
R Vijayalayan currently heads Automotive Industry Field Application Engineering & Control Design Verticals at MathWorks India. He works with Automotive OEMs and Tier 1 suppliers to help adopt model-based design for system simulation, virtual calibration, embedded code generation & verification and real-time testing.
As the Manager – Application Engineering at MathWorks India, Dr Amod Anandkumar leads diverse client-facing engineers spanning multiple geographies, industry verticals, and product groups.
How does MathWorks support automotive customers optimising mechanical systems with mechatronics?
R Vijayalayan (RV): Developing mechatronic systems requires integrating physical sub-systems with control systems and embedded software. Automotive engineers use model-based design to model, simulate, and verify multidisciplinary mechatronic methods from initial development to production.
MathWorks supports automotive companies by providing MATLAB, Simulink, and Simscape, which can speed up development by working in parallel with multiple teams, predict and optimise system performance, improve the quality of mechatronic systems and test using fewer hardware prototypes, eliminate manual coding and reuse design models as operational digital twins.
What toolchains do you provide to support the development of ADAS and Autonomous?
Dr Amod Anandkumar (AA): We all know an ADAS stack has three different domains integrated to achieve functions: perception (sensors involving understanding the environment), planning (software-led decisions made on where the car should move next) and controls (interactions with the mechanical systems to achieve braking, acceleration and/or steering). We provide toolboxes for each of these domains to help engineers accelerate algorithm development.
Our investments have also been in workforce mobility by providing reference frameworks and shipping examples to help engineers discover other domains.
With automated driving comes the need for the highest safety, which entails millions or billions of kilometres of testing. Today, the industry relies heavily on simulation to achieve that level of trust in software; this is the third motivation for us to invest – to provide a virtual development environment, where engineers can test the multitude of scenarios a vehicle can encounter on a real road.
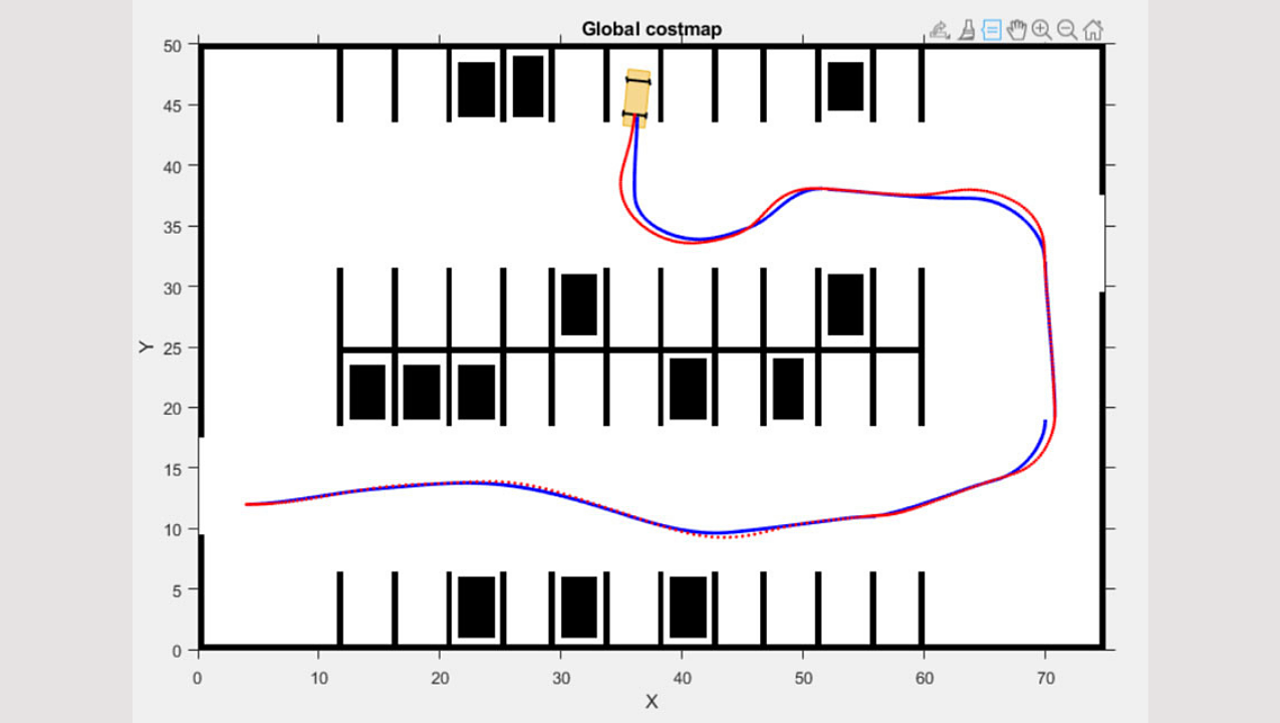
What are the solutions for connected technologies?
