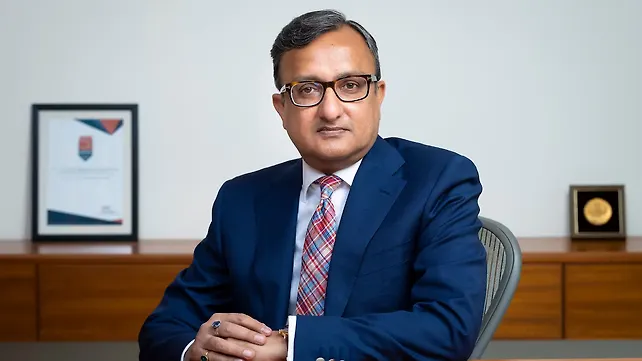
Rohit Saboo is an engineering graduate from the Birla Institute of Technology and holds an MBA from Rochester Institute of Technology, NY. He has also participated in the Senior Executive Program at Columbia University, NY. Saboo began his journey as Executive Assistant to the Chairman of CK Birla Group. He has worked in manufacturing, R&D and is now President and CEO of National Engineering Industries. Saboo believes that organisations need to be ready for numerous changes, transforming the industry as a whole to make India self-reliant and be the manufacturing hub for the globe.
Can you briefly tell us about your product offerings to automotive, railways and other industrial segments?
NBC Bearings has a wide range of bearings for various critical industries across automotive, railways and industrial segments like steel mills, power generation plants, cement, electric motor and domestic appliance manufacturers. Our product range includes ball bearings, taper roller bearings, cylindrical roller bearings, spherical roller bearings, axle boxes and our newly introduced needle bearings.
Apart from this, we are also making bearings for EVs and stepping our foot into aerospace and defence segments. For automotive, we supply our products to all major domestic and international automotive manufacturers and the railway product to Indian Railways and other international public and private railways.
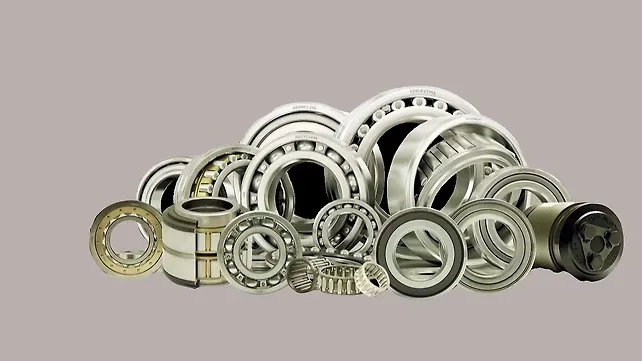
Do you see scope to enter the aviation sector? If so, please brief us about your plans.
Majority of bearings for the aviation sector are being imported currently. With the current focus on “Atmanirbhar Bharat”, we see this as a good opportunity to enter this segment. We are discussing with various aviation customers and finding that there is huge potential for a domestic player, who can strategically partner with them right from drawing board to manufacturing.
Bearings being a critical safety precision component, we are working on expanding our portfolio in a systematic manner. We are working with prominent academic institutes, national labs, domestic and international players to develop precision products for this segment. Our subsidiary in Europe, Kinex Bearings, has been active in this segment, which gives us a good kick-start for our plans in India. We plan to have bearings for this segment from FY22.
The automotive industry had a negative growth of 13.6% in FY21. How was it for NEI?
Even before the pandemic, the automotive industry was going through a tough time, and then with COVID-19, everything got worse. For the last 75 years, the company has been witnessing various social, political, economic and policy changes within the country, and NEI has always been able to keep up the pace. The year 2020, however, was very challenging. We registered zero sales during the two lockdown months, and business only picked up bit-by-bit post the unlock phases. Overall, we did better for FY21 than the industry and managed to pull our sales in the last two quarters.
Recovery has been happening steadily, but with the new strains, we have seen another wave of COVID-19 spreading fast and destabilising the country’s growth in the past few months. So, it comes as no shock that the recovery graph will be up and down before settling on a steady course and going upwards.
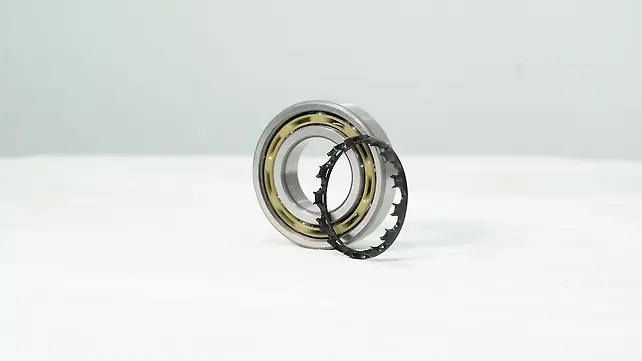
Which segment fared better in FY21 and why?
We saw V-shaped recovery in most segments we operate in, but the agri/tractor segment did exceptionally well. The sales in this segment have grown significantly during the last year. The demand was due to factors like better monsoon, easy finance availability and increased MSPs. We see the sign of recovery in CV market as well.
In the automotive segment, proliferation of EVs is expected to hamper friction reduction parts/systems, including bearings. How do you see this influence NEI and what are your thoughts on managing the emerging situation?
India cannot afford to miss out on the EV evolution, as the automotive sector is one of the largest contributors to the national GDP. Recent policies by the government resonate with the same sentiment. The Scrappage Policy or Faster Adoption and Manufacturing of (Hybrid &) Electric Vehicles in India (FAME) Phase 2, all promote and encourage the growth of EVs within the Indian automotive sector.
