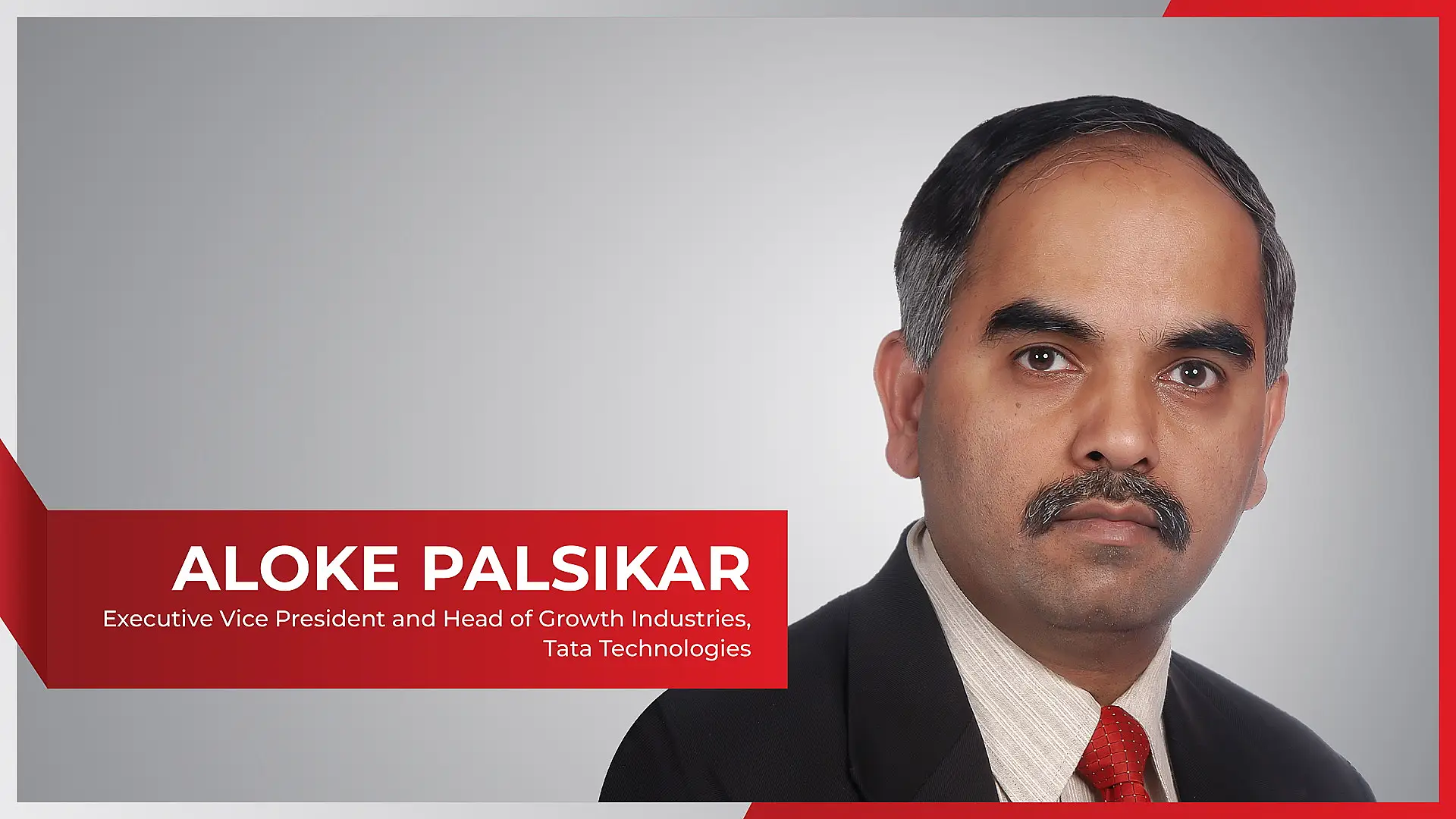
Aloke Palsikar joined Tata Technologies in 2020 and handles its Aerospace Vertical from Mumbai. In his career spanning over 34 years, he has worked with Siemens, Larsen & Toubro and Tech Mahindra. Associated with the aerospace industry for two decades, Palsikar speaks fluent German. He graduated with a Masters in Engineering from IIT Mumbai in 1987 and later went on to gain an MBA from IIM Ahmedabad.
