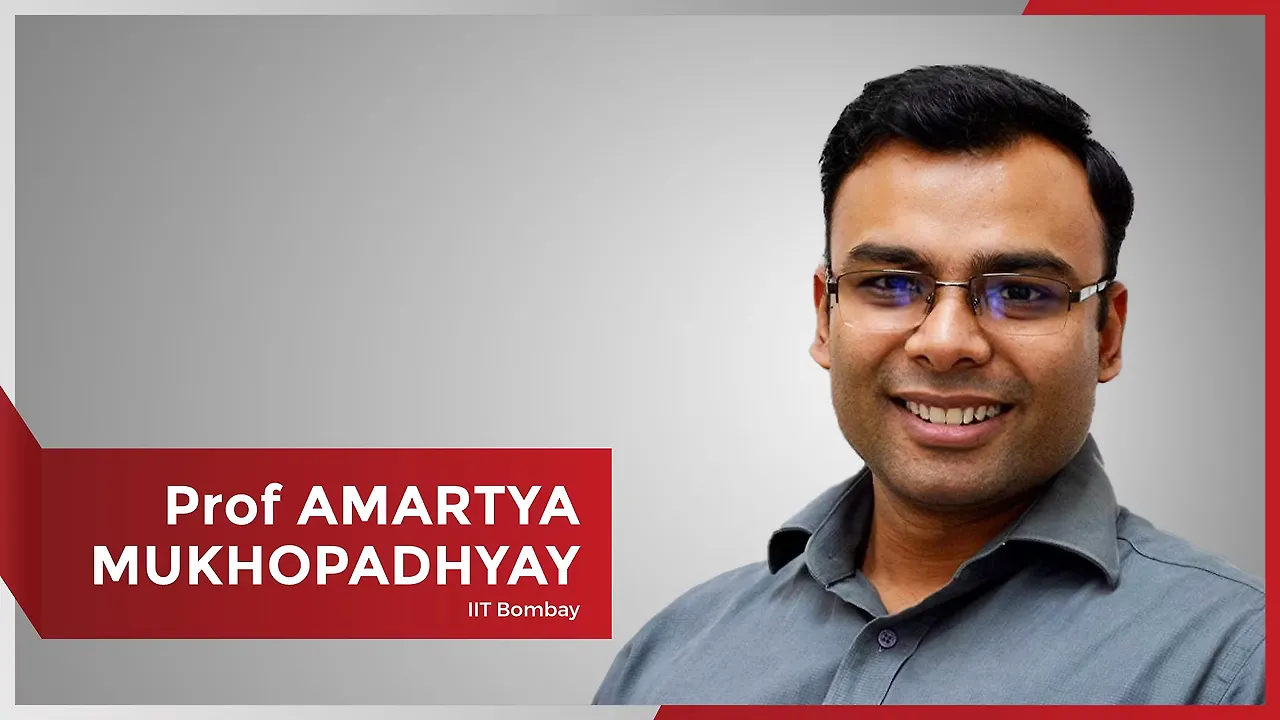
The Tata Transformation Prize celebrates visionary scientists in India who are pioneering breakthrough technologies to tackle the country’s most pressing challenges in food security, sustainability, and healthcare. With a focus on driving impactful innovation and scaling high-reward research, the prize serves as a catalyst for transformative solutions.
In 2024, an international jury of leading experts selected three winners from 169 entries spanning 18 Indian States. Among them, Professor Amartya Mukhopadhyay from the Indian Institute of Technology Bombay was recognised in the sustainability category for his work on designing and developing safe, sustainable, and cost-effective sodium-ion batteries using ‘aqueous processed’ electrodes. In this conversation, he shares insights into his research, its potential impact, and the future of energy storage solutions. Edited excerpts:
Can you tell us about your work on Design and Development of Safe, Sustainable and Cost-Effective Na-ion batteries based on ‘Aqueous Processed’ Electrodes?
The type of cathode materials which give Na-ion batteries the ability to hold a lot of charge and, hence, store a lot of energy, i.e., layered sodium transition metal oxides, are very easily damaged by water, even just from the air around us. This makes their fabrication and handling very challenging, requires using a dry room, increases energy consumption, increases its carbon footprint, and typically requires the use of incredibly toxic chemicals for electrode processing.
And that is precisely the problem our work, as referred to by you in the question, is solving; i.e., developing cathode materials that can withstand exposure to water, and thus do not require the use of such hazardous chemicals, and also reduce energy consumption for handling/storage.
In the cathode materials under consideration here, water-based species can find its way into the crystalline lattice and force the sodium ions to leave by interrupting bonds with oxygen ions in the lattice.
Sodium gets depleted and the bulk, as well as surface, structure of the cathode material is negatively impacted in a big way. In fact, one cannot make a battery cell with such air exposed cathode.