At NBC Bearings, we have designed & developed bearings for EV motors and transmission and already supplying to few partners. We also have developed and validated our indigenously developed ‘sensorised’ bearings for EVs and would be launching in the coming months of this financial year.
The automotive space forms about 65-70% of our total revenue. However, the contribution from EV business to total revenues currently stands at just around 1%, as the segment itself is at a very introductory stage of adoption. It will gradually evolve, and although the number of bearings used in this segment is less, the value of these bearings is significantly higher. This is an opportunity for us to enter new international markets.
Can you update on each of your manufacturing facilities?
We have five manufacturing facilities, which are located in Jaipur, Newai, Manesar and Vadodara. These factories manufacture over 200 million bearings each year offered in more than 2,300 variants. Recently, our 75-year-old Jaipur plant was awarded the coveted IGBC Green Factory Building Platinum Certification. Earlier in 2016, our Gujarat plant had also received Platinum Certification by IGBC.
We believe that continuous efforts need to be made at the factories to adopt the latest sustainability methods both in building and manufacturing. Water and energy being the most critical resources, our continued focus is on implementing efficient measures like utilising solar power, rainwater harvesting, on-site water treatment and replacing old equipment with more energy-efficient machines and technology. Due to rainwater harvesting, we also have been able to save more than six million litres of water.
We are continually evolving, trying to find agile and smarter ways to ramp up our production and offer value to our customers.
Can you elaborate on your JV with Amsted Seals? To what extent this JV will fetch new businesses to NEI from the railways segment?
Our joint venture with Amsted Seals is a significant step towards diversifying our product area and offering complementary products to our customers in railways. We have had a very long association with Amsted Rail that dates back to more than 35 years, and this joint venture is a testament to the same. I have no doubt the JV will be a big step towards supporting the vision of self-reliant India to set up best-in-class manufacturing infrastructure in the country.
NEI and Amsted Seals will develop a greenfield project located in Solitaire Industrial Park Bagru, Jaipur, Rajasthan. The JV entity will market its products with the brand name ‘NBC-Brenco’. We also plan to add automotive seals and products with metal fabrication in the future.
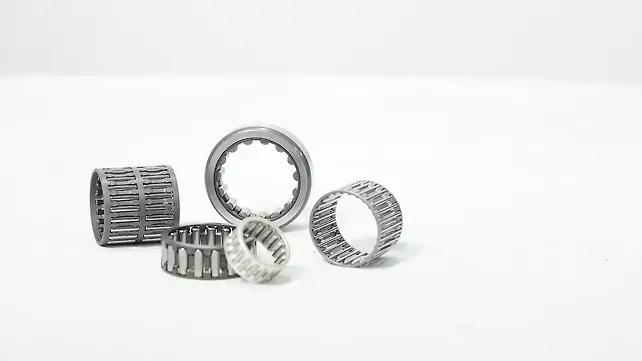
Do you see scope for extending the industrial segment offerings to customers in maritime?
Currently, for us, the demand from the maritime segment is not substantial. They need special material, and the volumes are low. Presently, we are not considering this, but we keep evaluating new segments to analyse viability.
What is the revenue breakup amongst automotive, industrial and railways?
For us, automotive is the biggest segment, which accounts for almost 60% of our revenues. Railways contribute around 25% of our revenue, while industrial segment accounts for 15%.
We are keeping pace with the developments in the automotive segment and expect it to grow steadily. One segment that we are bullish about is the industrial segment, where there is much scope for growth as the market is huge. We will put special efforts to grow our business in this segment in the coming future. Apart from this, although at very initial stages, the aerospace segment looks promising for the long run.
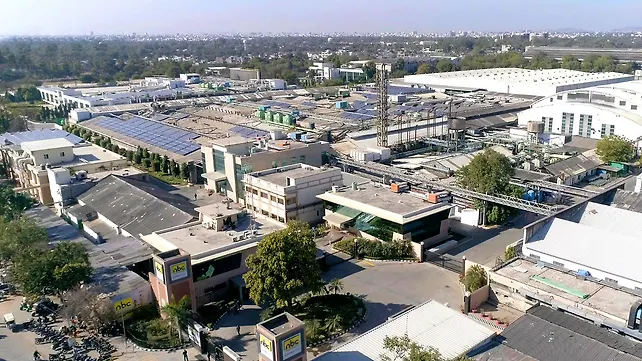
What percentage of revenue comes from the aftermarket? What are the challenges you face in this space, and how do you manage them?
At present, the automotive/industrial aftermarket accounts for around 20% of our business. It is a very dynamic segment, where we face competition from lost cost bearings, as it is a very cost-sensitive segment. Another issue plaguing this segment is duplicate/fake bearings. The spurious bearings are not suitable for the manufacturers and the end-user, as the quality is compromised. Lately, OEMs are also pushing the aftermarket spares directly, which is a sizeable market.
Can you tell us about your long term plans?
At the moment, our major focus is on investing in R&D, quality of products, people, and technology. We have chalked out our growth plans both organically and inorganically. Organically, we will keep working towards expanding our portfolio based on the evolving landscape of the industries/ sectors and, of course, the needs of our customers.
This year, we have invested in new lines to manufacture needle bearings – a requirement from our customers. We will also be introducing more bearings for EVs and smart bearings, and our industrial range of bearings is being enhanced with spherical and cylindrical bearings.
On top of that, we are actively exploring aerospace, defence, space exploration and other sectors to grow. Apart from the activities we are doing in India, we will continue to expand our presence in international markets. We will also continue to look for expansion opportunities to fuel our growth and will aim to fully digitise our manufacturing and non-manufacturing operations in the coming years.