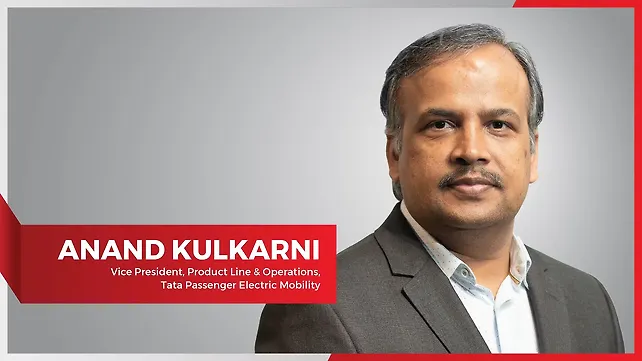
For someone who joined Tata Motors as a graduate engineer in 1993, Anand Kulkarni has over the years with the company contributed to all passenger car products. He has worked in multiple functions like engineering and product development, and has extensive experience in product conceptualisation, advanced product creation, programme management and delivery. An automobile engineer from the University of Pune, Kulkarni’s core strengths lie in the areas of thermal management, vehicle dynamics, ergonomics, attribute management and multi-parameter optimisations. An alumnus of the SP Jain Institute of Management & Research, Kulkarni leads the team responsible for development of all Passenger Electric Vehicles at Tata Motors.
From a product and engineering perspective, how significant is the Nexon EV MAX for Tata Motors?
The Nexon EV MAX creates a formidable package in terms of range, reliability, safety aspects and features that we’ve been able to incorporate. It is one segment up in whatever categories you look at. When we started the Nexon EV three and a half to four years back, we wanted to electrify an aspirational product that was already existing.
We looked at putting all the basic ingredients in place in terms of how the power and torque should look like, how the weight distribution should be and how the overall cooling systems should be managed because we were about to introduce a high-tech, high voltage architecture into a hot country like India, where aspects of how the battery will behave over a period of time in elevated temperatures, etc, there was no past data available.
I think the Nexon EV MAX leverages all the learnings of the 25,000 cars and 100 million km, and puts it into a package that I think is complete now.
Talking about hot weather conditions in the country, what kind of improvements or modifications have you brought into the battery pack on the Nexon EV MAV, specifically into thermal management?
The work that we had done in the existing Nexon EV itself from a thermal management perspective has been very, very stable. The data over the last couple of years and a 100 million km is essentially reinforcing and vindicating the convictions that we had in terms of how systems could be designed safely, and how batteries could be managed in a very safe manner.
That has been absolutely critical to now being able to package additional energy underneath the vehicle and still be confident of how this energy is going to behave, and how it's going to deliver additional range and flexibility to our customers.
From the perspective of structure or structural safety, this has also given us more insights into how the weight balances should be taken care of so that you don't run out of capacities and saturation limits on the tyres.
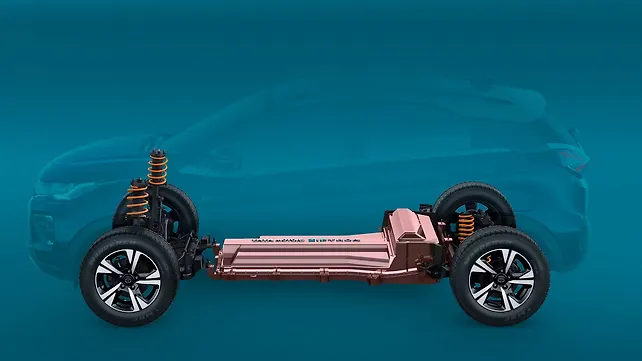
We've also been able to add additional controls in the form of an electronic stability control on the Nexon EV MAX, and all put together I think, all the work that was done earlier has been superbly reinforced and re-engineered in places to make sure that we have a brilliant package.
How did you go about packaging this slightly bigger battery pack to bring in more energy into the overall vehicle?
