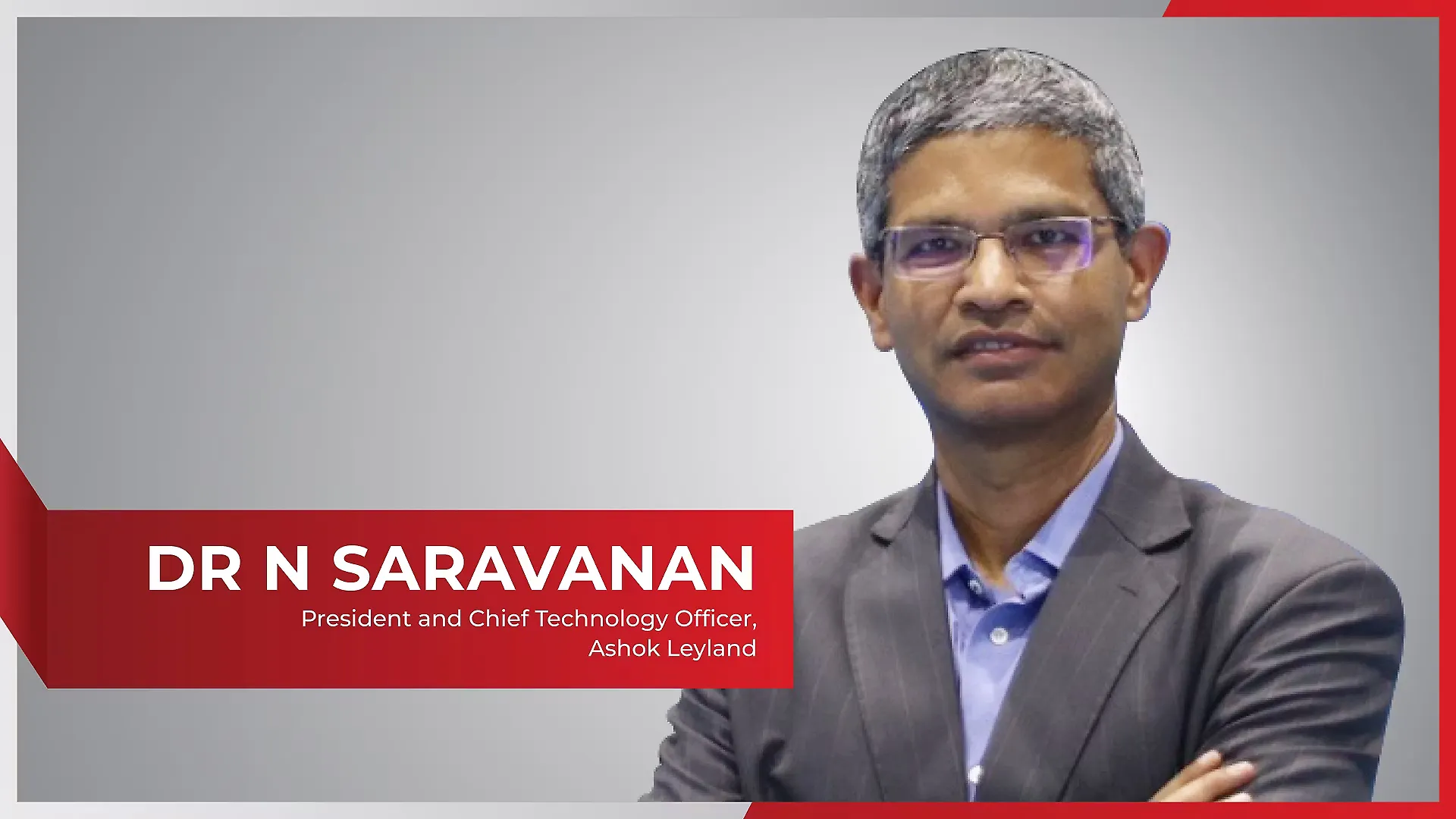
Dr N Saravanan, President & Chief Technology Officer, Ashok Leyland has rich experience in vehicle engineering, verification and validation. After a two-year assignment in 2011 as CEO of Nissan Ashok Leyland Technologies, where he oversaw the LCV development of the JV, he took over as Head of Engineering at Ashok Leyland in 2013. He later became the Head of Product Development and is currently the Chief Technology Officer. He has over 20 publications to his credit and serves on the board of many industry bodies in the areas of safety, regulations and emissions.
What are the new technologies that Ashok Leland is readying towards commercialisation?
We are trying to demonstrate various technologies relevant to the commercial vehicle sector because there is no single path to decarbonising the transport sector, especially the heavy-duty segment, using CNG, LNG and other fuels. There is, of course, some applications where battery electric vehicle and hydrogen could play a role.
