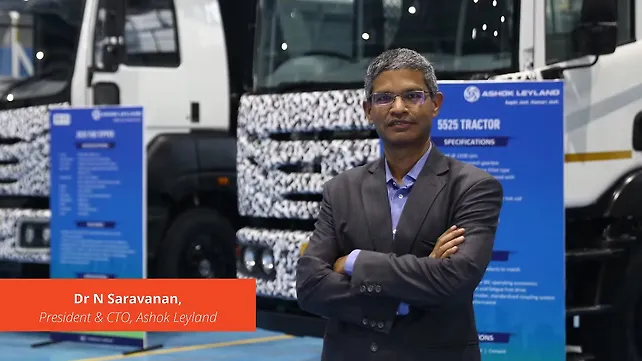
Dr N Saravanan is the President & Chief Technology Officer of Ashok Leyland. As the head of R&D, he leads a team of over 1,500 engineers at Ashok Leyland Technical Centre. He has over 25 years of experience in the automotive industry. Before joining Ashok Leyland, he worked in Ford Motor Company and Intel Corporation.
What is the big thing at Ashok Leyland R&D now?
The big thing is that so many things are going on simultaneously. We were about a 99% diesel powertrain company; then, electrification slowly came for the bus, and later LCV moved towards electric. The following 10 years will witness drastic changes coming out of disruption. The period between 2020-2030 is what I call the messy decade. We have to work on many things without knowing the final solution.
Can you throw some light on the technologies that you are working on?
We are working on CNG/ LNG because the government has incentives. However, we cannot ignore electrification, at least in the lower tonnage vehicles. At the same time, there is a push now towards hydrogen, both driven by some incentives and due to a few prominent ecosystem players looking at hydrogen as a fuel. Then there is a bit more challenge on fuel economy/ CO2 norms. In addition, the government is also pushing on ethanol.
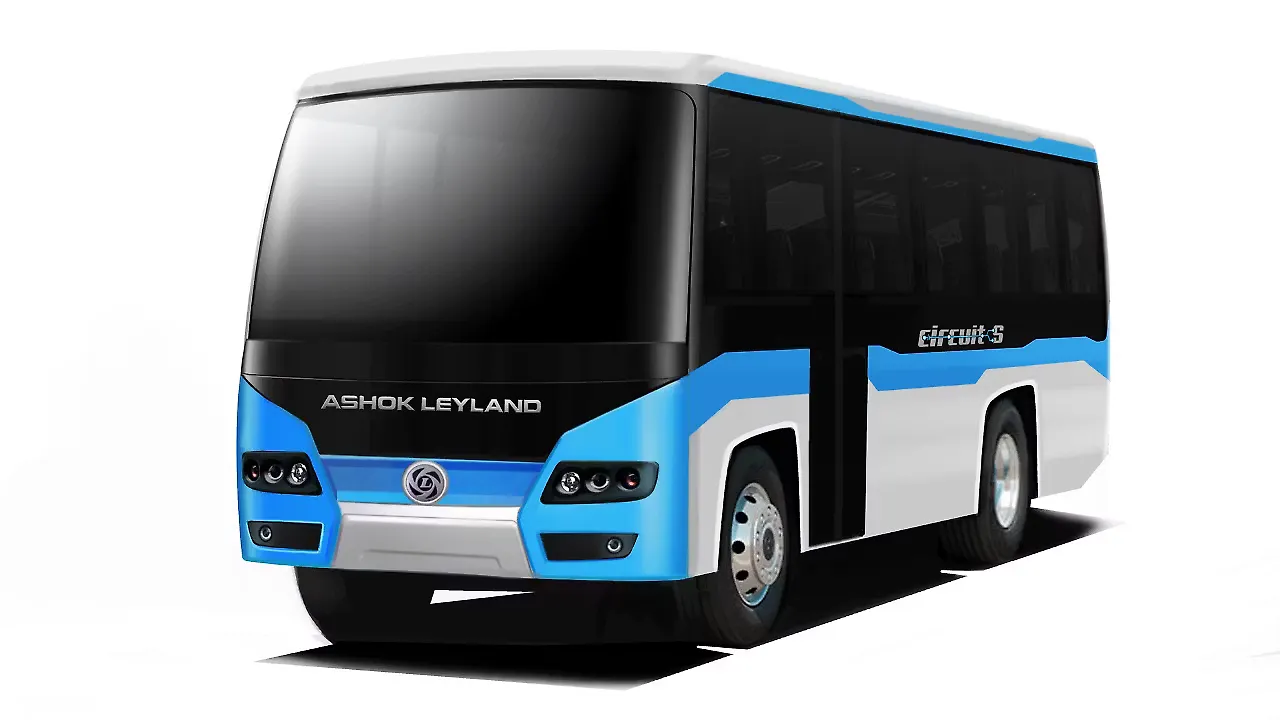
The technology has not stabilised yet. How do we work on all these technologies at the same time, be able to focus and deliver is the biggest question? It is easier if change happens in just one segment.
