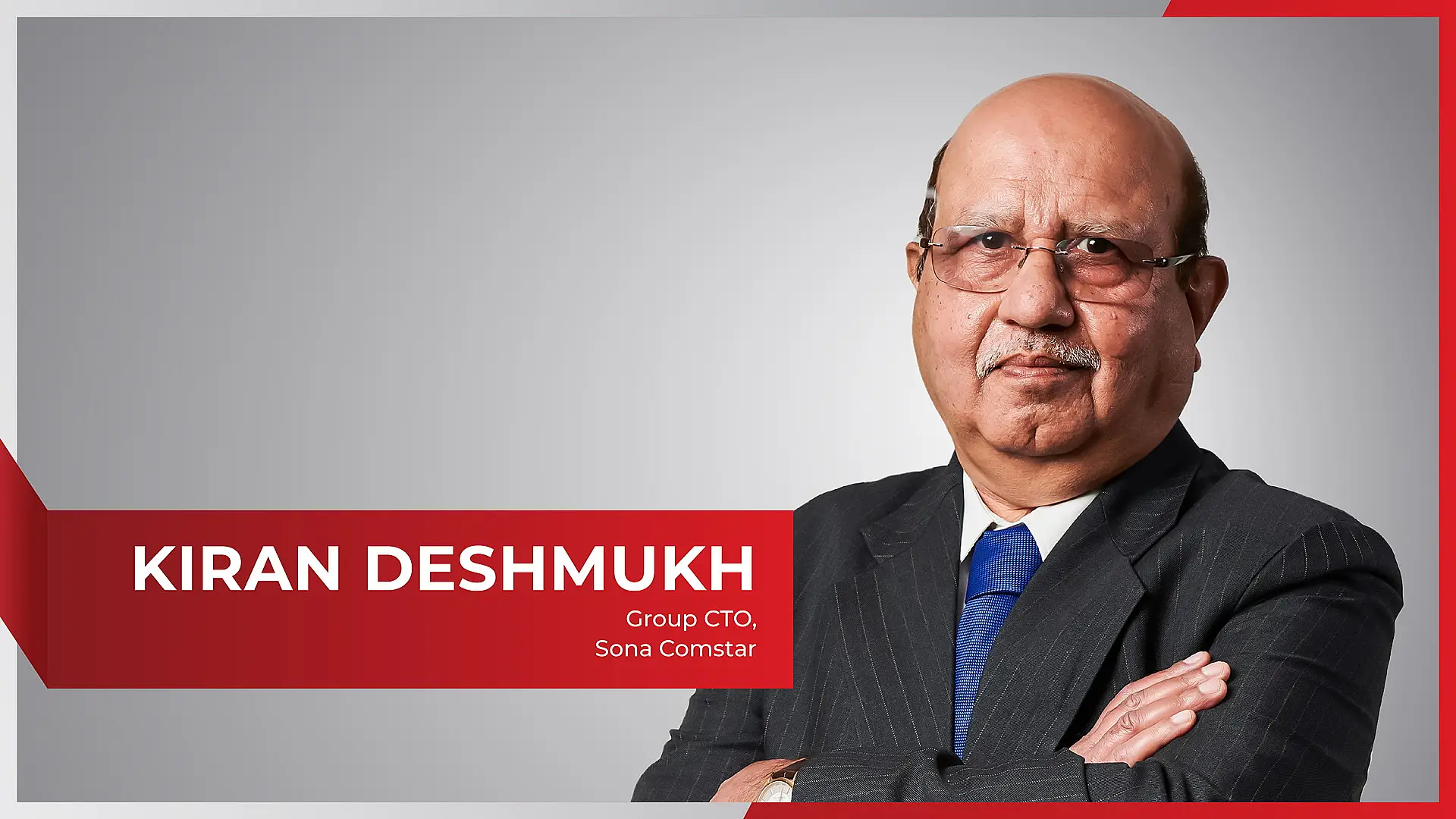
Kiran Deshmukh is the Group Chief Technology Officer of Sona Comstar. He holds a bachelor’s degree in technology in metallurgical engineering from the Indian Institute of Technology, Bombay. Deshmukh has significant experience in automotive components manufacturing and has worked in the areas of, among others, manufacturing, process control and design. He is responsible for steering the development of new technologies, establishing technology partnerships, and building competencies in manufacturing excellence at Sona Comstar.
