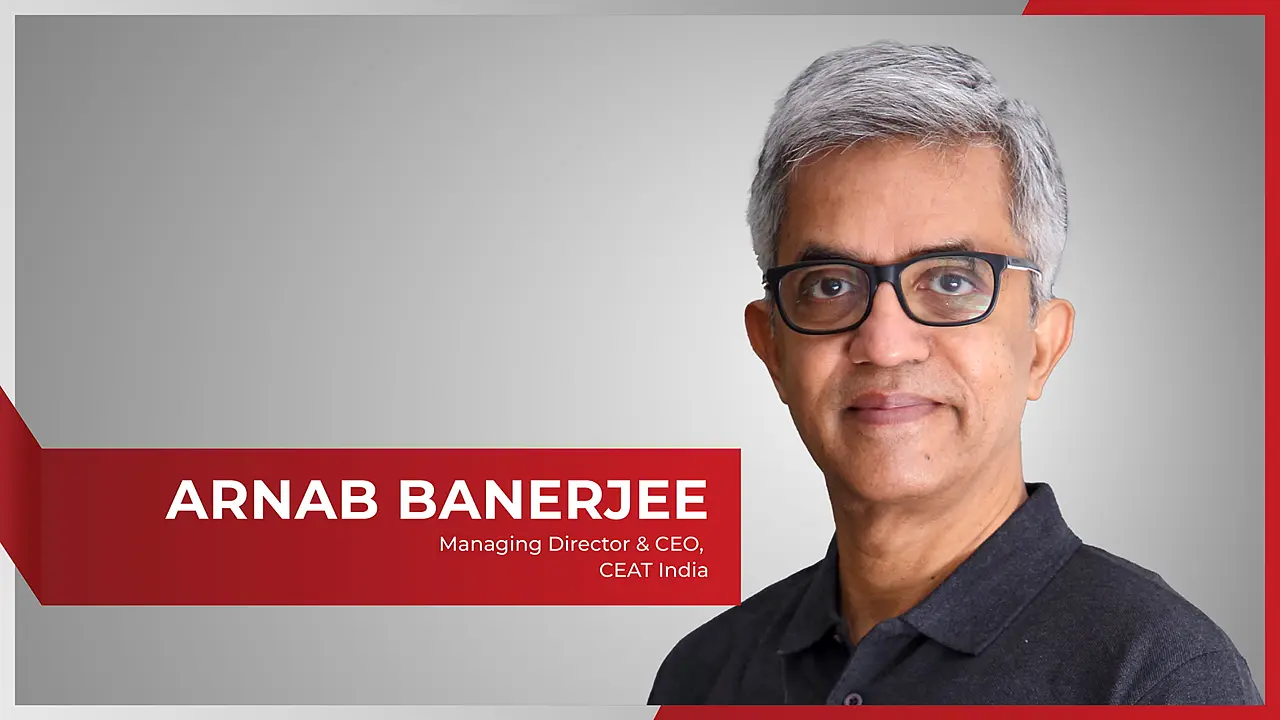
The process of winning a Deming prize involves going through an annual cycle of assessment on improvement practices. The Deming Grand also looks at quality of management, thinking and decision making.
Arnab Banerjee, Managing Director & CEO, Ceat India, spoke to Mobility Outlook’s Abhijeet Singh on what this award means to the company. Edited excerpts:
Could you perhaps throw some light on the journey to the Deming Grand?
We started in 2009 and at the time had no idea of what we were getting into. We adopted a sensei (teacher), N Ramanathan, who is one of the top TQM practitioners in the world. He told us that it does not require too much investment from capex but some mindset change and a way of doing things. He also said it would be a tough journey that would take time.
In 2015 we made a diagnosis by calling the Japanese assessors and asked them if the company was ready to challenge the award. They told us that it had progressed a lot from 2009 to 2015 but was still not good enough to win.
So Ceat worked even harder and, finally in 2017, was able to win the Deming award. After this, we thought this was the highest we could achieve since Deming Grand was simply too tough to achieve. However, we continued the good practices and started improving further. By 2021, we considered giving the Deming Grand a shot as well and did the assessment successfully the following year before getting the Deming Grand in 2023.
What were the challenges faced in this constant improvement of TQM practices on a companywide basis?
The biggest challenge with a large 60-year-old organisation is that we think we know too much and can comfortably succeed. Since we know how the tyre industry and our business work, it becomes difficult to get out of our own beliefs and systems.
The focus was to become more customer-specific and focused where all of us had to solve problems. Internal boundaries between departments like finance, HR, marketing and R&D had to be dissolved and brought together as one team.
The challenge, therefore, was to get Ceat’s purpose, vision and strategy understood by everyone right from the Managing Director to the last man standing across functions. Then you have a new generation of joinees, especially at the senior level, who are really good at their jobs but their experience of working on issues comes from a different way of doing things.
This creates a lot of friction within the organisation but we must work on fresh ideas brought in by these new joinees while absorbing them into TQM. The other big challenge was enhancing the capability of the team.
Today, we talk about data science and engineering which is mostly technology adoption of the same philosophy. Even without that, you will need sharp intellect and tools to analyse the situation, find the root cause and then address it to improve customer experience and company performance.
Nowadays, there is a lot of data to work with but this was not the case 10 years back. Data engineering and science solve customer problems more efficiently.
What are the benefits accruing to the overall functioning of an organisation?
The biggest benefit is alignment. Everyone in the company is looking at one vision and following one set of strategies. Some nuances change, some emphasis changes, something speeds up or slows down when new bosses come in but the direction, goal and capabilities remain the same.
Another outcome is that we place a lot of emphasis on grooming internal talent so that there is continuity, especially at the senior level where we want people within the organisation to be groomed. The other benefit relates to enhanced feedback loop systems from the customer to company.
We may not be the best company in the world but listen the most and have the humility to accept our mistakes and improve. If a customer complains to us, it is a great advantage as we get to know what the problem is. However, when they do not complain and switch to competitive products that would be a terrible situation.
We also listen to social media, incoming call-centre calls and organise surveys with the senior leadership also visiting customers to get insights and solve problems. All these TQM practices have helped us reduce the development cycle time of our products as well as their cost.
We are ready to release one for the American market later this year or early 2024. We are not sure if it will succeed but all these practices have increased the probability (of success).
These are some benefits of TQM which result in better market share and margins as well as better business fundamentals which will lead to better stakeholder wealth. We also have very clear goals on sustainability and will contribute towards making this planet safer.
How has technology played a role in the effort towards TQM?
Of late, technology has been a big part of TQM. After the first Deming awards in 2017, we were at a very rudimentary stage of technology utilisation but this really accelerated during the pandemic. We also received the Lighthouse Certification for our Halol plant in Gujarat thanks to the use of IoT, sensors and a lot of data analysis in Industry 4.0 applications.
There were a lot of problems, which we were not even aware of, solved with these technological advancements. We have reduced our energy and water consumption, enhanced productivity and use of equipment as well as manpower productivity while cutting down on cycle time of training new workers.
The old way of working in sales, which was about selling and order taking, has changed and all the communication is done through digital and mobile channels. The value-added part of the job has gone up significantly with technology while we have also been working towards human error prevention.
What would you tell other companies that are keen on getting the Deming?
Each company has its own quality system and not getting a Deming does not mean that you do not have a sound system in place. Deming s a wonderful enjoyable journey for most parts of the time, and there is immense learning, humility and listening power that gets enhanced. There is immense joy in working together as one company, one unit and one team. So, I think it's worth the effort.
Also Read