So that means you have to drive without a proper direction, right?
Yes, we cannot expect any direction as there are many things in the market, including policies, individual companies' ambition to be CO2 neutral, customers' requirements, etc. It is not fair to expect somebody to give a roadmap. So we have to figure out where we see the market going and how we can be flexible and develop solutions. We can develop all these maybe with partnerships.
The big project Ashok Leyland pursued for quite some time was the modular platform. Do you see a vacuum after that?
There is no vacuum. As we start looking at multiple powertrain options, we begin realising the full potential of the modular platform. For example, we can take the diesel-based modular platform, and with minimal changes, we can build an alternate powertrain platform with CNG or LNG or fuel cell, and with a little bit of changes, we can make a hydrogen ICE.
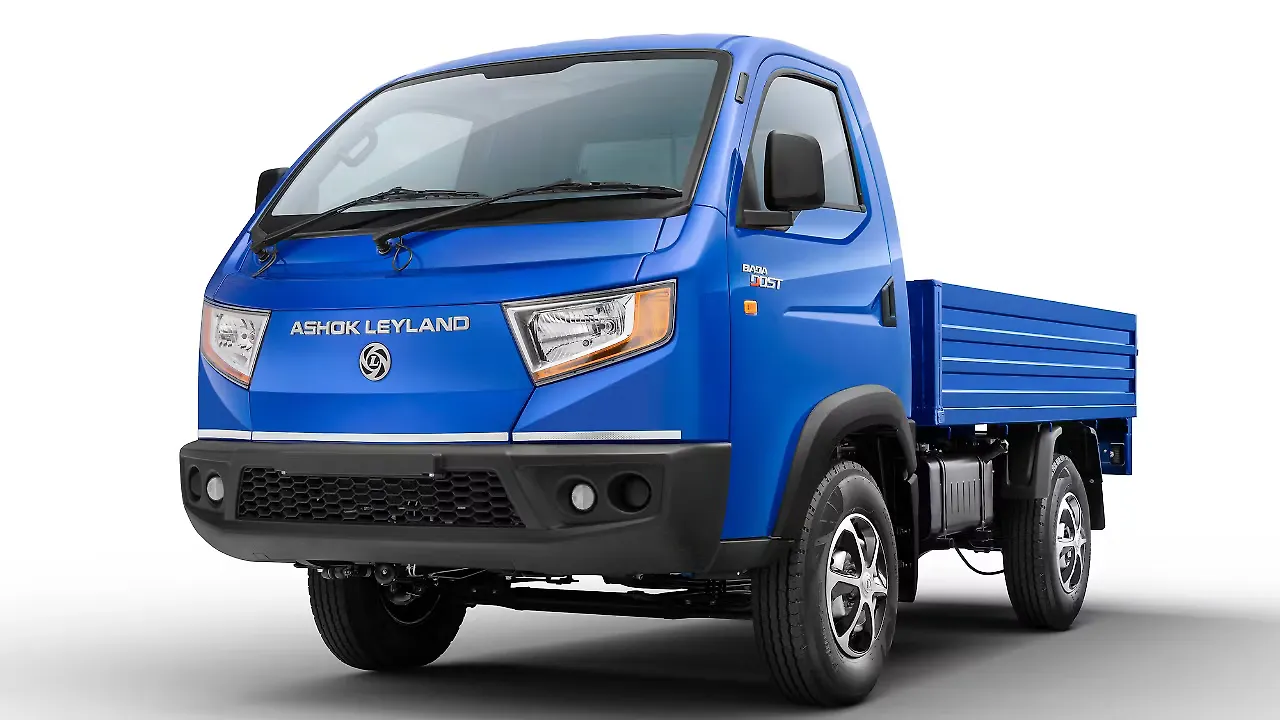
We can launch models very fast. We can even make some commonalities between CNG and LNG as the same tank space can be reserved. Similarly, we can take up EVs and fuel cell vehicles by reserving battery packs in specific locations. So there are multiple ways of actually extending the modular platform.