There are two possible options within hydrogen: fuel cell and ICE hydrogen. We have the entire range available and will be ready when the market shifts to newer technologies. Even though the hydrogen IC engine that we have is powering a 41-tonne GVW (gross vehicle weight) proto platform, the same powertrain, with some tweaks, can easily replace any other GVW configuration. Of course, the challenge remains, especially on the infrastructure. That is the inherent challenge in the technology space.
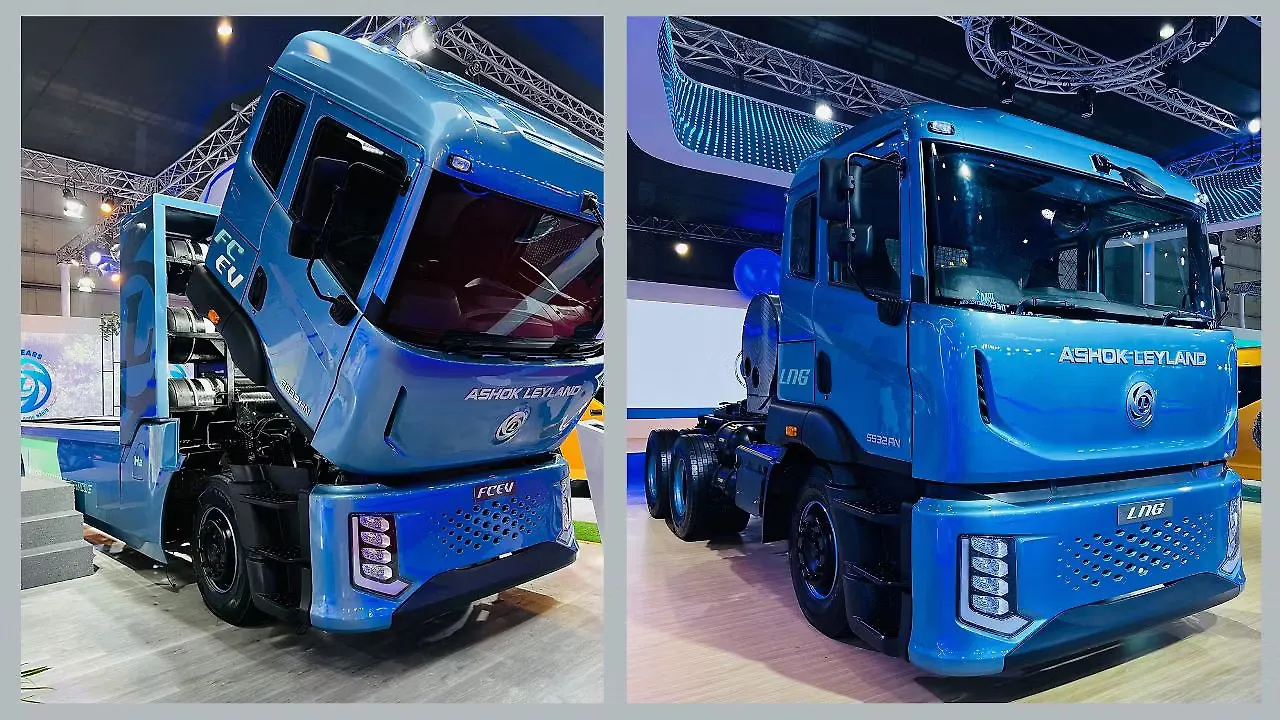
Can you elaborate on your initiatives in hydrogen?
We are exploring both options. We have seen much visibility on hydrogen during the last year and a half. Even in Europe, where they primarily looked at the fuel cell and not hydrogen ICE, some OEMs are looking at hydrogen ICE as a viable alternative.
There are probable applications that are perhaps more robust than fuel cells, because it is less sensitive to the quality of hydrogen, abuse in Indian conditions and more friendly even from the perception of the customers. So we believe that hydrogen ICE, if developed and executed, could play a role.
NOX is part of the exhaust from the combustion of ICE hydrogen. Is it manageable?
Compared to fuel cell engines, there will be some NOX in hydrogen ICE, but it is significantly less than in diesel engines. So it is a question of what you want to trade off.
Do you see hydrogen ICE technology leading the transitioning to fuel cell?
Difficult to say, but fuel cell technology might not come to India. Fuel cell, in one sense, is the most technically advanced, as it has fuel cell along with battery electric vehicle technologies. Whereas in the case of hydrogen ICE, it is the conventional ICE engines with hydrogen tanks. Therefore, the complexities are less. In some regions, the fuel cell may not hit the high volumes. It is too early to say though.
Do you see faster progression of Hydrogen ICE for vehicle makers?
Technically speaking, fuel cell is more advanced. Even though it is not proven for high volume, people have been working on this technology for about 50 years with many prototypes running. However, there is not a single hydrogen ICE truck running now. I think Toyota is running a couple of prototypes.