AA: We look at connected technologies from two aspects: the connectivity technology (5G, 4G LTE, Wi-Fi, Bluetooth, etc.) and web/cloud-based applications leveraging data aggregated from multiple vehicles.
We provide solutions for connectivity technologies ranging from simulation and analysis of network performance and signal strength to developing and testing modem hardware and software.
The data aggregated from connected vehicles enables various fleet data analytics applications such as predictive maintenance, fleet optimisation, and driver/ride quality assessment. We offer a combination of GUI-based and programmatic tools for the easy development of such advanced analytics solutions that can be rapidly deployed to web and cloud platforms.
Can you tell us about hardware and software interfaces compatibility options for Autonomous Driving (AD)?
AA: One source of AD development complexity is the sensors and interfaces it brings. MathWorks tools integrate with CAN, ROS (Robot Operating System) and can integrate with C, C++ code, and Python frequently encountered in AD development.
It is also a given that any AD development environment needs to integrate with several tools and interfaces as the complexity demands the same here; we continue to develop Simulink as an integration platform that can integrate with 150+ available tools in the market.
RoadRunner is a best-in-class tool to design static scenes for AD development and testing exports scenes to the most popularly available simulators.
Another need in the AD area is for tools to integrate with maps, and we have capabilities to import HERE HD Map data, OpenStreetMap, and Zenrin Map, which is popular in Japan. However, something we also hear increasingly is the need for more standardisation. MathWorks is a part of the ASAM organisation, and we are actively investing in OpenSCENARIO and OpenDRIVE.
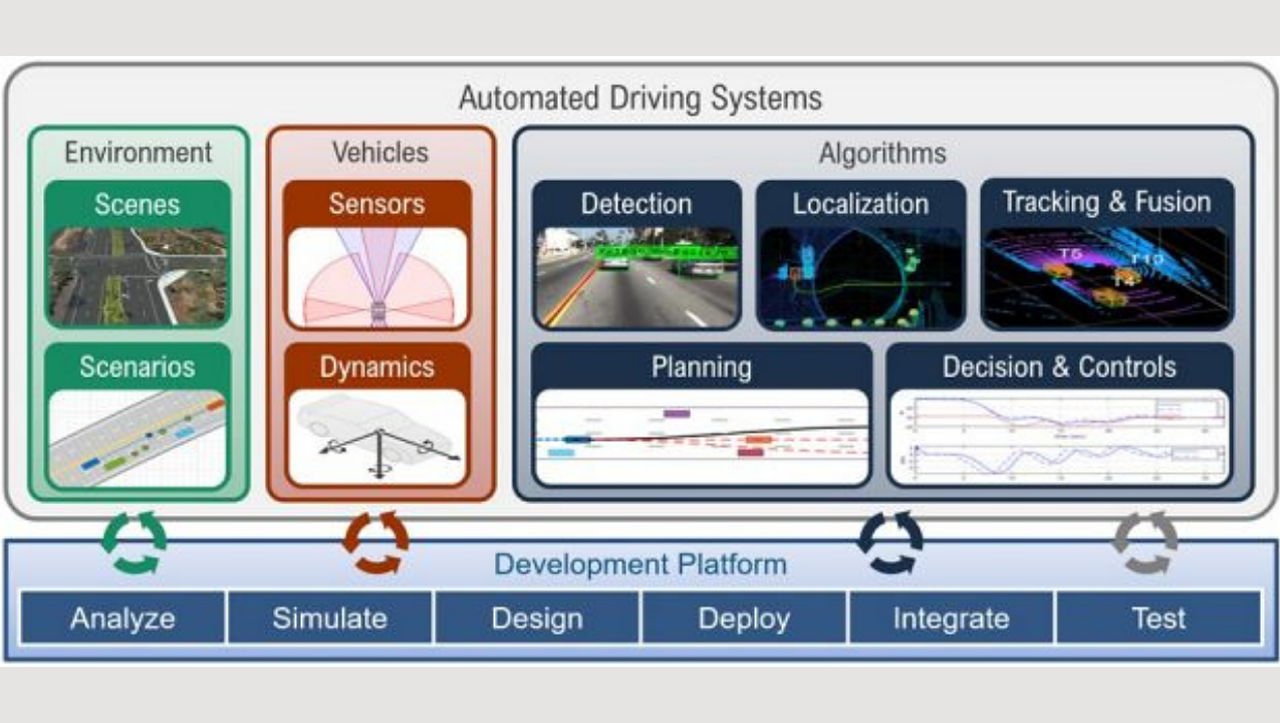
How do you address cybersecurity concerns?
VJ: The coding phase of the development process introduces a significant proportion of the defects and security vulnerabilities found in software. Software coding standards such as MISRA have played an important role in preventing unreliable programming constructs in software development processes.
