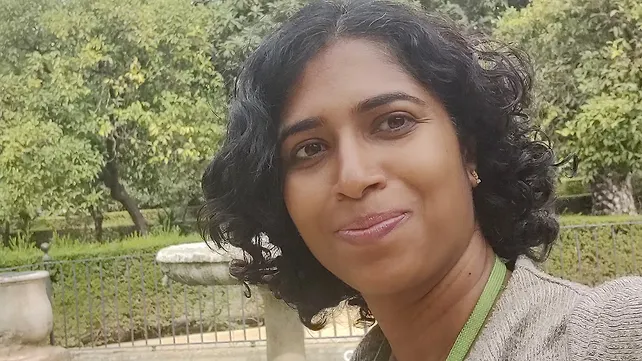
Shirin Hameed is currently the Chief Marketing Officer of DEP (Detroit Engineered Products) involved in planning and leading comprehensive B2B marketing projects in the B2B technology space. She is currently leading the global marketing team and is also responsible for all marketing activities for DEP and its product lines globally. In the past she has worked with Tata Technologies and National Instruments.
Can you update on DEP’s operations?
DEP operates in three verticals, including Engineering Services, CAE Software (we have our own CAE platform, DEP MeshWorks), and Product Development. Headquartered in Troy, US, we have our own offices in India, Japan and China. We have a network of channel partners and distributors globally through whom we achieve maximum reach. We have helped several companies reach to market faster across several industry sectors such as automotive, defence, aerospace, biomed, energy, oil & gas, consumer products and heavy equipment.
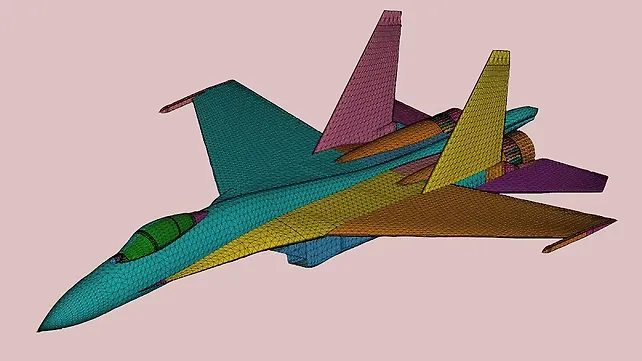
Can you elaborate on DEP MeshWorks and other products that you have?
DEP MeshWorks is a CAE driven integrated platform for pre- and post-processing, involving rapid concept CAE and CAD model generation, parameterisation and optimisation, advanced meshing, process automation, concept modelling and CAD morphing. All these tools can be used in the design stage directly in the CAE by companies to optimise their product without working in the CAD design.
Essentially, it has a power-packed tool offering that simplifies tedious, time-consuming processes associated with CAE design changes. This naturally helps companies reduce the product development cycle, saving them time and money and get to market faster. We work across turnkey projects like 2D modelling, concept design, benchmarking, value engineering, tool design, and reverse engineering.
Our development wing works with companies to help build innovative products. We have some products in-house as well. Companies have come to us with just an idea, and we have helped evaluate and design the product.
We have created industry’s first volume production combustion sensor that achieves better fuel economy, reduced emissions, and enables the use of multiple fuel types, including biofuels. This technology has more than 10 patents. We have designed and developed a drone that deters birds from causing damage to assets in aerial territory for a client who needed this. We have developed an in-house EV scooter as a technology demonstrator, which we also showcased at the Auto Expo in 2020.
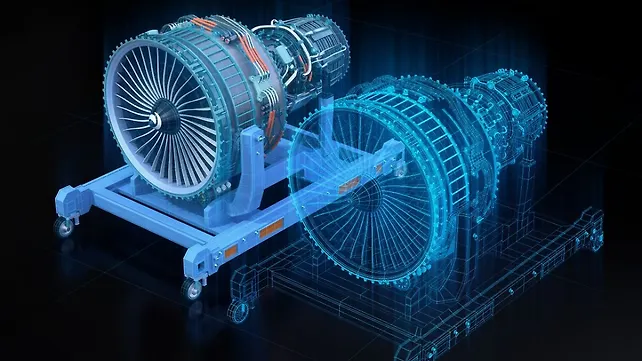
What are your contributions to automotive, aerospace, railways and maritime sectors?