Is there a possibility to extend the modular concept for even small commercial vehicles?
The variants are not that many for small commercial vehicles to go modular. We have diesel now and maybe we can have a CNG engine also, but there is not much to be done packaging-wise. We wouldn't worry too much about it.
We have to see if it makes sense for us to have the same platform for EVs GenOne, but we will probably have a specific EV platform in the long term. There is no sense to carry out some of the constraints of diesel into EV space, especially for LCVs. To be successful, we believe that we have to leverage those advantages and have a custom-built EV LCV platform, which will happen.
Commercial vehicles will have to comply with the OBD-2 from April 2023. So, is there any special preparation required?
The next level of BS-VI is tightening around the margins and norms, and also, the confirmatory factor comes into play. More than hardware change, it will be a lot in software and calibration. It is necessary to ensure many physical testing are carried out to get the right calibration threshold limits.
Does it mean that endurance tests, in the future, should be even more robust?
Yes, it should be quite robust. Here's where our EGR+SCR strategy helps as it gives a little bit more margin in terms of emission limits. In the case of pure SCR, the catalyst has to operate at very high efficiencies. The bigger challenge is in-field practices. It may not be likely that every customer follows the service interval requirements regularly and can take care of the vehicle. So, discipline has to come in. If somebody picks the vehicle randomly that is not being serviced, there will be challenges. I think it's going to be a learning experience.
Do you think the timeframe given by the government is sufficient for the field trials?
The government has notified this along with BS-VI regulation, and therefore, there is no room for requesting an extension. The industry knew that, but it did not expect COVID; therefore, the investment recovery of the BS-VI itself has not happened. Instead, we lost about 30-40% of volumes. So, there is additional spending on top of that.
There is also talks on moving towards CNG. So, it's in that sense that there's almost no time for the OEMs to recover their investments from BS-IV to VI, though the development was done in three years. Generally, we don't recover large investments in three years. Then, OBD-2 has already come. So, we are constantly, maybe in red, in terms of recurring investments.
And now we have to work on fuel cell hydrogen ICE gas engines and electrification, so that's a challenge. That is why the industry is asking for time.
To facilitate TCO improvement and serviceability, OEMs are looking at optimising or replacing mechanical systems with alternatives. What kind of options do you have?
I can look at two ways – one is with the current diesel vehicle with many sensors in the engine, exhaust etc., and we have a telematics unit in every vehicle generating data. We can have more sensors, if needed. However, as we start moving away from diesel, especially into the fuel cell and battery electric vehicles that inherently have a lot of sensors built-in, it makes it more conducive to be able to build digital twins of every vehicle and be able to use that information to look at much more prognostics, to predict failures.
Moreover, there is no need to put sensors everywhere as, for example, we can perform soft-sensing with the existing ones. Utilising sensors in the gearbox, it is possible to calculate the vehicle's payload and check if it is overloaded.