What are the latest technological offerings from Sona Comstar?
We have a couple of technologies, including a ‘switch reluctance’ motor for high-capacity applications, electronic locking differential assembly and single module radar system for in-cabin monitoring.
Can you explain the uniqueness of the motor technology?
We have been looking at motors that do not use magnets with rare-earth materials, of which over 90% come from China. About 75% of the high-performance magnets also come from the country. We wanted to be free of this supply chain issue. Magnets, especially for high-performance motors, constitute 25-45% of the bill of material cost.
While looking to overcome this issue, the idea to look at motors without magnets emerged. We partnered with the IRP Nexus group and began some projects. There are technological challenges while developing motors without magnets to get the right torque and control noise and vibrations. The development continues.
The motor we displayed at the Auto Expo recently was developed in partnership with the Canadian start-up Enedym. It is a ‘switch reluctance’ motor that does not require any magnets.
This technology has been prevalent for quite some time. What is new now?
This technology has been in vogue for many decades. However, these could not be deployed in mobility applications due to inherent issues like noise and vibrations because of how the flux is managed. The stator has coils that induce magnetism into the rotor. Based on the combination of the poles on the stator and the rotor, the rotor gets attracted and rotates. When the polarity is switched, it continues to rotate.
Is it something like magnetic levitation?
Yes, it is. In the past, it wasn’t easy to switch poles quickly. But, thanks to the development in electronics, software and hardware algorithm, the team from McMaster University cracked the issue. As a result, the motor is silent and there is no vibration because the switching happens inside the controller that is powered by the Metal-Oxide-Semiconductor Field-Effect Transistor (MOSFET). Yet another key advantage is that it is easy to manufacture, as the motor does not have magnets.
You currently have motors operating between 48V to 96V. Is it possible to enhance the operating voltage?
The motors can reach an operating voltage of up to 800, and there is no limit to generating the power. The dimensions can be managed based on the space available in the vehicle.
What are the other advantages?
In conventional motors with magnets, if the temperature crosses Curie temperature, the magnets become non-magnetic. Typically rare earth magnets do not have higher Curie temperatures, and if the motor temperature shoots beyond the point, they become demagnetised. Therefore, all the motors (with magnets) have temperature sensors to derate them if the temperature is closer to the Curie temperature. To manage these issues, the motor will be made bigger or supported with cooling systems.
For switch reluctance motors, there is no risk of Curie temperature. The cooling system is required only if there are constraints in packaging and only for the stator. Therefore, we see applications for this motor in PVs and LCVs as well.
Are there any advantages to deploying these motors in 2Ws?
The advantage in terms of cost is more with higher capacity motors. That is why we are targeting applications for more than 10kW.
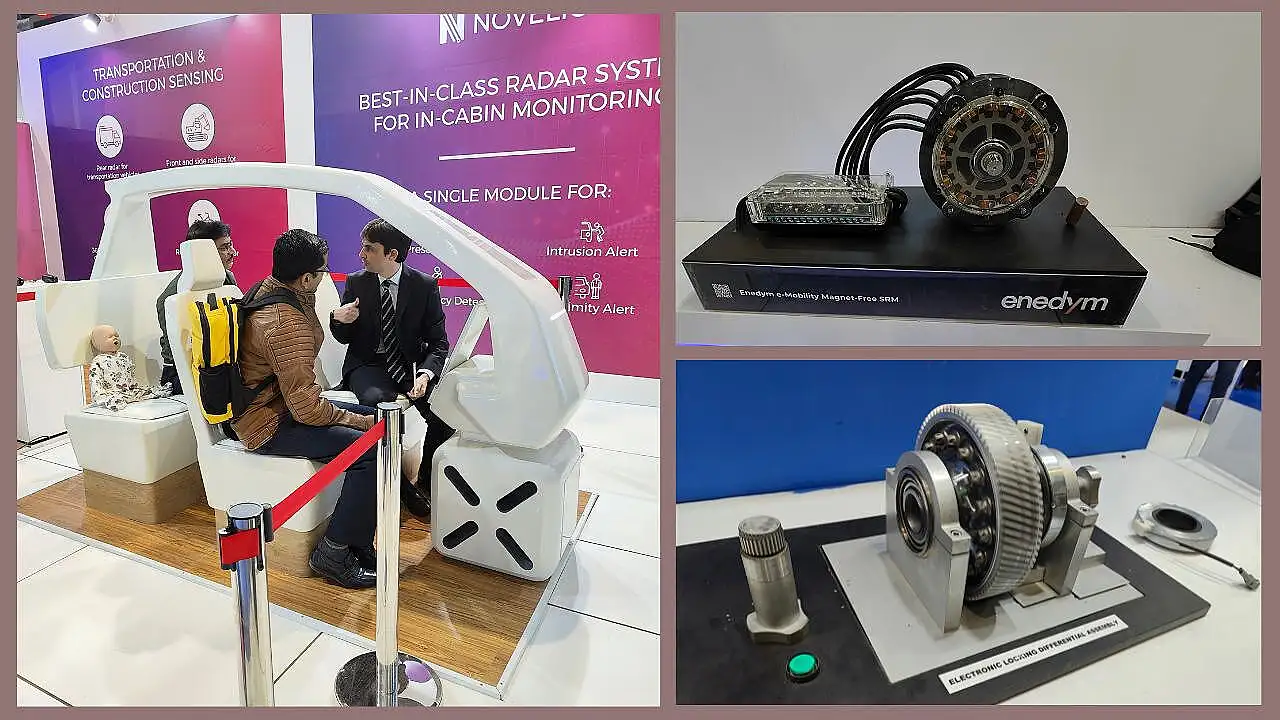
What are the unique features of the electronic locking differential assembly?