Automotive is the sector we have been working the longest in, but the fundamental principles remain the same, and we support all CAE design engineering and workflow projects in aerospace, marine, railways and other industries.
In automotive, we have worked right from conceptualising a new vehicle to helping companies create multiple variants from an existing model (naturally, this saves a lot more time than coming up with a new model), as well as optimising and providing consulting services like safety, crash, durability, NVH etc. For instance, we worked with a Mahindra vehicle to minimise the mass model of an SUV by 12%, while maintaining all the performance targets.
In shipping, we were asked to convert aluminium bulkheads into a composite bulkhead, and we were able to reduce the mass by 28%, with performance improvement and maintaining the same level of stiffness.
Standard CAE works like design analysis, weight optimisation, alternate configurations or materials, parameterisation, and optimisation is what we do regularly across industries, including aerospace, railways and maritime.
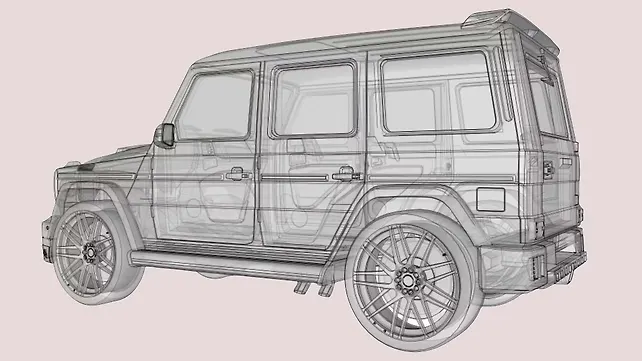
What are the compelling reasons for an OEM or a supplier to reach out to you, while developing new products?
The main reason why OEMs like to work with us is our in-house talent pool; we have a high number of experienced Masters and PhD holders in our team with domain experience. Another reason is that we use MeshWorks, which is our proprietary software developed in-house. This gives us a great degree of flexibility and customisation to project needs. We use a minimalist approach technique, and this, combined with MeshWorks, makes us comfortably achieve 30-60% time savings compared to the traditional DoE approach.
What are the challenges and opportunities you see with EVs emerging in the automotive space?
Charging is a critical component. Consumers are still looking at EVs as only a city or town or neighbourhood ride, even though EVs claim more number of miles per charge. India is also a very price-sensitive market, and investment is always seen as a function of the benefits availed.
The gap between electric and conventional vehicles needs to be addressed and bridged. One way to address this issue would be to introduce more hybrid vehicles first (perhaps with a cheaper fuel like diesel) with an option to switch to electric. This will enable the four-wheeler user to switch to electric slowly. Also, in India, there has to be a dedicated awareness of the need to shift to EVs, with highlights on environmental impacts. Battery recycling needs to be looked into seriously. If Indian OEMs, selective R&D organisations and recycling providers work together, there is an opportunity to increase the life cycle of battery packs from one industry to the other.
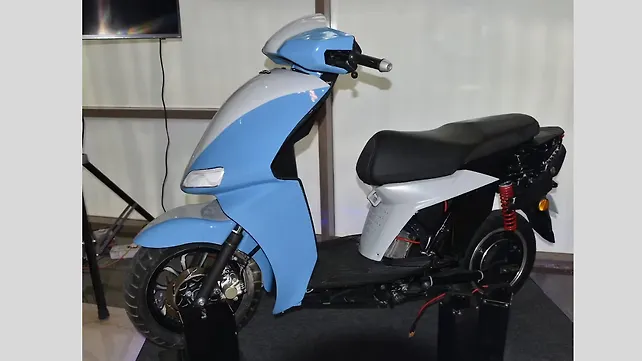
Simple product innovations (through frugal engineering, like DEP has done) will entice the consumers towards EVs. Minor improvements like the automatic reverse movement of the vehicle, simple and camera-enabled sensors etc., can go a long way in customer experience and EV adoption.
What are your short term plans?
We are continuing to expand in global markets and increase our reach both geographically and technology-wise. It is always an exciting time to be in the engineering space, and we are looking forward to some really interesting collaboration, especially in the EV and product design areas.