CERT C, ISO/IEC 17961, and CWE are coding rule guidelines developed specifically to address the growing cybersecurity concerns within embedded systems. Common Weakness Enumeration (CWE) is an evolving security standard that provides common characterisations of exploitable software constructs that can make the software vulnerable to exploitation.
Checking the code against these guidelines can help reduce the software's attack surface and prevent security vulnerabilities. These checks are fast becoming an accepted – even required – criteria for software suppliers, when ensuring that their software complies with one or more cybersecurity standards.
Polyspace Bug Finder from MathWorks helps check the code against all of the above coding guidelines and generate reports to document compliance. It helps find such vulnerabilities and defects early, which helps in reducing rework of making the embedded code safe and secure and cuts time to market.
What are the impacts of Artificial Intelligence (AI), Machine Learning (ML) and Deep Learning (DL) on ADAS and AD?
AA: AI has had a tremendous influence on this field and has become a key enabler for these systems. Among the various aspects of ADAS, perception is where AI has had the most significant impact and remarkable progress.
Perception is challenging as the system has to detect the drivable area, lanes and other road markings, traffic lights/signs, and other road users such as vehicles, bicyclists, and pedestrians. Traditional algorithms fail to solve these complex tasks due to the diverse situations and broad variations seen in the real world.
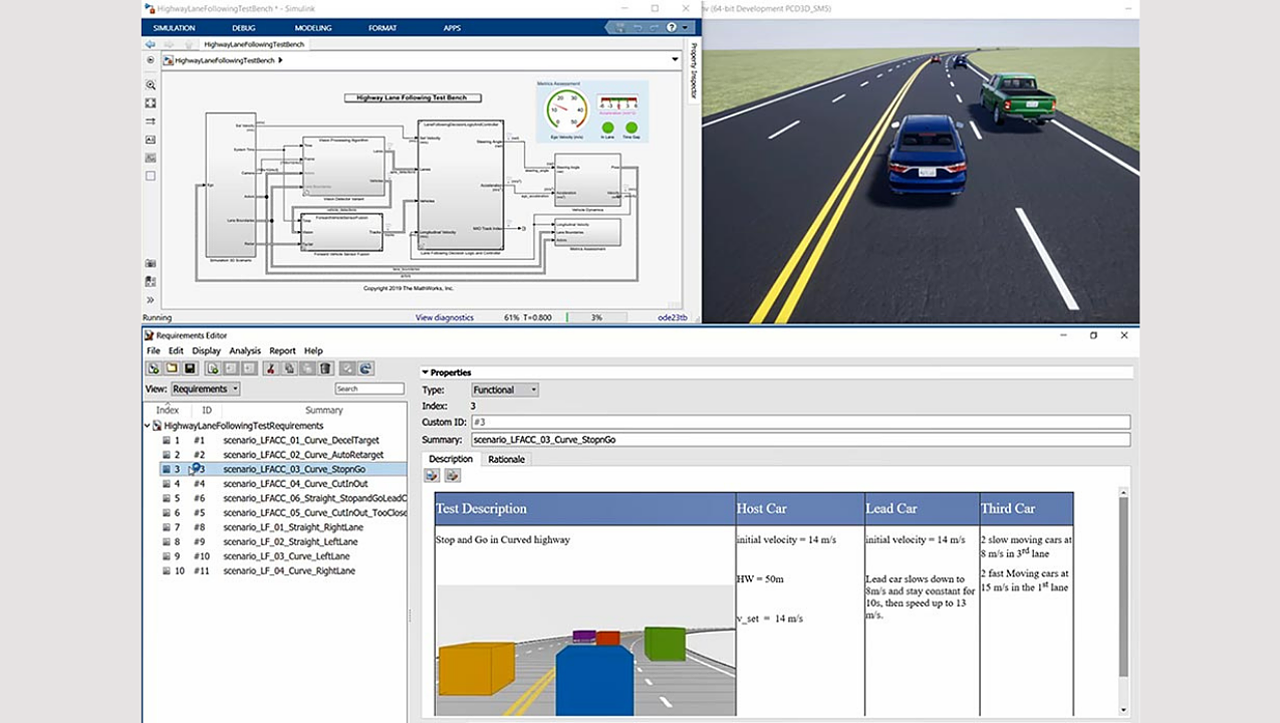
DL has emerged as the primary approach to solving perception tasks. Data labelling is another area where DL has a huge impact; it can be used to pre-label large amounts of recorded data before validation by human users, accelerating the data annotation process.
Some emerging research areas, where AI is being explored are planning and data synthesis. Reinforcement learning is a type of ML technique, where a computer agent learns to perform a task through repeated trial and error interactions with a dynamic environment. We are starting to see exciting results for training a reinforcement learning agent to perform planning tasks.