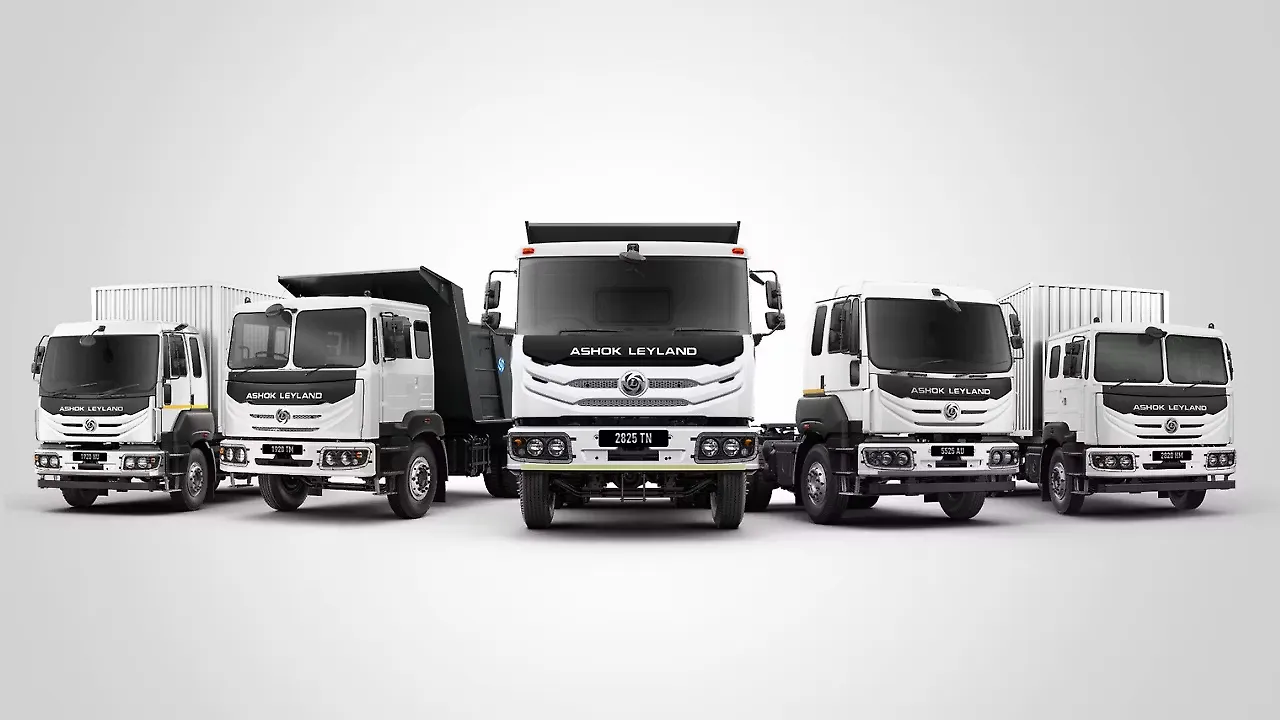
Would this enable OEMs to dictate terms for a warranty issue? Do you see a scenario coming?
That is more to do with the approach to dealing with a customer. I don't think we will have that kind of black and white policy in India. It is always goodwill. We can now internally understand how much the goodwill is and how much is on the warranty, but I think it is possible to tighten over time. I am not sure.
What is your vision, especially for Leyland's R&D wing when it comes to product development, testing and delivering it?
If you look at it, we are one of the few OEMs in the commercial vehicle space, which is self-sufficient in technology.
My vision is that as we move towards new technologies, we want to, at least in the key areas, add value, and have as much technology contribution as we can so that we can differentiate. We want to differentiate our products even in new technology space, including fuel cell or hydrogen, but not just buy and package. We do not want to be an integrator. We want to differentiate where we think we can and that I think is my vision. Still, be the differentiated player in the market.