Please provide an overview of the work done by Tata Technologies?
Tata Technologies is predominantly a product engineering and digital engineering partner for the manufacturing industry, with a total strength of around 12,000 engineers. We are present only where manufacturing activities are required to be performed. When it comes to manufacturing, we focus on three verticals – automotive, industrial/heavy machinery and aerospace. We are the unseen arm of a lot of engineering activities, which go on, in these sectors. Essentially, our portfolio is a ‘meter wide but a mile deep’.
We are present from end-to-end for product development, right from the concept design to manufacturing, handling whatever engineering requirements are needed. With the emergence of digital technologies, we are also going beyond the manufacturing aspects to look at the after sales aspect, including customer experience and aftermarket sales and service, and feeding that data back to product design. This is the entire value chain of activities that we are involved in.
Please provide an insight into the work done by Tata Technologies in the Aerospace domain?
In the aerospace domain, Tata Technologies is engaged in all the aero-structural aspects and are working on aerostructures, fuselage, doors, wiring harnesses, primary and secondary structures, etc. We also provide engine performance analytics for commercial aircraft engines.
One area that we are doing a lot of work is in cabin design, which includes design of interior galleys, seats, infotainment systems, etc. We do manufacturing engineering, which is designing the way the product gets manufactured. This involves work on production jigs, tools, fixtures, shopfloor layout, etc, wherein we bring in significant productivity improvements.
Work on conversion of passenger aircraft to freighters is also an important business area for us. This work is typically undertaken on aircraft, which are at the end of their passenger service life. When a commercial aircraft is rolled out of a factory by the OEM, it begins a service life that will go on for approximately 40 years.
Usually an aircraft is used for passenger transport for 20-25 years, following which it is converted for freighter/cargo use. This is when an aircraft gets a second lease of life. Passenger to freighter aircraft conversions are an emerging engineering opportunity for us and we have already done quite a lot of work there.
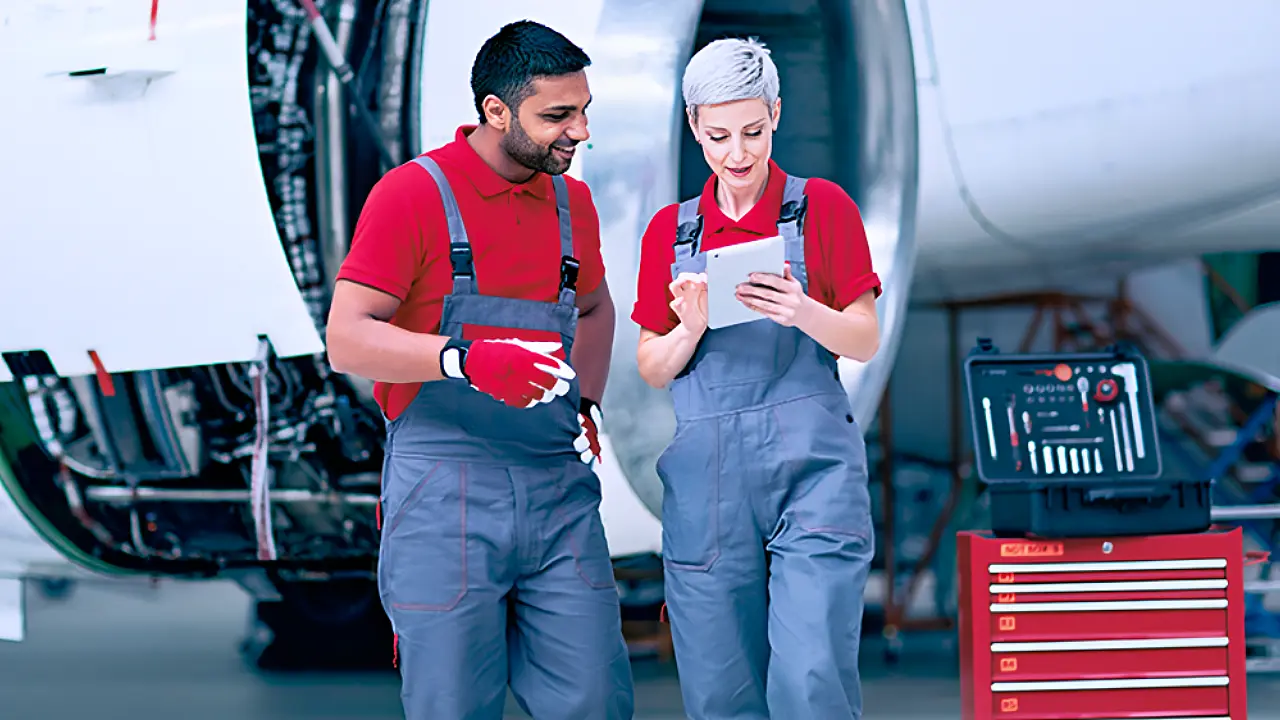
India is now globally making a name for itself as a manufacturing hub for aerospace. How do you see this trend growing?