Another recent innovation in DL is Generative Adversarial Networks (GANs), which can transform input images to generate artificial images and videos that are very realistic. GANs are starting to generate additional labelled video data for training and testing ADAS, for example, by converting daytime videos to night-time videos or developing videos from scene semantic images.
How does MathWorks support vehicle makers and the relevant system suppliers in analysing emission-related issues?
VJ: With the need for efficiency improvement and meeting shrinking timelines, MathWorks supports the powertrain engineers in frontloading their calibration and testing activities using model-based calibration and virtual vehicle simulation. This approach, coupled with data analytics, enables automotive organisations to translate human expertise into a systematic and repeatable framework for testing and calibration to produce consistent results and be reusable across multiple programmes.
Our Powertrain Blockset and Model-Based Calibration Toolbox will enable the engineers to perform model-based calibration and build virtual dynos/vehicles to reduce the time spent at dyno/test tracks for calibration/tuning.
How do you support large Tier 1 suppliers to nullify defects as vehicle makers insist their suppliers achieve zero PPM?
AA: We have a long history in image processing, starting with the release of the Image Processing Toolbox in 1993. It has evolved into a comprehensive toolkit for image and video analysis that can be integrated with a wide range of imaging systems and deployed on various platforms. These tools have been used by companies in multiple industries such as aerospace, manufacturing, and materials to develop defect detection and visual inspection solutions.
A recent example is from a Japanese automotive parts manufacturer, who leveraged a DL-based visual inspection system developed in MATLAB to automate the inspection of a million automotive parts (gears) per month and find anomalies. The company works with our consultants to build a camera connection setup, pre-process images, create a custom annotation tool using App Designer, and improve the accuracy of the DL model. They generated code for the trained model using GPU Coder, implemented it on NVIDIA Jetson, and leveraged the results to the PLC for integration with the production line.