Do you see the possibilities of making a hydrogen ICE engine, like OEMs converted the core diesel engine to a CNG engine?
From that perspective, yes; it is an easier route for us. Typically, the diesel engine that burns lean, ends up having VGT – Variable Geometry Turbochargers – for extra air. As hydrogen requires a low-energy ignition, it needs a different ignition coil. Similarly, it needs different injectors due to the properties of the gaseous fuel. Besides, crankcase evacuation is required.
Overall, there will be a few modifications needed. This will be Gen-1. In the long term, technology will be towards direct injection to get the right efficiency.
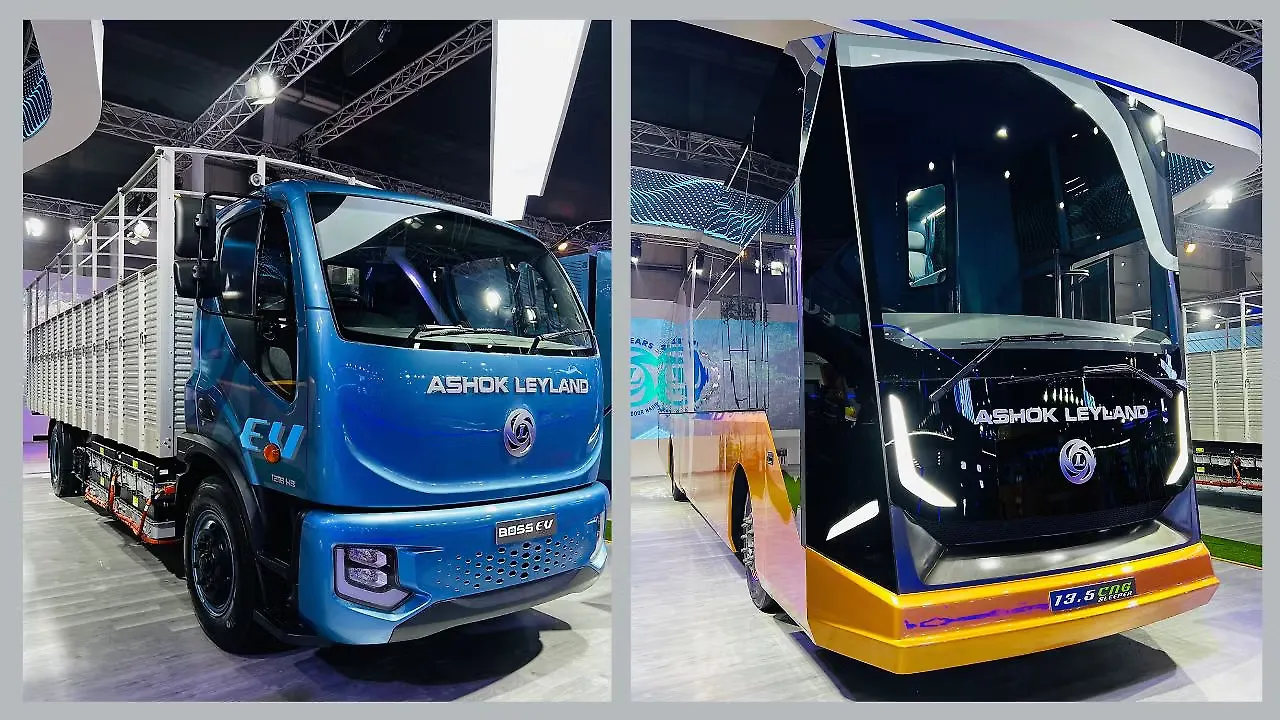
Do you see challenges in developing these intricate systems and technologies?
Yes, we will have to keep in mind the safe handling of hydrogen per se during combustion, fuel distribution from the tank to the combustion chamber, etc. There could be possibilities of embrittlement (a significant decrease in ductility of a material, which makes the material brittle) and this has to be studied. It will take some time to achieve the right level of power and torque.
You have the prototype ready for hydrogen ICE. When do you intend to begin testing?
The testing will start in a couple of months and the refinement will take about 18 to 24 months to make it into production form.
What is the progress on the Swirl Mesh Lean Direct injection technology to support hybrid EVs?
This is more of a research project as we look at multiple ways to develop technologies.
Can you update us on the MoU that Ashok Leyland has with Libertine Holdings PLC for Linear Generator technology?
It is currently in technology readiness levels (TRL) 1 or 2. We are looking at its opposed-piston design (instead of a crankcase at the bottom of the engine) with many electronic controls. The idea is to have a variable compression ratio that allows going with multiple fuels. There is a long way to go.
Opposed-piston technology is decades old and used in a few military applications including battle tanks. Do you see the relevance for this technology now?