We've looked at battery packaging efficiency. The cells are the same, but we’ve packaged the cells differently. Look at it as a unitary volume, inside which you pack cells, and then you can have packaging efficiency to it. We've improved the packaging efficiency on this battery by between 7-8%.
We've also expanded the battery slightly from the bottom as well as from the top by modifications of the floor so that we can accommodate a better battery. We have also looked at certain other structural elements, where we have optimised those areas to provide more uniform spaces for the batteries to be accommodated. All of this put together has helped us in being able to increase the capacity by about 10 kWh.
What about the BMS? What are the kind of modifications you have brought into the BMS?
Primarily from a platform perspective, the BMS remains the same, but we have brought in the ability in this BMS to push over-the-air (OTA) updates. We will bring this on when we are ready with it, but as a platform, it is now available.
From a future standpoint, what are the possibilities you have within this platform?
When we talk about Ziptron, we talk about a certain architecture, and today that architecture is helping us deliver additional products. When we look at architectures, we look at the ways in which we are going to do certain components, we look at strategies, and we look at how these components are validated within the overall ambit of Indian drive conditions. So that's one part of it.
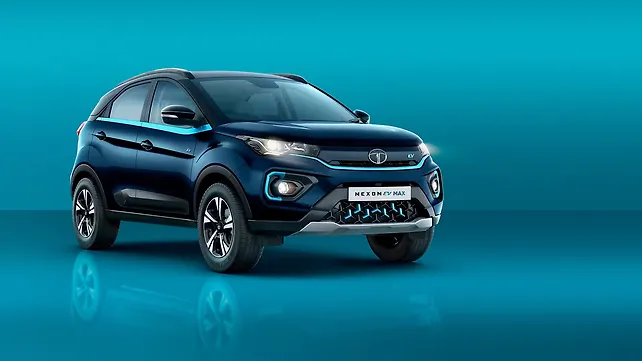
The second part is that there are certain components that will become a part of the library. For example, the i-VBAC (intelligent – Vacuum-less Boost & Active Control) is an important component and that will be available for application on a larger number of vehicles because that’s one way in which we can deliver safety as well as a dynamic control, and we can deliver optimal use of energy through regeneration.
Then there will be certain additional features like electrical park brake (EPB), which will become common at least in a certain category of vehicles. Then you have the ability to look at features, which enhance comfort and convenience for the users. Cruise control, for example, is a very critical requirement, not only from a comfort point of view but also from the perspective of energy optimisation. We look at the ability to combine multiple electronic boxes and functionalities into one common box, and that becomes a library part that can span multiple products.
All of this put together, we are creating a strong foundation, which will help us to consistently deploy a certain functionality or certain reliability and a certain logic across products; and secondly to make ready-made components and parts available that can be deployed faster with more standardisation across a large number of products.
And do we see standardisation across ICEs and EVs?
No, I'm talking more from an EV perspective, because we’ve already been doing this for ICE cars. For example, there are a lot of parts that get shared, particularly the hardware parts that get shared between ICE cars and EVs. But I think from an EV perspective, because the journey is recent, we need to develop this entire platform, this entire common library of parts, which will enable us to go much faster in the future.
Apart from the battery pack, have you brought in any changes to the charging technology as well?
We got a better charging solution now. While the existing Nexon has a 3.3 kW charger, we now have a 6.6 kW charger on board the Nexon EV MAX. Along with it, we’ve also designed a bespoke wall charging solution, which is capable of supporting 7.2 kW. That is superbly aligned with the performance of the car in terms of charging performance and behaviour.
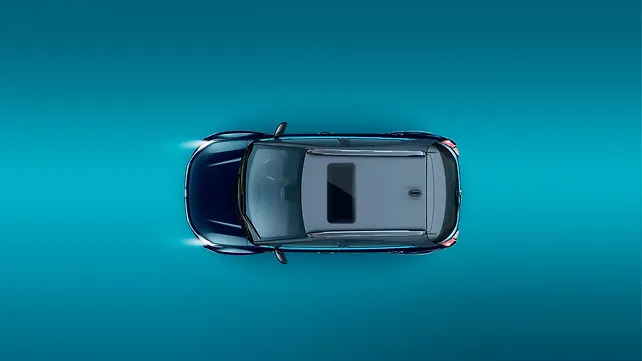
ESP gives us the ability to do multiple functions like hill hold, hill descent control and the four disc brakes give a better fade compensation capability making it a wholesome package. We have multimode regen and cruise control.
The Nexon EV had two modes – Sport mode and Drive mode. Because of the enhanced power that we've been able to give on the Nexon EV MAX, we’ve also been able to introduce an Eco mode. If you want to do long drives on highways with cruise control and the eco mode activated, then the car can travel that much more distance.
The Nexon EV MAX is also a 100 kg heavier than the regular Nexon EV. What changes have been made to the overall platform to accommodate the extra weight?
Seventy of the 100 kg additional weight is from the batteries. A part of it is on account of the changes that needed to be made to suspensions and to some other components, to be able to structurally take care of this additional weight. In case of crash, for example, if you need to absorb that additional kinetic energy of the 100 kg, you need to make the structure more robust. That's been done from the front-end longitudinals into the front firewall kind of stiffening.
When you carry additional load and still want to make the car equally comfortable in abusive conditions, certain structural components need to undergo more strengthening. A part of the weight increase is also on account of that.
On the wheels, instead of the four-bolt arrangement, it's now gone to five-bolt arrangement, which is essentially to be able to house generation three bearing that gives us lower frictional energy consumption. Therefore, the wheel rims are different. That enables us to add more elements of robustness to the entire design.
Moreover, we’ve changed spring rates on the springs. We've changed damper settings so that it still retains comfort as the original Nexon did.
Have you also introduced newer materials to the structure?
Some level of high strength steel has found its way because that's one way to improve the structural rigidity and robustness. However, I won’t be able to put a number to it at this stage.
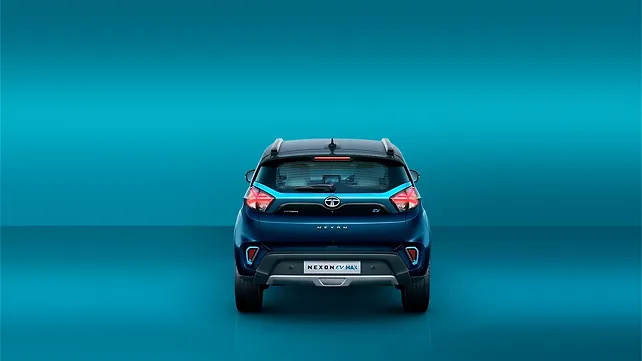
Despite the learnings you’ve had in your EV journey, what continue to be some specific challenges for the organisation?
We've already spoken about 10 vehicles to be introduced within a span of five-odd years, starting January 2020 up to sometime in 2025. We’ve already laid out to you our Gen 1, Gen 2, and Gen 3 approaches. So, while there is product development that happens on one side, there is also a lot of activity happening on localisation, for example.
That's something that we are investing in very heavily, and we are actively working on that. Sometimes it is actually counter-productive to cost because the volumes are still nascent. We want to invest more and bring more value locally, and therefore we are early investors in localisation.
But when you have this kind of intense, very frenetic, furious activity going on, there's a lot of work. That's been one of the challenges, to be able to have so much activity done. We are also at the same time trying to get more people on-boarded. So, it's a lot of activity and a lot of challenging times.
How is your supplier base coping up with the transition?
We engage with our suppliers on a very early basis. As early as 15-17 months back, we had started telling them how the volumes would grow. Initially, it was a lot of incredulity, with the kind of projections. But with the success that we've had in the past few quarters, there is belief in the system and therefore there's a lot of active work that happens with suppliers, for them to also be ready with what we would want, two or three quarters down the line.
All in all, intense work, a lot of movement, and a lot of action. But the results are there to speak about it and we're happy about it.