When a vehicle takes a turn, the inner wheel takes a lesser turn than the outer wheel; the differential plays the role by dividing the power (from the engine or motor) to either wheel based on the requirements. A locking mechanism is triggered manually to lock the wheels to mitigate bad road conditions.
We have developed an electronic locking differential, where a signal sent to the system locks and unlocks the differential. With the signal from OEM’s controller, the differential can be locked/ unlocked in real-time, in a fraction of a second. A solenoid coil inside the system creates magnetic force and triggers the locking of one of the differential gears.
What are the opportunities you see in the adjacent areas?
Electrification is a given thing now, and they have to be necessarily autonomous. Therefore, we created a technological roadmap to make ourselves move towards autonomous and autonomy, while we transition to electrification. As a Tier-1 company, we realised that sensors and software are essential. We already have software for motor controllers, but that is not enough. We need to go one notch ahead.
As tomorrow’s car will be software-driven, we were looking at partners or companies for acquisition in sensors and software. That led to us acquiring Novelic recently. They have unique solutions based on radar, which is impervious, and the technology has been used since World War-I. However, the technology was not used in automotive as the antennas were huge. Thanks to electronics and allied developments, these antennas have become miniaturised. Our radar sensor from Novelic has the chip, the receiver and the transmitter.
Of course, the radar will not be the only sensor, as there will be requirements for cameras and others. There will be a fusion of sensors, but radar will play a major role in autonomous vehicles.
As a CTO, what are the probable areas you are looking at to introduce new technologies in the near future?
Our motto is torque per gram – how do we get maximum torque with minimum weight. We are developing products in differential, driveline gears and motors that are as compact as possible and give maximum output. We see that in India, after the electrification of 2/3 wheelers, it will be small commercial vehicles (SCVs) – the last-mile delivery segment – and city buses. Therefore, our focus is to develop electrified applications for SCVs and buses.
Our traction motors are currently for 2/3 wheelers – sub-100V. We are now looking at higher voltage motors, say up to 800V. We already have motor controllers, and we may look at adding a few electronics and offer added features such as DC-DC converters, chargers and such things.
On autonomous and sensing, we will look at promoting radar sensors, the in-cabin sensing technology we have from the Serbian company Novelic. To get a five-star NCAP rating in Europe, the vehicle must have ‘unattended child presence detection’. There are cases where the child is left in the car, restrained, and windows shut. As the child could not withstand the temperature building up inside the cabin, there were deaths due to heat stroke. Soon, these regulations will become global.
The radar technology senses breathing and heartbeats, which are different for children, and triggers an alarm. This is the real cutting-edge technology for safety. The radar sensor can identify the occupants of the car and can eliminate the load sensors (including the related wiring harness and assembly time for OEMs) currently used to sense the occupants to trigger the seatbelt alarm.
Also Read:
Sona Comstar Achieves 350 Mn Gears Production Milestone
Sona Comstar Acquires 54% Stake In NOVELIC
Sona Comstar Achieves 100k EV Traction Motors Production Milestone