We discovered two avenues to address this. One of them involves making the lattice more tightly packed by carefully selecting the lattice composition to strengthen the sodium-oxygen bonds, to ensure that water-based species can’t enter, thus, also preventing them from kicking out sodium ions.
The second avenue involves designing the lattice by strategically embedding positively-charged ions to repel, block and prevent water-based species from entering and interrupting the chemical bonds. We’ve used these methods to great success, creating materials that are so water-stable that we can drop them in water and stir them around for long durations without damaging them!
With these accomplishments, we can process these cathodes without needing energy-intensive dry rooms, and without the use of incredibly toxic chemicals.
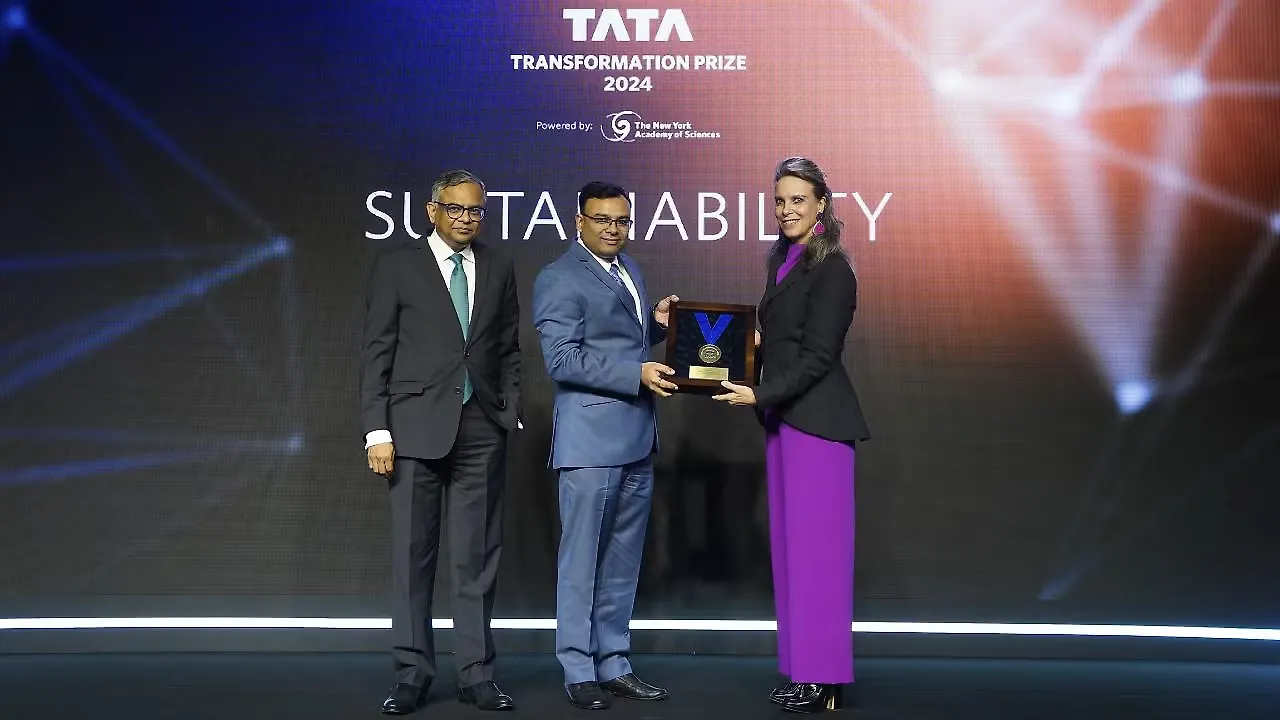
Sodium’s abundance lowers costs and supply risks, but its battery materials must withstand water-based binders and solvents without degradation. How do you ensure stability while maintaining electrochemical performance?
As long as the cathode materials are rendered highly air and water stable, as we have been able to, the composition and structure remains absolutely intact even after aqueous processing of the electrodes using water-based binders and water as solvent. Hence, there is no compromise at all with the electrochemical performances.
In fact, in some cases we have also found that the usage of water-based binders, as opposed to the more commonly used PVDF binder (with NMP as solvent), results in more favourable electrode slurry and, thus, even facilitates slightly improved electrochemical performance of the aqueous processed electrodes for Na-ion batteries.
Sodium reduces mining impact, and aqueous processing eliminates toxic solvents, enhancing sustainability. However, scaling up without performance loss or contamination is challenging. How do you balance these factors?
Aqueous processing simply eliminates the need for energy intensive dry rooms and eliminates the use of toxic chemicals for electrode processing, while allowing the exact same electrode processing route to be followed and, hence, use of the same set-ups as used otherwise. Thus, there is no question of aqueous processing affecting scalability at all; rather, may help with it.
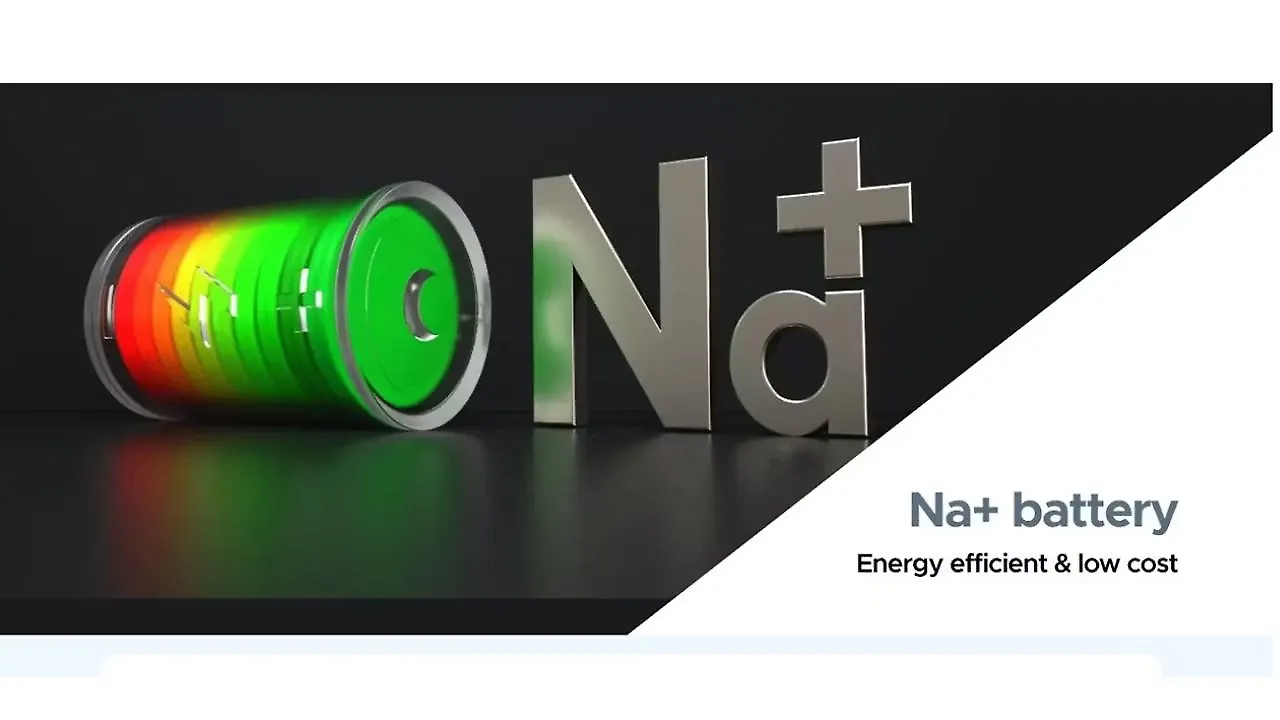
Na-ion batteries have lower energy density than Li-ion. How do you optimise electrode materials and processing to boost capacity while keeping costs competitive?
While the fabrication process of Na-ion cells is the same as for Li-ion cells, the usage of more abundant materials in the case of Na-ion cells can lower the cost by ~20-25%; of course, depending on the supply chain. Now, 'aqueous processing' of cathodes, as against the present NMP-based processing, can further lower the preparation cost by ~15%, in addition to lessening the power consumption.
Can you tell us about the application of your research with respect to automotive industry?
In its present form, Na-ion battery technology can be readily adapted to making power grid storage more robust, as well as for other stationary storage applications. In the context of the automotive industry, Na-ion batteries can now be used for three-wheelers and also buses.
With further enhancement of energy density, which is on the cards, they will be suited for application in four-wheeler electric vehicles, even if with a slightly limited range, to start with; but will lower the cost of electric vehicles, making their use more economical and affordable for many of us.
Can you quantify the benefits of Na-ion over other battery chemistries?
While quantification of the benefits depends on the particular Na-ion vs. Li-ion battery chemistries being considered, in general, the benefits of Na-ion over Li-ion technology are numerous:
Na-ion batteries operate safely over a wider range of temperatures (which is advantageous for tropical/subtropical regions), they are capable of charging faster, they can be safer during operation, as well as when stored/transported (at zero volt), and they can be cheaper for the same amount of energy stored, to name just a few. Of course, Na-ion battery chemistry is a more sustainable chemistry.
Also Read:
How Converging Technologies Are Shaping Smarter, Sustainable Vehicles