I am optimistic that we are in the upcycle mode for the aviation industry. When one takes into account the backlog of aircraft orders with both major OEMs, it is enough for the next 7-8 years. We also have new technologies entering the market and I believe that we are in a sustainable growth cycle in the aviation sector.
For the last 10-15 years, India has been an engineering and R&D hub for many companies, including the aerospace sector, where OEMs have invested heavily in India for talent. We are seeing aircraft manufacturing in India growing and the first of these is the C295 military transport aircraft programme, between Tata and Airbus, coming up in Gujarat. This is the first time that such a task is being undertaken in India by a private sector firm, but definitely not the last.
The growth of aerospace manufacturing in India is also accelerating the development of the ancillary industry in this sector. On the services side as well, a lot of high-end work today is being done in India. New product design, new product conceptualisation, and a lot of core design work now gets done here.
Please provide an insight into upcoming technologies that you view as important for Tata Technologies?
We are focusing right now on digitalisation. So, from product design to manufacturing, we are now trying to create a ‘Digital Twin’ or a ‘Digital Thread’ for the entire value chain.
Earlier, when a designer was working on an aircraft programme, he or she would complete the design and then pass it on to another team, which would then work out the cost impact. If the cost was too expensive, the designer had to go back to the drawing board. Our engineers are now working on ‘Design to Cost,’ where, when changes are made to the design, they receive a bill of materials, which states the cost impact of the change. This reduces the iterative process in the design and introduces greater efficiencies, allowing our engineers to meet customer requirements in a more efficient manner.
Another area, where efficiencies can be introduced, is related to work instructions to the shopfloor for manufacturing activities. Earlier, this was mainly paper-based but if it can be automated to cater for work instructions from the manufacturing schedules to the last person, who is doing the manufacturing work, it would improve efficiency and deliver big savings.
So, on a Final Assembly Line (FAL) for an aircraft, if we are able to have a digitised version of the instructions, it would allow the assembly schedule to be adjusted depending on supply chain variability or product availability or changes in delivery schedule. This would be done without compromising on the time available in that shopfloor for that day or for that hour. So, the ability to quickly change work instructions adds to another layer of efficiency and we are focussed on this area.
We are also doing a lot of work in the digital Maintenance, Repair & Overhaul (MRO) space. We are developing our own MRO solution as the digitalisation of the MRO value chain is a market opportunity for us.
We are also looking at the opportunities that will arise from electrification of aircraft. We are already doing a lot of work on electrification of automobiles and looking to see how we can bring this to aircraft. Some conceptual pilot studies are underway at this stage.
So, essentially these are the three to four areas we are looking to invest our time and resources over the next two to three years.
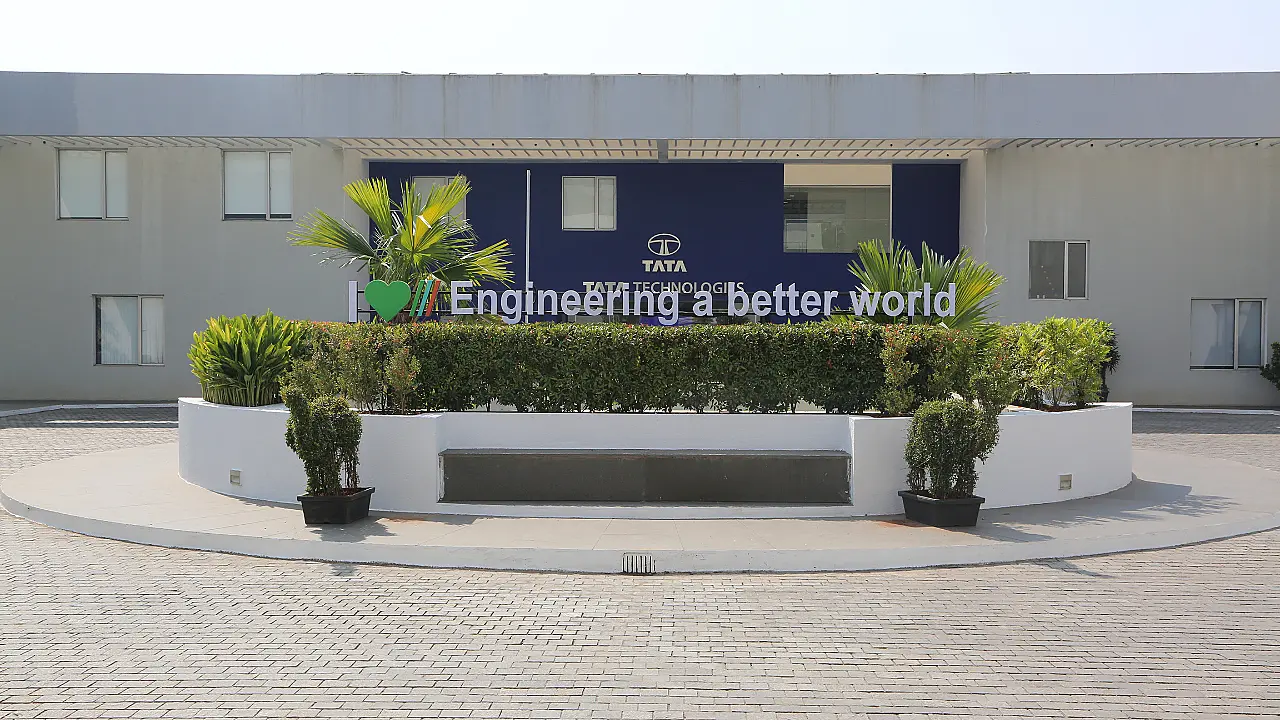
Please provide an insight into some of the solutions provided by Tata Technologies for its customers?
We provided an innovative solution for one of our airline customers, who needed to refurbish their aircraft cabins in short order and needed it completed quickly. The seat manufacturers did not have the capacity to supply the parts in the time required.
Our teams inspected the aircraft for broken parts or parts which were damaged/ needed to be replaced. We then scanned these parts using digital scanners, reverse engineered them and sent the airline prototypes made with the same material configuration. The airline then had their own suppliers manufacture these parts. We were able to complete the activity within two months, which could otherwise have taken months.
A few years back, we had undertaken an exercise for an engine OEM, which wanted to increase its production capacity but did not have the CAPEX. By rearranging their shopfloor, doing a time and motion study and alignment of various shopfloor equipment, we were able to increase the production rate by half an engine every month. If the company was earlier making two engines a month, it was now able to produce three. Our input was very much appreciated because there was no CAPEX involvement and yet resulted in an increase in productivity.
We also developed an innovative solution for an Indian OEM, which wanted to undertake performance analytics. We suggested a very different data model approach, because this was data coming from an engine. As you know, an engine has thousands of parameters that need to be monitored. This data then can be used to improve the performance and behaviour of the engine.
Our approach was different from what was being suggested by the OEM, which we then tested and demonstrated. The result was that we were able to deliver a 20% saving of their cost to build such a solution.
Also Read
Tata Boeing Aerospace Delivers First AH-64 Helicopter Fuselage To Indian Army
Tata Boeing Aerospace Ships First Boeing 737 Vertical Fin Structure
Airbus Gets DGAQA Approval For India C295 Quality Mgmt System