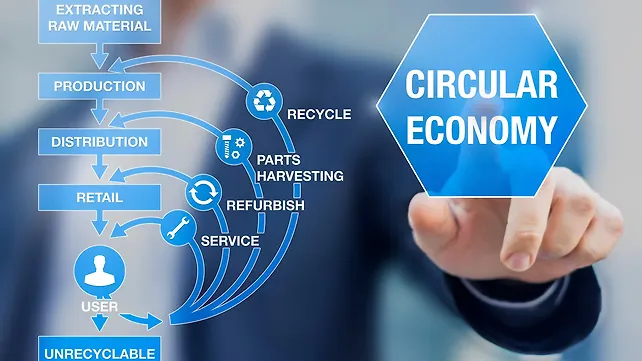
The automotive industry is under mounting pressure to adopt circular economy practices, catalysed by the need to meet decarbonisation imperatives, realise cost-effective and sustainable supply chains, and advance green manufacturing processes.
Unlike traditional, linear economy models, a circular economy seeks to redesign, reduce, reclaim, remanufacture, and reuse components and materials. The aim is to prolong the useful life of products, optimise resource consumption, minimise waste, and make value chains and ecosystems more sustainable.
It is estimated that globally, circular economy initiatives could generate revenues of almost $4.5 trillion by 2030.
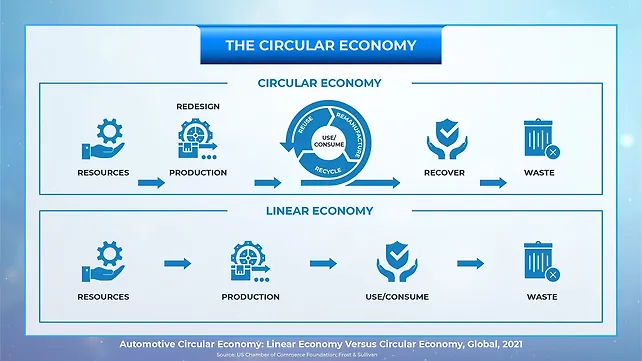
In the automotive industry, circular economy practices are coalescing around four main areas:
- Firstly, remanufacturing, where used components are repaired and then deployed in used cars or sold in the aftermarket.
- Secondly, recycling, where raw materials extracted from used components are utilised in new vehicles and other industries.
- Thirdly, product life extension, where vehicle parts are proactively serviced before they develop any faults, thereby extending their useful life.
- And, fourthly, sustainable material use, where innovative, eco-friendly materials such as bio-plastics are incorporated into new cars.
Leading automakers are embracing such resource responsible trends. For instance, over 2021-2025, Ford intends to use 20% sustainable materials in its vehicles, Volkswagen has committed to halving the carbon emissions per vehicle in all its plants, and Toyota has declared that it will seek a 30% reduction in the global average carbon emissions from its new vehicles, compared to 2010 levels.
Likewise, over 2026-2030, General Motors has stated that it will use 100% renewable energy for vehicles manufactured in the US and reduce factory greenhouse gas emissions by 31%, even as a raft of automakers, including Honda, Nissan, Toyota, Volvo, and Volkswagen, are working to achieve carbon neutrality by 2031-2050.
Remanufacturing
Among the perceived benefits of remanufacturing include the conservation of natural resources, reduced waste, smaller carbon footprint, and lower costs. Remanufactured components also come with quality assurances since they must meet standard factory specifications in terms of performance, reliability, and durability.
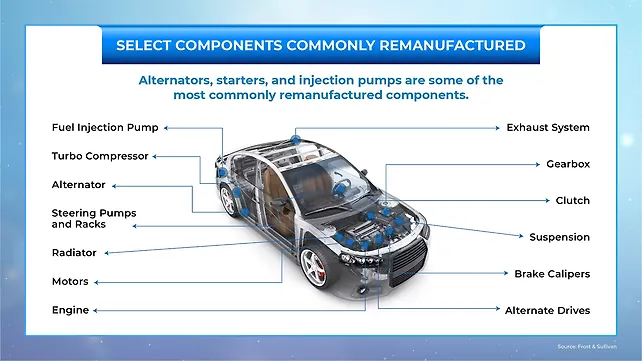
Companies such as ZF, Robert Bosch, Carwood, IM Group, and Valeo are active in this space as are several automakers. For example, Renault announced Europe’s first circular economy factory – the Refactory – focused on mobility. It is built around four pillars: Re-trofit (vehicle life extension), Re-energy (green energy management), Re-cycle (resource management optimisation), and Re-start (accessible innovation).