More than relevance, it allows us to learn new technology and look at some options. We may miss the bigger picture if we see it as irrelevant. By learning its operations, including the variable compression ratio and the electronics, I am sure there are applications elsewhere.
Do you see the possibility of burning hydrogen in an opposed-piston engine?
Theoretically, it is possible. The engine can burn any fuel – hydrogen and hydrogen-CNG combined – but it has to be proven.
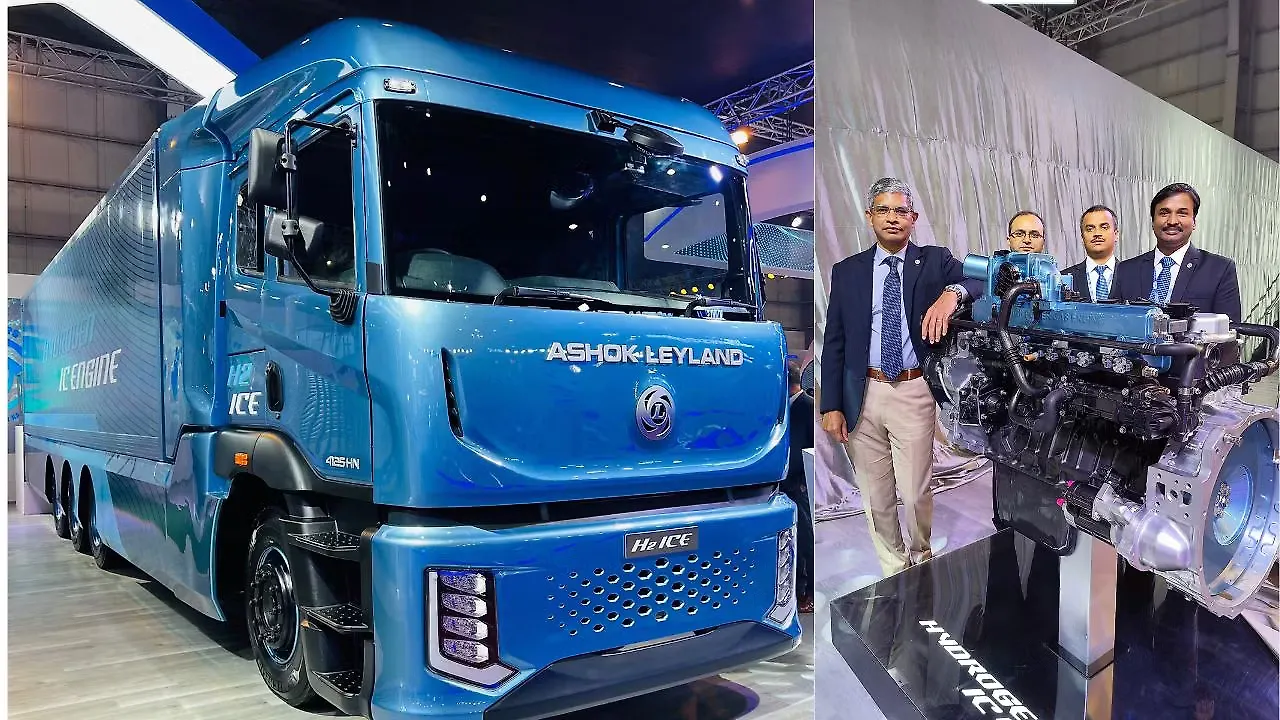
Coming to EVs, what are the options that Ashok Leyland has?
Buses are already established, with LCVs coming in next. After that, I see ICVs getting electrified, especially the BOSS platform being one option. However, there are possibilities in pockets of MHCV trucks, especially in terminal tractors at ports – those unique vehicles that move containers from ships to the yard. This application seems amenable for electrification, even from the total cost of ownership (TCO) perspective. These trucks have well-defined and short routes, and there is enough time for charging on most days. Besides, there is a push to reduce CO2 emissions around the port.
Similarly, there are large industrial complexes, including refineries, where electric MHCV makes sense. We are seeing pockets of potential adoption of EVs. The question is how do we take the idea forward, get the right TCO and, more importantly, execute the projects.
How do you plan to augment your R&D to take up futuristic technologies?
Regarding IC engines, which can evolve by burning different fuels – be it diesel, CNG, LPG or hydrogen – we have converted the engine R&D in Hosur to a research centre for IC engines burning primarily gaseous fuels. We have deployed all the safety systems and relevant approvals to develop and test, including hydrogen and other liquid fuels, such as ethanol, etc.
At the tech centre in Vellivoyalchavadi, near Chennai, we have set up an Advanced Engineering group to look at technology from a vehicle perspective – on how advanced powertrain will fit in the vehicles. Secondly, it will work on non-IC aggregates that would go into new powertrains such as EVs, and fuel cells, especially starting with common aggregates such as motors, power electronics, battery packs and such things. So that is how we are structuring it.
Also Read: