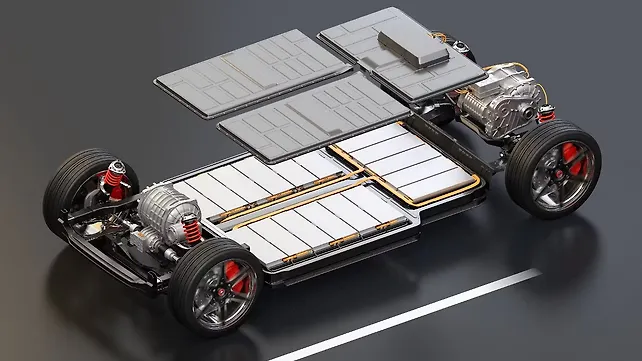
Weight management is a critical aspect in mobility and even more, in e-mobility. Optimising weight is a primary & founding aspect in enhancing energy efficiency and range of the vehicle. This requires an amalgamation of end-to-end processes and techniques that introduces a mindset open to alternate materials that are lighter, offer same or better performance, robustness & reliability, affordable for mass-market applications and have better recyclability.
In tandem, there is a need to review the current components and systems for weight optimisation opportunities. The obvious benefits of optimised weight are being able to offer better fuel economy, lower the wear & tear of components, better endurance, lower cost of ownership, responsible use of natural resources and vehicle longevity.
Overwhelming Material Innovations
The escalation of weight watching in the mobility industry has been rapid in the last few decades. In the mid-90s, the US Department of Energy (DoE) funded a 50-50 cost share programme with the then ‘Big 3’ – General Motors, Ford and Daimler Chrysler – to build mid-size passenger vehicles that were about 2,000 lbs, or approximately 907 kg.
Materials ranging from magnesium, composites, plastics, jute, wood dust, titanium, aluminium, metal matrix alloys, conventional steel and carbon fibre were used in various vehicle systems and body panels. The material innovations to build these drivable technology demonstrators were mind-boggling.
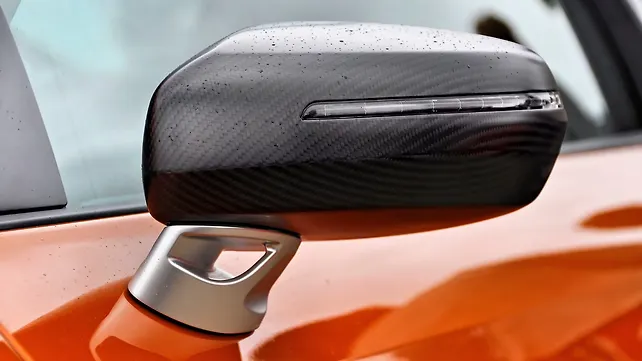
The intent of the DoE funded programme was to be able to implement nuggets of these innovative material and manufacturing technologies and transversely deploy as many as of these in mass-market applications. In parallel, stimulate the vendor base, as well as the supply chain, recyclability avenues and nurture them for a sustainable environment.
Fast forward 30 years, many of these materials exist in vehicle platforms across different target segments worldwide.
A unique aspect of EVs is that the weight has moved from under the hood as in a conventional vehicle to other sections of the vehicle. This changes the weight distribution, driving dynamics, occupant safety and many other attributes. The components’ transition requires revisiting vehicle development strategies with a newer manufacturing mindset, tools, software, styling, skill-sets and end-to-end vehicle development.
The other intriguing aspect is that the fuel in the tank of a conventional vehicle is in a dynamic state, when it is full versus when it is receding as the vehicle consumes the same during driving. Whereas in an EV the weight of energy storage systems remains constant. This changes the approach to choice of materials in vehicle development.
Ingenious Mindset For Weight Management
The weight and size of the energy storage system depends on the vehicle platform, chemistry of cells or energy source, pre-defined driving range and cost to the customer. Additionally, weight of wiring harnesses could be between 50 and 400 kg, depending on the vehicle platforms. This entails an ingenious mindset for weight management options.
Sometimes, light weighting to a consumer may appear to send a negative connotation. The consumer may perceive a loss in offering due to light weighting and possibly a reduction in value or performance to them. In reality, the efforts and results to optimise weight offer a better value proposition to a consumer. It is the mobility stakeholders’ responsibility to bring awareness to consumers and launch appropriate programmes.
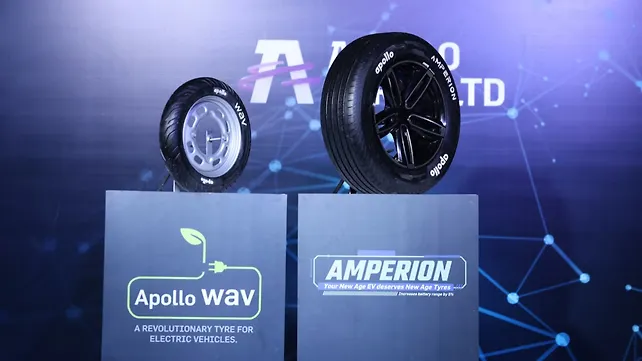
Tyre industry, like other mobility partners, is playing a key role in weight optimisation for e-mobility. The capacity to carry additional load, offset battery weight and optimise the weight distribution is possible by lighter tyres. Tyre technology has advanced to provide a balance of better or equal rolling resistance and/or wear characteristics. The unique EV tyres have many additional advantages and are trending rapidly.
In Conclusion
Weight management in the era of e-mobility warrants an innovative mindset to be able to optimise chassis, suspension, ensure that the vehicle meets the passive and active safety norms, and meet the ability of isolating high voltage, where applicable.
Composites, nanotechnology and reinforced carbon fibre have augmented these newer asks and have made major inroads in EVs. The innovations and research focus, tracked through patents filed in the US, EU and Asia shows a lot more overall investment.
The recipe for sustainability and to a sustainable long-term weight management strategy will be possible through partnership of like-minded stakeholders that include mobility fraternity, investors, academia & research labs, regulators and policy makers, and most importantly the skill-sets.
About the Author: Dr Arun Jaura is the Chief Technology Officer at Hero MotoCorp.