Recycling
Commonly recycled automotive parts from end-of-life vehicles (ELVs) cover the gamut – from body, seat, engine, window glass, and wheel to bumper, suspension, radiator, coolant, and engine oil. Recycling of plastic, steel, aluminium, and tyres offer a host of environmental benefits.
For example, it is estimated that recycling one kg of aluminium from ELVs will save 14 kWh (kilowatt-hours) of power; recycling steel from ELVs will create energy savings of 2.95 mWh (milliwatt-hours), and recycling four tyres will save approximately 323 pounds (~ 146 kg) of carbon emissions.
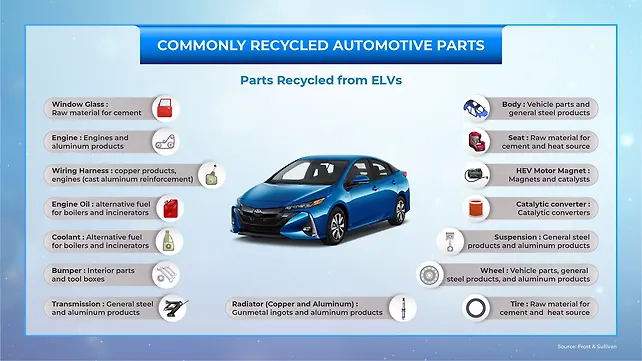
The Toyota Mirai, Audi eTron, Ford F-150, and BMW i3V highlight the use of aluminium recycling. Automakers such as General Motors, Honda, Nissan, Ford, Volkswagen, and Chrysler are involved in plastics recycling. Honda, for instance, makes mud guards and splash guards from recycled scrap bumper, while Chrysler Grand Cherokee has seats made of recycled polyurethane foam plastic.
Steel is almost 100% recyclable, and most car bodies today contain approximately 25% recycled steel. Many companies are now assessing green steel – a more sustainable way to manufacture steel compared to traditional methods. Mercedes-Benz is collaborating with H2 Green Steel and Volvo with SSAB AB to produce green steel cars by 2025. While promising, high costs mean that until economies of scale are achieved, green steel use will remain restricted to the premium segment.
Companies such as Wastefront, Bridgestone, and Michelin are showcasing innovative approaches to tyre recycling. For example, Bridgestone Indonesia in partnership with Soles4Souls Asia will recycle 40,000 EOL tyres into at least 400,000 pairs of shoes for charity by 2022.
Closed loop recycling is a major trend that reduces natural resource usage, pollution, and landfill burden, with the World Economic Forum estimating that this model can save energy consumption by up to 75%. The 2021 Nissan Rogue uses a closed loop recycling strategy for aluminium in the vehicle.
Product Life Extension
From tyre and battery life extension to servicing electronic components and deploying predictive maintenance systems, the focus is on increasing the useful life of the automotive product.
Today, almost 44% of all trucks in North America operate on retreaded tyres. Retreading can extend a tyre’s life by at least 200%, while helping fleets save $3 billion annually in tyre related costs. Continental Tyres India launched the Conti Bharosa warranty programme in July 2021, which offers a 5-year warranty on truck and bus tyres, including the first tyre retreading.
Servicing electronic components instead of discarding them reduces electronic wastes in landfills, with Faurecia being a prominent player in this area. Electric vehicle (EV) battery management systems monitor battery health in real time. For instance, TWAICE, a Germany-based battery health management start-up, works in multiple transportation areas, including passenger cars, trucks, and electric scooters.
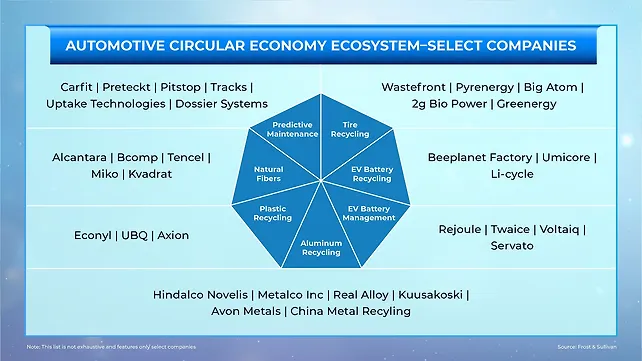
Poor vehicle maintenance costs North America 1.2 billion tons of excess CO2 emissions. Predictive maintenance systems (PMS) perform remote diagnostics to detect component faults before they happen and predict the need for repairs. Canada-based PMS start-up Pitstop counts General Motors, Ford, and several independent dealerships and auto shops among its clients.
In the field of battery diagnostics, companies such as ReJoule provide rapid diagnostic testing for EV batteries entering second-life applications. Repurposing EOL batteries for secondary applications, such as stationary energy storage systems is another significant focus area.
Volvo with its plug-in hybrids, Renault with the Zoe, Nissan with the Leaf, and General Motors with the Chevrolet Volt are among several automakers who are testing EOL batteries from their EVs for stationary energy storage applications to power charging stations, convenience stores, and entire communities.
Companies such as Sweden-based BatteryLoop are manufacturing energy storage systems using second-life batteries from EVs, while Spanish company BeePlanet Factory refurbishes and reuses EOL lithium-ion EV batteries, repurposing them into stationary energy storage systems.
Sustainable Materials
The past decade has seen a distinct movement toward the use of renewable, eco-friendly materials in cars. A host of futuristic, sustainable options are being assessed: leather alternatives like recyclable polyester microfiber (Dinamica), vegan leather made from discarded grape skins and seeds from vineyards (Vegea), plastic alternatives such as compressed wood composites (Karuun), and natural fibre alternatives (Amplitex) to carbon fibre.
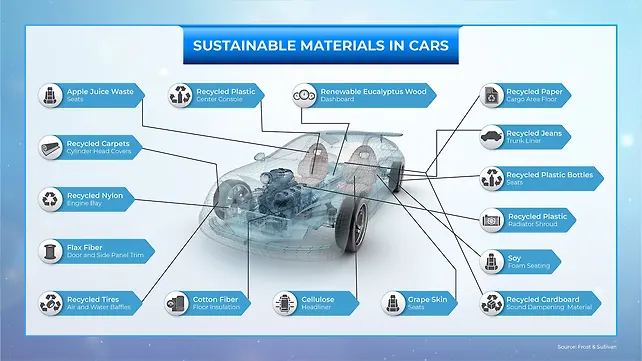
Conclusion
Circular economy concepts are now being evidenced not just in manufacturing processes but in vehicles themselves. For instance, more than 25% of the plastics in the BMW i3’s interior use recycled plastics and renewable raw materials. The Mercedes-Benz S-Class uses plastic recyclates in more than 120 components. Over 60% of the Nissan Leaf’s interior incorporates recycled materials, mainly from recycled PET bottles. Hyundai has developed the interiors of the Ioniq 5 from sustainable materials, textiles, bio-paints, and natural/ recycled fibres.
Going forward, government regulations such as the ELV in Europe and the vehicle scrappage policy in India will play a key role in promoting decarbonisation, sustainable agendas, and driving the circular economy.
The creation of organised scrapyard markets, particularly in countries such as India, exploring new revenue streams by repurposing EOL batteries for second life applications, and investments in eco-friendly sustainable materials will accelerate and strengthen the circular economy in the automotive industry.
About the Author: Sujith Unnikrishnan is a Senior Research Analyst, Mobility – Business Strategy and Innovation Group at Frost & Sullivan. He has more than 5 years of automotive strategy research experience and has worked on 20+ mobility assignments engaging with global automotive industry experts. His expertise lies in strategic planning, trend analysis, business model analysis, forecasting, company profiling, and market analysis. He is a core team member with Frost & Sullivan’s Mobility Business Model services and works with BSIG (Business Strategy and Innovation Group) research arm. He holds bachelor’s degree in Mechanical engineering from SRM University, Chennai.
Also Read:
Manufacturing Sector Will Catalyse Indian Economy, GDP Growth
GKN Automotive Joins SCREAM To Develop Circular Supply Chain For Recycled Rare-earth Magnets
Emission-reduction Initiatives Should Not Affect Fuel Economy: Dr Ameya Joshi